Since its opening in 2014, the new Ultra-Low Vibration Lab (ULVL) at the University of Michigan has already achieved two key scientific milestones: Quantifying heat fluxes at the nanoscale; and showing that light emitting diodes (LEDs) can be employed to cool electronic devices.
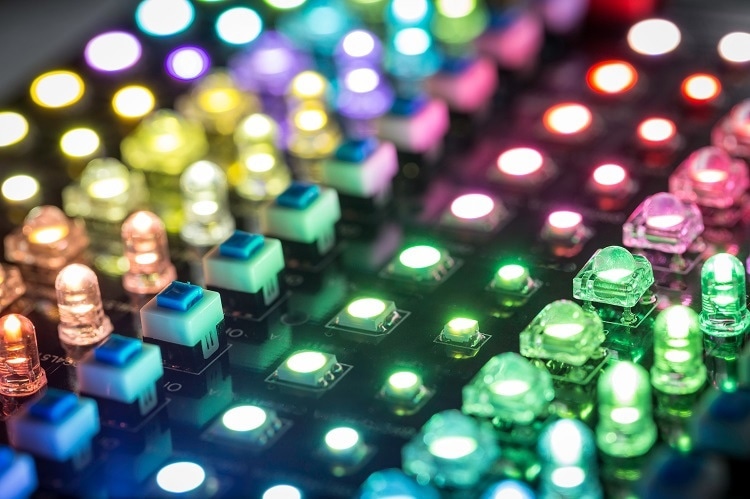
Image Credit: NV77/shutterstock.com
ULVL’s Negative-Stiffness vibration isolation platforms, engineered by Minus K Technology, assisted in these discoveries. They have provided record low vibration levels in every ULVL chamber, varying from VC-K to VC-M at frequencies higher than 2.5 Hz.
The recently opened Center of Excellence in Nano Mechanical Science and Engineering (NAMSE) houses the Ultra Low Vibration Lab. The facility is the latest development within the G.G. Brown Laboratories, located in Ann Arbor on the North Campus of the University of Michigan.
The previous Associate Chair for Facilities and Planning with the Department of Mechanical Engineering, Noel Perkins, explains this development as a ‘building-within-a-building’.
Found on the ground floor, the Nanoengineering Lab comprises eight ultra-low-vibration chambers for nanoscale metrology, temperature, mechanical, and interference investigations.
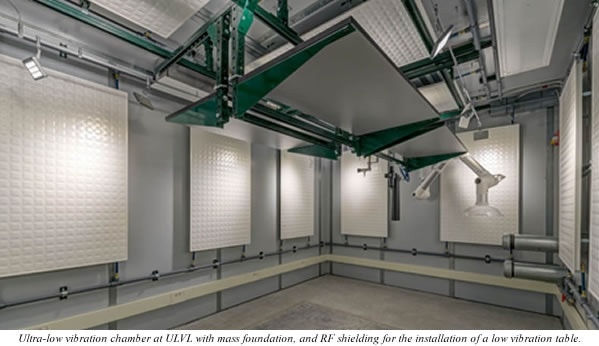
Image Credit: University of Michigan
The chambers are structurally separate from the balance of the building. Pillars that constitute an 8 ft (2.4 m) thick seismic mass, which is distinct from the floor of the chamber, have vibration isolation tables connected to them. Even the footsteps of researchers will not interrupt investigations.
With the emergence of nanotechnology and nanoengineering of the last two decades, a relatively small number of institutions and agencies have been able to construct facilities for ultra-sensitive measurements, and I know of none that are focused on the mission of a mechanical engineering department.
Edgar Meyhofer, Professor of Mechanical Engineering and Biomedical Engineering, University of Michigan
Meyhofer, in collaboration with Pramod Reddy, a Professor of Mechanical Engineering, and Materials Science and Engineering at the University of Michigan, have been working together on nanoscale heat transfer, biomechanics research, and energy transduction.
The Nanostructures Lab is being used by other researchers to construct artificial neurons for advanced computers and artificial platelet cells for medical applications.
The smallest forces are investigated at the University’s Microdynamics Lab, using computational models that explain the mechanics of protein assemblies and DNA, along with the behavior of viruses.
Fluctuational Electrodynamics
When heat moves between two disconnected objects, it travels differently at the tiniest scales. These are distances on the order of 1/50,000 of a human hair or the diameter of DNA. As an example, heat is emitted 10,000 times quicker at the nanoscale.
For decades, researchers have known about this phenomenon, but they have not established the reasons behind the process. At ULVL, researchers have now analyzed how heat is emitted in a vacuum from one surface to another at distances as low as 2 nm.
