Air filters have become increasingly popular on the market as consumers seek to combat harmful particles, including the novel coronavirus. Most contemporary air filters are composed of electrostatically charged silica glass microfibers, but the next generation of air filters will likely feature the inclusion of electrospun nanofibers.
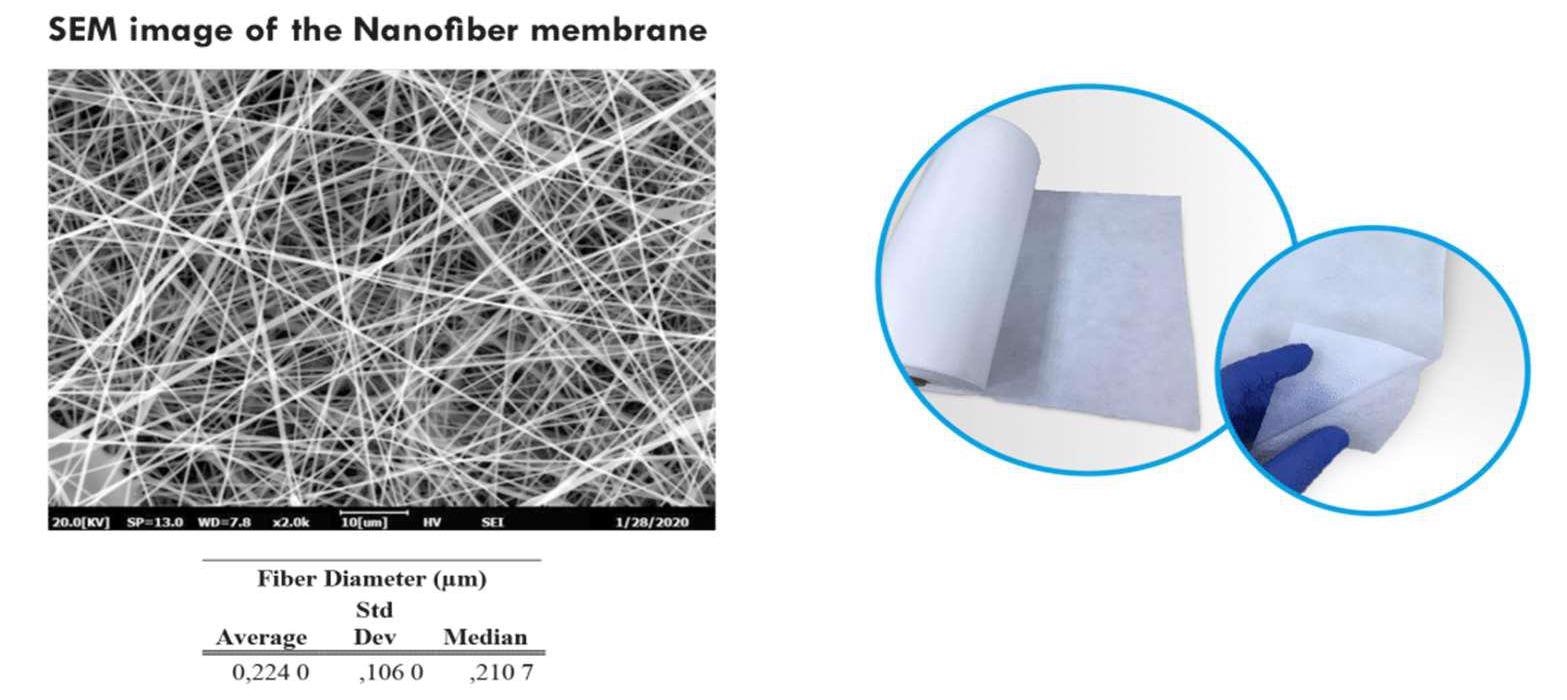
Image Credit: Inovenso
The structure of electrospun nanofibers offers a number of effective properties, and Inovenso employs electrospinning technology in the mass production of nanofiber filters suitable for use in Fine and HEPA filters.
Protection Against Air Pollutants
Ensuring that environments are clean and properly protected against airborne pollutants is becoming more important than ever.
A range of harmful pollutants must be protected against, including various sizes of particulate matter (PM) and very small particles which may enter the lungs and cause damage to a person’s respiratory system.
