Researchers rely on professional tools to obtain success in their experimental studies as they offer the data required, irrespective of the ongoing tasks. Through progressing main technologies and designs, Nanosurf has made the FlexAFM one of the highly versatile and flexible AFMs ever.
This enables a vast range of research applications to be handled with comfort. Together with the strong C3000i controller, complicated material characterizations are possible.
- Modular concept to precisely match user’s requirements
- Flat and linear scanning as a result of flexure-based scanner technology
- Consistent with inverted microscopes
- True flexibility available with exchangeable cantilever holders for specialized tasks
- Appropriate for any sample size
- Scanning capabilities in liquid and latest measurement modes
We have been using the FlexAFM system for the last couple of years. The ease of use and its robustness helped us publish a number of articles in high impact journals. I'm very pleased with the performance of your AFM system and would highly recommend your systems for other customers in India and abroad. The technical support from Switzerland as well as local support in India is found to be very satisfactory.
Nitya Nand Gosvami, Professor, Department of Materials Science & Engineering, Indian Institute of Technology Delhi
Image Credit: Nanosurf AG
Practical Details That Really Matter in Daily Use
Cantilever holders with alignment structures are available for use with cantilevers that have alignment grooves. This offers circumventing laser alignment, micrometer repositioning accuracy and enables users to determine the same sample features repeatedly.
Entering the image in the cantilevers is from top to bottom, so sample orientation is frequently the same, no matter if users look by eye, CCD camera or AFM (when scanned at the default scan angle).
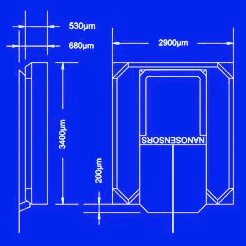
Alignment chip technology. Image Credit: Nanosurf AG
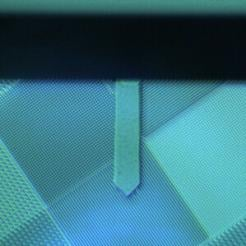
Top view on stand-alone stage. Image Credit: Nanosurf AG
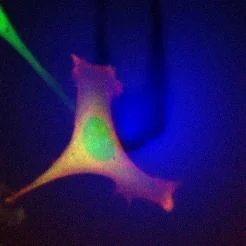
Top view on inverted microscope. Image Credit: O. Guilaume-Gentil, ETH Zürich, Switzerland.
FlexAFM Imaging Modes
This overview displays which modes the instrument is capable of. Some modes might need extra components or software options.
Standard Imaging Modes
- Static force mode
- Lateral force mode
- Phase imaging mode
- Dynamic force mode (tapping mode)
Thermal Imaging Modes
- Scanning thermal microscopy (SThM)
Magnetic Properties
- Magnetic force microscopy
Electrical Properties
- Conductive AFM (C-AFM)
- Surface potential
- Electrostatic force microscopy (EFM)
- Piezoelectric force microscopy (PFM)
- Scanning spreading resistance microscopy (SSRM)
- Kelvin probe force microscopy (KPFM)
Mechanical Properties
- Force spectroscopy