We've shown for the first time, the dramatic enhancements of radiative heat fluxes in the extreme near-field. Our experiments and calculations imply that heat flows several orders of magnitude faster in these ultra-small gaps.
Pramod Reddy, Professor of Mechanical Engineering, and Materials Science and Engineering, University of Michigan
The Russian radio physicist, Sergei Rytov, in the mid-20th century, offered a new theory named ‘fluctuational electrodynamics’ to outline heat transfer occurring at distances smaller than 10-micrometers. Investigations since that time have not always materialized in supporting evidence.
“Experiments were undertaken in the 1990s and early 2000s that tried to test these ideas further, and they found large discrepancies between what theory would predict and what their experiments revealed,” Meyhofer described.
The researchers have stated that their results close the case, and prove that Rytov was correct, due to the advanced nature of the new laboratory at the University of Michigan.
Custom Low-Vibration Chamber
The ULVL chamber was tailor-made to execute nanoscale experiments. They are so accurate that they are reactive to the lightest footsteps.
In the chamber, the vibration isolation system comprises seismic mass and an advanced low-vibration table, which decreases external vibrations, and internally reduces the mechanical vibrations related to cooling and heating systems, or elevators.
The chamber restricts acoustic noise, changes in humidity and temperature, along with radio frequency and magnetic interference.
“Our facility represents the true state-of-the-art,” stated Meyhofer, “When creating nanoscale gaps, such as those required for our nanoscale heat radiation experiments, the slightest perturbation can ruin an experiment.”
In the chamber, the researchers utilized custom-made ‘scanning thermal microscopy probes’ that enabled them to directly study how efficiently heat travels between two surfaces of gold, silica, and silicon nitride.
The researchers selected these materials as they are frequently employed in nanotechnology.
One sample (the planar substrate) was provided for each material that would be heated to 305 °F.
They covered the tip with the same material using a probe, but ensured its connection at the base to a thermal reservoir that was kept at a cooler temperature of 98 °F.
The probe and the sample were moved at a slow pace, simultaneously, in small steps, starting at 50 nanometers until they were touching. The temperature of the tip was analyzed at frequent distances (gaps) ranging from 2 nm and 50 nm.
The researchers found that the cause of the fast heat transfer was the overlap of the two surfaces’ sides, and evanescent waves, both of which generate heat. This process can be observed in nanoscale gaps.
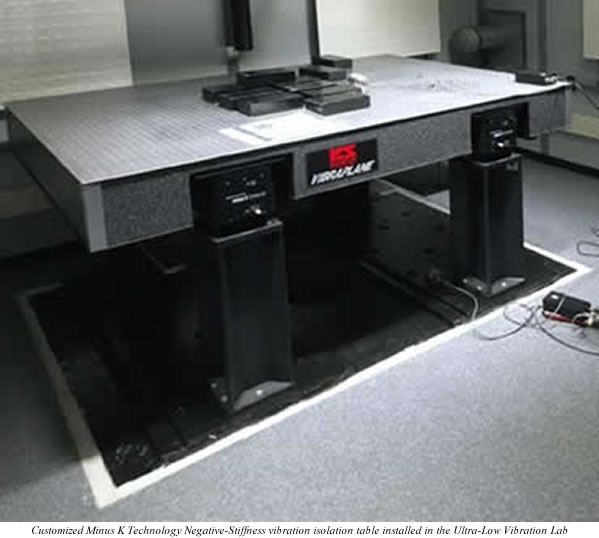
Image Credit: Colin Gordon Associates
“These waves reach only a small distance into the gap between materials,” explained Bai Song, a previous graduate student in mechanical engineering and one of the primary authors.
Song added, “And their intensity at the extreme near-field is enormous compared to the electromagnetic waves at larger distances. When these waves from the two different devices overlap, that is when they allow tremendous heat flux.”
Cooling Supercomputers with Heat-Absorbing LEDs
LEDs with electrodes can reverse-cool adjoining devices only several nanometers away.
This technique could result in contemporary solid-state technology for the microprocessors of the future, which will have so many transistors fitting into small spaces where modern techniques will be unable to remove heat efficiently enough.
"We have demonstrated a second method for using photons to cool devices," explained Reddy, who co-led this research with Meyhofer, "The LED, with this reverse bias trick, behaves as if it were at a lower temperature."
It is highly complex to measure this cooling and verify that something of interest has happened.
To get an adequate amount of infrared light to travel from an object into the LED, the two would have to be very near to each other, less than one wavelength of infrared light.
This is essential to benefit from the evanescent coupling or near field effects, which allows a greater amount of infrared photons to travel from the object to be cooled into the LED.
Meyhofer and Reddy had a strength in that they had already been cooling and heating nanoscale devices, positioning them so that they were just several tens of nanometers apart.