Various forms of bacteria and viruses are also considered to be advanced particles, and the emergence of the current pandemic has led to increased efforts in the prevention of the COVID-19 virus entering buildings, households and the respiratory tract.
This has become a major concern, prompting scientists to focus their research efforts on improving approaches to filtering out these harmful pollutants.
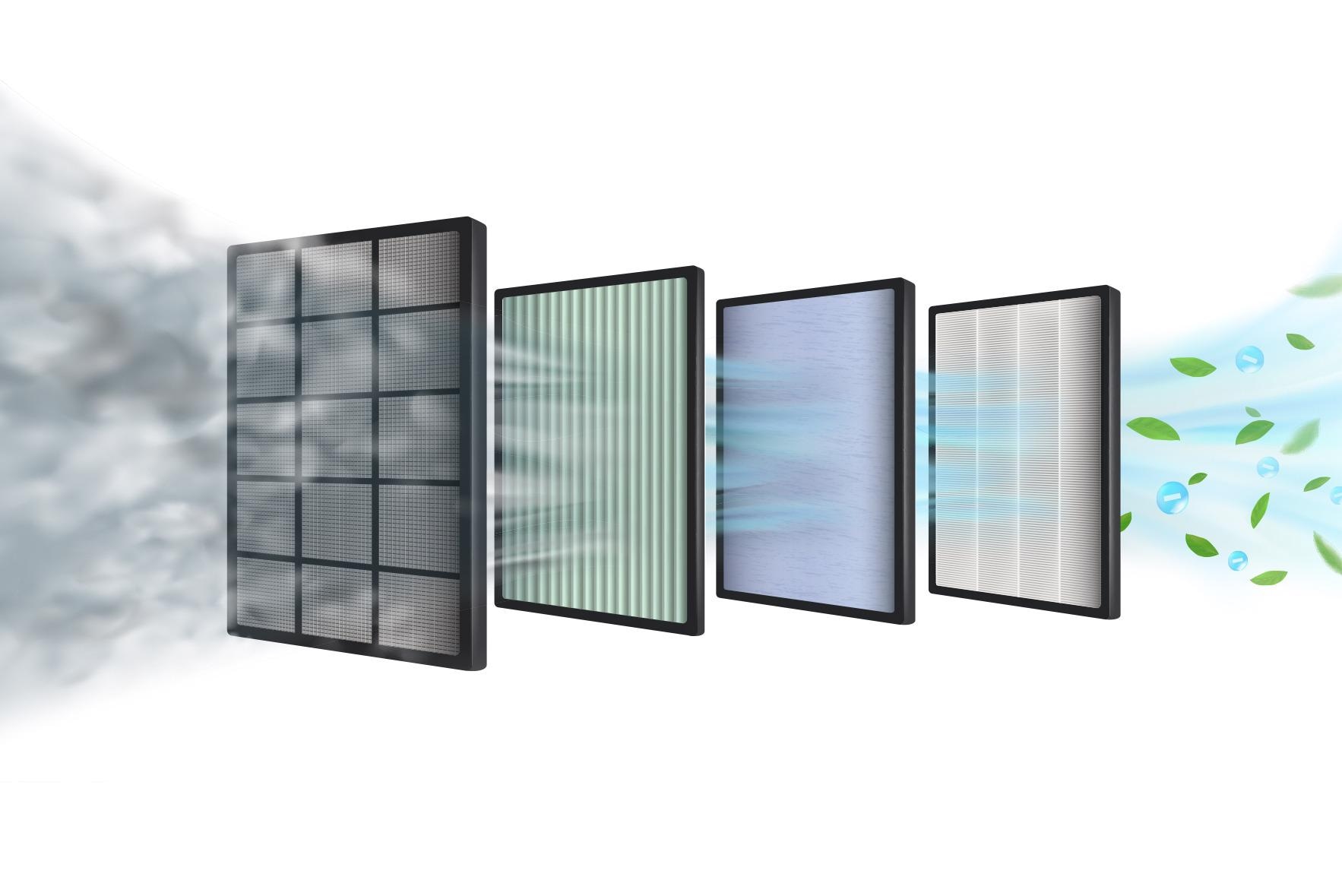
Image Credit: Inovenso
Thankfully, modern filtration technology has become highly effective at decontaminating air and preventing the movement of PMs; for example, current technologies including the line of N95/N99 filtration masks and sophisticated HEPA air filters.