- Adhesion
- Force modulation
- Stiffness and modulus
- Force mapping
- Unfolding and stretching
Other Measurement Modes
- Electrochemical AFM (EC-AFM)
- Lithography and nanomanipulation
System Specifications
Table 1. FlexAFM 5 scan head specifications with C3000i controller. Source: Nanosurf AG
FlexAFM 5 scan head specifications with C3000i controller |
100-µm scan head |
10-µm scan head |
Sample size |
Unlimited without sample stage 100 mm on sample stage |
Maximum Petri dish height (fluid level) |
9 mm (6 mm) |
Manual height adjustment range |
6 mm |
Motorized approach range (at tip position) |
2 mm |
Max. scan range (XY) |
100 µm1 |
10 µm1 |
Max. height range (Z) |
10 µm2 |
3 µm1 |
XY-linearity mean error |
<0.1% |
XY-flatness at maximum scan range |
typ. 5 nm |
typ. 1 nm |
Detector bandwidth |
DC - 4 MHz |
Detector noise level (RMS) |
typ. 60 pm / max. 100 pm (3, 4) |
Z-sensor noise level (RMS) |
typ. 180 pm / max. 200 pm (3) |
Z-measurement noise level (RMS, static mode in air) |
typ. 100 pm / max. 200 pm |
Z-measurement noise level (RMS, dynamic mode in air) |
typ. 35 pm / max. 50 pm |
Scan head dimensions |
413 x 158 x 53 mm |
Scan head weight |
1.25 kg |
(1) Manufacturing tolerances ±5%
(2) Manufacturing tolerances ±10%
(3) Measured at 2 kHz
(4) Measured with XYContr cantilever
Table 2. C3000i controller — Core hardware specifications. Source: Nanosurf AG
. |
. |
X/Y/Z-axis scan and position controller |
3× 24-bit DAC (200 kHz) |
X/Y/Z-axis position measurement |
1× 24-bit ADC (200 kHz) |
Excitation & modulation outputs |
2× 16-bit DAC (20 MHz) |
Analog signal input bandwidth |
0–5 MHz |
Main input signal capturing |
2× 16-bit ADC (20 MHz)
2× 24-bit ADC (200 kHz) |
Additional user signal outputs |
1× 24-bit ADC (200 kHz) |
Digital synchronization |
Sync Out 1/2: digital outputs, signal range 0/5 V TTL pulses |
FPGA module and embedded processor |
ALTERA FPGA,
32-bit NIOS-CPU,
80 MHz, 256 MB RAM,
multitasking OS |
Communication |
USB 2.0 Hi-Speed to PC and scan head interface |
System clock |
Internal quarts (10 MHz) or external clock |
Power |
90–240 V AC, 70 W, 50/60 Hz |
Table 3. Cantilever. Source: Nanosurf AG
. |
. |
Width |
min. 20 μm |
Length |
min. 40 μm |
Reflective coating |
Reflective coating recommended |
Liquid measurements |
Yes, with gold coating |
Alignment grooves |
Required by default
Special cantilever holders without alignment grooves are available |
Resonance frequency dynamic
mode Easyscan 2 Controller |
15 kHz to 350 kHz |
Resonance frequency dynamic
mode C3000 Controller |
<4 MHz |
Cantilever shape |
Single rectangular cantilevers and multilever cantilevers (depending on scan head version and cantilever holder) |
Chip thickness |
300 μm, 500 μm or 600 μm depending on cantilever holder |
Scan Head Dimensions
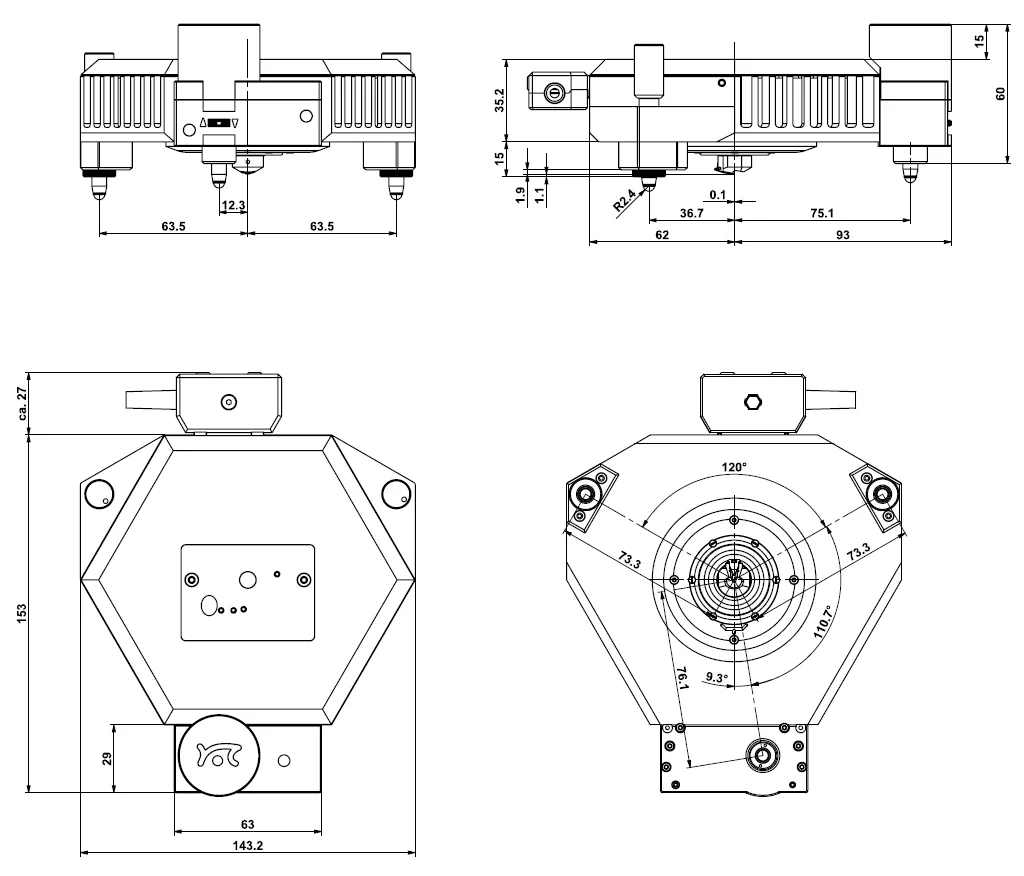
Image Credit: Nanosurf AG