A photon, that would not have escaped the cooled object, can travel into the LED at this close proximity, almost as though the gap between them was not present.
The group verified the theory by constructing a minuscule calorimeter, which is a device that quantifies energy variations, and placing it close to a minuscule LED around the size of a grain of rice.
They were always generating and receiving thermal photons from each other and different sources in their surroundings.
"Any object that is at room temperature is emitting light. For example, a night vision camera is basically capturing the infrared light that is coming from a warm body,” Meyhofer stated.
When the LED was reverse-biased, it started to absorb photons from the calorimeter, performing as a very-low temperature object.
The gap simultaneously stopped heat from moving back into the calorimeter through conduction, creating a cooling effect. The team showed cooling of 6 watts per meter squared.
In theory, this technique could create cooling the same as 1000 watts per meter squared, or around the power of sunshine on the surface of the Earth.
Engineering a Solution for the Lab
A vibration survey was performed on the Ultra-Low Vibration Lab chambers once the construction period of the Center of Excellence in NAMSE had finished.
The measurements showed that even when one vehicle was being driven on the street nearby, the vibrations were more than the NIST-A specifications required for the ULVL.
It was essential to have a Vibration Criterion (VC) of NIST-A (1 micro-inch, 1 to 20 Hz; 125 micro-inch from 20 to 100 Hz) to ensure the success of the Ultra-Low Vibration Lab.
The VC specifications were produced in the early 1980s by Colin Gordon and Eric Ungar. They were primarily made for use in the semiconductor industry but have been used in a range of technological applications.
The NIST-A criterion was produced for metrology but has garnered interest from the nanotechnology community.
The suggestions to attain the necessary specifications were managing nearby traffic on the streets near the latest building addition, along with updating the proposed pneumatic vibration isolators on optical tables with Negative-Stiffness isolators, manufactured and designed by Minus K Technology.
The University of Michigan requested 31 customized Minus K Negative-Stiffness vibration isolators with pedestals supplied for the eight Ultra-Low Vibration Lab chambers, along with seven customized tabletops.
Negative-Stiffness isolators use an exclusive and fully mechanical concept in low-frequency vibration isolation.
Compressed air or electricity are not required. There are no pumps, chambers, or motors involved, and no maintenance is necessary as there is nothing that could wear out. They function in a passive fully mechanical mode.
In this vibration isolation system, vertical-motion isolation is provided by a stiff spring that supports a weight load, combined with a Negative-Stiffness mechanism. The net vertical stiffness is made very low without affecting the static load-supporting capability of the spring. Beam-columns connected in series with the vertical-motion isolator provide horizontal motion isolation. A beam-column behaves as a spring combined with a negative-stiffness mechanism.
Dr. David Platus, President, Minus K Technology
The isolator offers 0.5 Hz isolation performance both horizontal and vertical. For an isolation system with a natural frequency of 0.5 Hz, isolation starts at around 0.7 Hz and improves with the increase in the vibration frequency. The natural frequency is more regularly employed to describe the performance of the system.
Negative-stiffness isolators resonate at 0.5 Hz and there is practically no energy found at this frequency.
It would be very rare to discover a significant vibration at 0.5 Hz. Vibrations with frequencies higher than 0.7 Hz (where negative-stiffness isolators start isolating) are quickly attenuated as frequency increases.
Transmissibility with negative-stiffness isolators is significantly improved over air systems. Transmissibility is a measure of the vibrations that are transferred through the isolator in relation to the input vibrations.
When adjusted to 0.5 Hz, the Negative-Stiffness isolators attain a 93%isolation efficiency at 2 Hz; 99% at 5 Hz; and 99.7% at 10 Hz.
Negative-Stiffness isolators offer a very high performance, as quantified by a transmissibility curve.
Record-Low VC-M Level
Colin Gordon Associates (CGA), a globally renowned vibration and acoustics consultant, completed the last vibration survey upon installation of the customized Minus K Negative-Stiffness tables and isolators. They demonstrated the measured vibration levels in all ULVL chambers from VC-K to VC-M at frequencies higher than 2.5 Hz.
Vibration criterion (VC) curves are often utilized in the assessment of the ambient vibration found in facilities.
"VC-M is the lowest we have ever measured, though we weren’t able to measure below 2.5 Hz because our most sensitive sensor won’t go lower, due to sensor noise floor," explained the Vice President of Colin Gordon Associates, Hal Amick.
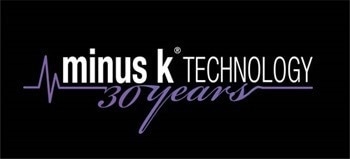
This information has been sourced, reviewed and adapted from materials provided by Minus K Technology.
For more information on this source, please visit Minus K Technology.