All of these filtration devices feature the same base-line mechanics: layers of extremely fine fibers, functioning as ‘sieves’ and blocking PMs from their trajectory path.
Air Filtration Technology
Fibers employed in existing technologies are generally comprised of synthetic meltblown polymers or glass fibers (SiO2).
Because the majority of these fibers are too large to effectively capture particles mechanically, they are often electrostatically charged in order to increase the attraction of PMs towards the fibers, therefore improving overall filtration efficiency.
Newer generations of filters incorporate nanofibers – fibers with diameters in the nanometer range. These extremely small diameter sizes mean that particles can become trapped by the nanofiber layers without the need to rely on electrostatic attractions.
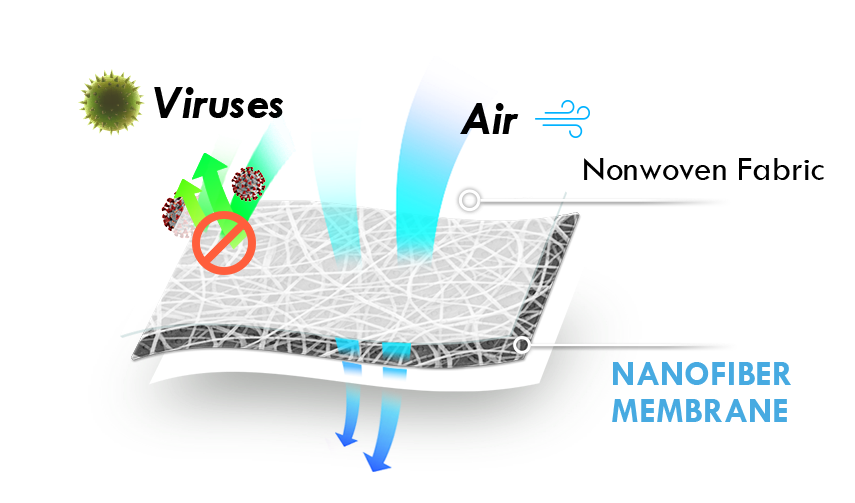
Image Credit: Inovenso
Rather, nanofiber filtration layers employ mechanisms such as inertial diffusion, impaction and interception.
It is possible to synthesize nanofibers using several types of laboratory procedures. These include phase separation, self-assembly and template synthesis, with certain techniques more suited to working with specific materials and sizes.
Electrospinning remains the most adaptable and common means of manufacturing nanofibers. Electrospinning involves a polymeric solution being charged under high voltage, forming jet streams towards a target substrate before solidifying. A solid textile - a layer of nanofibers - forms on the target substrate.
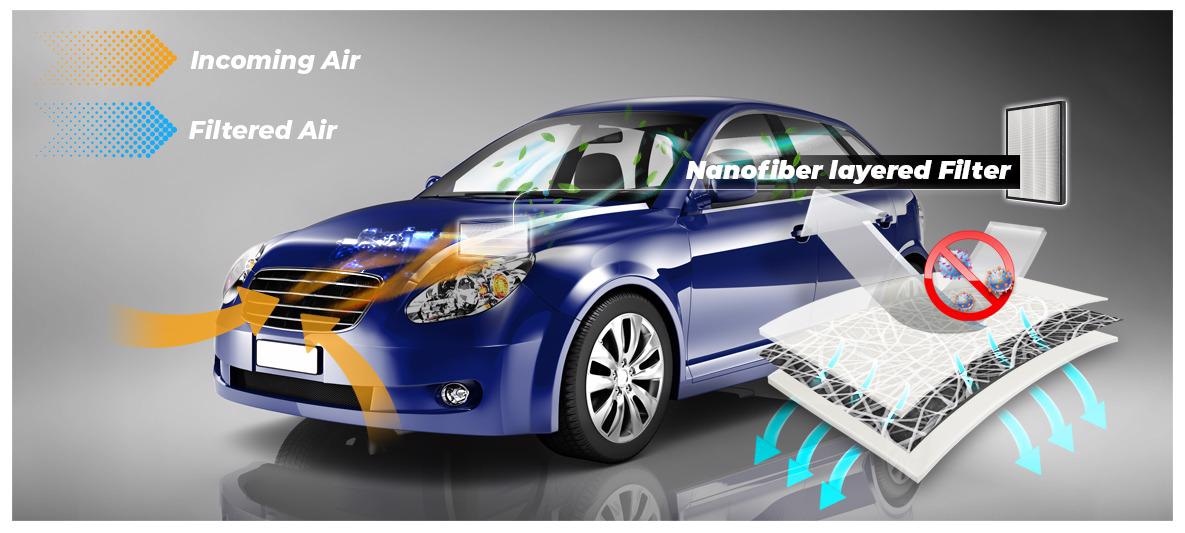
Image Credit: Inovenso
A number of industry leaders in the filtering sector are looking to employ nanofiber technology in their products. However, limitations in production rates have proved challenging in the large-scale manufacture of these products.
