The regulations governing the viable and nonviable management of Class D clean zones indicate that necessary actions should be determined on a site-by-site, risk-based assessment.
According to the FDA Guidance on Sterile Manufacture–2004: “The nature of the activities conducted in a supporting clean area determines its classification.”
Best practices can also be established by triangulating reasonable standards from various worldwide regulatory agencies.
For example, the Japan Aseptic Processing Guidance offers guidelines on what should be done when monitoring the background support regions. It states, “Classes C and D airborne microbial monitoring should be performed twice per week, and airborne particles once per month.”
The frequency recommendation for a monthly evaluation of aseptic areas also conforms with the PDA TR13 (2001–since revised) Fundamentals of an Environmental Monitoring Program, which proposed that: “Grade D areas be monitored for total particles on a monthly basis.”
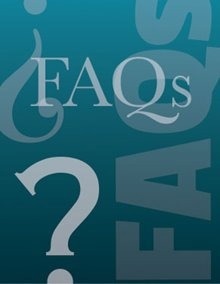
Image Credit: Particle Measuring Systems
The reason for regulating these less crucial areas is because there is contamination exposure of components or materials handled in these areas, albeit at a low level. As indicated by the guidelines listed above, it is typically advised that frequent assessments be carried out to avoid any considerable buildup of contaminants where these activities are carried out.
If an area is considered to be a Grade “mentionable” area as a result of the operations performed within it, that particular area must fulfill the internal quality criteria based on the threat to the product or activities undertaken there.
If it is determined that there is a low risk to the finished product or materials, that area will be given a lower Grade classification, which will mean that lower demand for resources will be necessitated to ensure that quality is maintained.
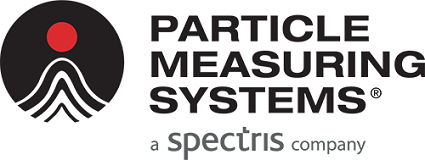
This information has been sourced, reviewed and adapted from materials provided by Particle Measuring Systems.
For more information on this source, please visit Particle Measuring Systems.