While the standard electrospinning technique is highly versatile, this approach is unable to produce nanofibers at a rate suitable for industrialization.
The charged polymeric solution used in an electrospinning setup is commonly evacuated from the small orifice of a needle, meaning that the quantity of nanofiber layer produced is minimal.
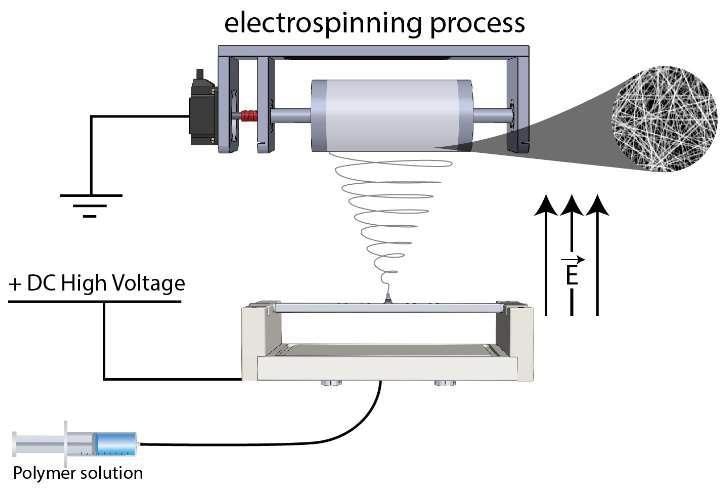
Image Credit: Inovenso
Research on Electrospun Nanofiber Filters
Researchers are working to modify this process, aiming to improve throughput during electrospinning while preserving sufficiently low fiber sizes. Inovenso has successfully developed a patented hybrid electrospinning technology, utilizing specially designed nozzles to replace standardized needles.
This new technology increases production rates by a factor of four while still producing nanofiber layers with low fiber diameters and high throughput.
Inovenso also produces its own electrospun nanofiber filters, specifically designed for air filtration applications. These Inofilters can be utilized as the filtering medium for half face masks, including N95/N99 filtration masks.
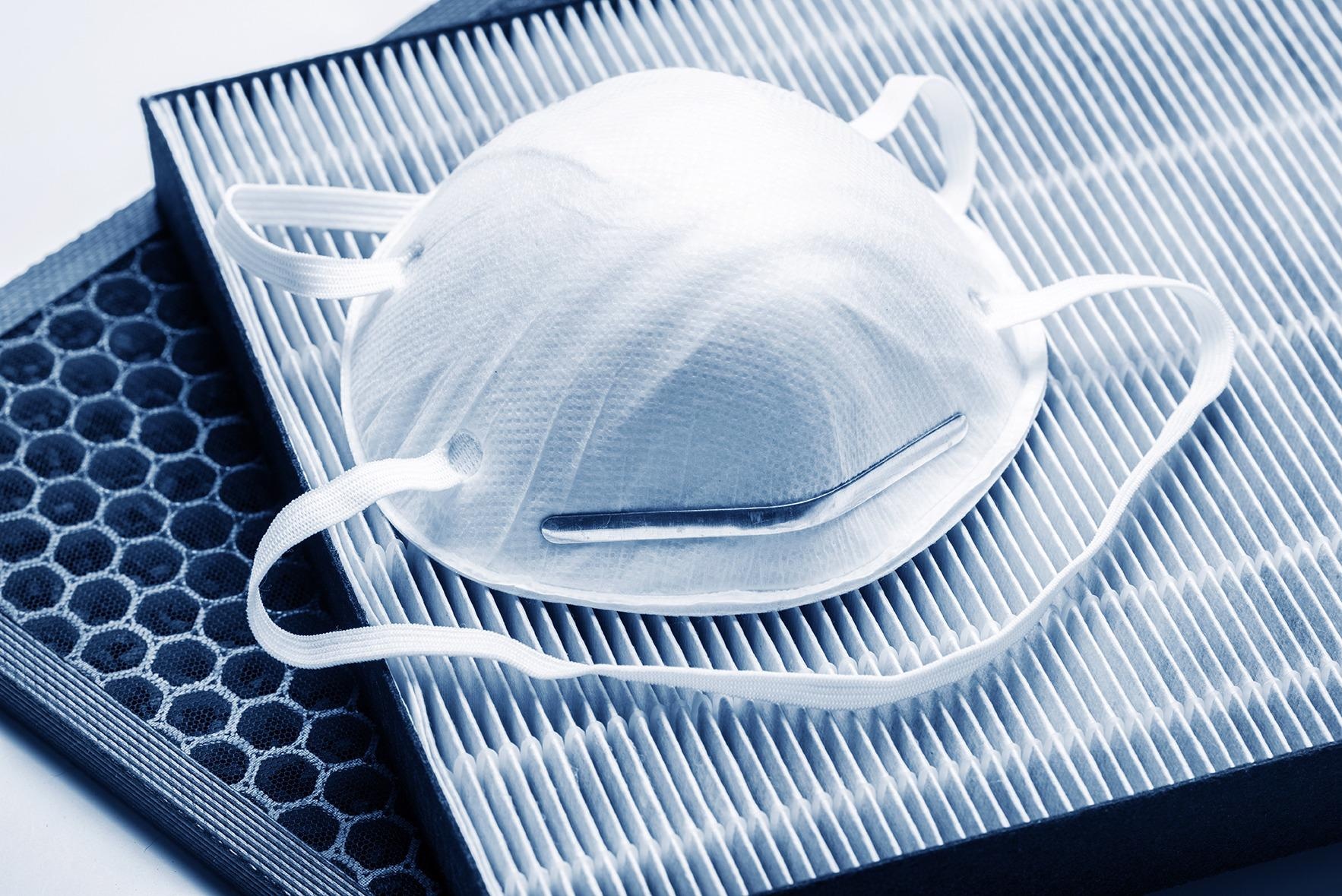
Image Credit: Inovenso
Inofilters can also be employed in fine air filters and Highly Efficient Particulate Arrestors (HEPA) and Ultra-Low Particulate Arrestors (ULPA) filters. These types of filters are the most advanced available, offering efficacy of more than 99%; a level of efficacy made possible thanks to nanofiber structures.
Nanofibers are able to physically trap undesirable particles, removing these from the air stream due to their fine fiber dimensions and high surface area to volume ratio, only allowing clean air to pass.
The Research and Development team at Inovenso has undertaken extensive research into the development of an optimal recipe for producing filter membranes able to achieve high filtration while maintaining a comparatively small pressure drop.
Once they are shaped into masks, these membranes are able to provide a balance of protection and comfort when breathing.
Nanofiber membranes are generally soft, so these are added to a support layer in order to improve their mechanical characteristics. The design for filter media is 3-ply with the addition of a nanofiber layer between two non-woven substrate layers.
Inovenso is continuing its work to advance this filtration technology, exploring the use of post-treatment and the addition of antimicrobial layers that can not only capture but also kill any harmful pollutants.
Acknowledgments
Produced from materials originally authored by Muhammad Omer Sahto from Inovenso.
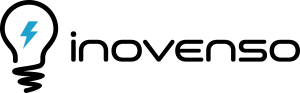
This information has been sourced, reviewed and adapted from materials provided by Inovenso.
For more information on this source, please visit Inovenso.