Based on Leica Microsystems’ motto, “with the user for the user,” the redesigned EM TIC 3X combines performance and versatility in a way that is relevant to everyday life.
The latest EM TIC 3X’s doubled ion milling rate can be further improved with the choice of five distinct stages that are tailored to the application’s needs.

Leica EM TIC 3X—Ion Beam Slope Cutter. Image Credit: Leica Microsystems GmbH
Reproducible Results by Ion Milling
The Triple Ion Beam Milling System, EM TIC 3X, enables the fabrication of cross sections and planar surfaces for Microstructure Analysis (EDS, WDS, Auger, EBSD), AFM, and Scanning Electron Microscopy (SEM) examinations.
The EM TIC 3X allows the user to produce high-quality surfaces of practically any material at normal temperature or under cryogenic conditions, revealing the sample’s interior structures close to their natural state as is practical.

1: Cross section of SiC abrasive paper l 2: Cross section of veneer l 3: Coaxial polymer fiber (water soluble) prepared at −120 °C l 4: Oil shale (nanopores), revealed with the EM TIC 3X (rotary stage) total sample size Ø 25 mm. Image Credit: Leica Microsystems GmbH
Efficiency
The key determinant of an ion beam miller’s efficiency is the production of high throughput, high-quality output. The innovative triple ion beam technology optimizes the preparation quality and cuts down on working time, which is more than enough to make up for the fact that it is possible to double the milling rate in comparison to the previous generation.
In a single session, up to three samples can be processed. One stage can perform polishing and cross-sectioning.
Workflow solutions allow for the efficient and safe transfer of samples to subsequent analysis systems or preparation instruments.

Image Credit: Leica Microsystems GmbH
Flexible system—Adaptable to the Needs at any Time
The flexible selection of stages makes the EM TIC 3X a suitable instrument not only for high throughput but also for contract laboratories.
Based on the requirement, the EM TIC 3X can be configured individually using interchangeable stages for applications of standard preparation, high throughput processing, and the preparation of extremely heat-sensitive samples, such as rubbers, polymers, or biological materials at low temperatures.
The interchangeable stages include:
- Standard stage
- Rotary stage
- Multiple sample stage
- Cooling stage
- Vacuum Cryo Transfer Docking Station
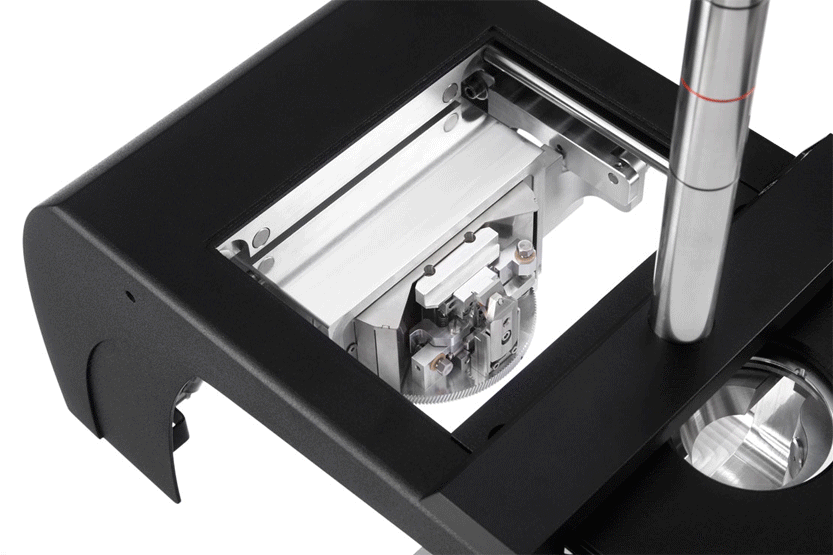
Image Credit: Leica Microsystems GmbH
Environmentally Controlled Workflow Solution
The VCT docking port and the EM TIC 3X provide the ideal workflow for surfacing cryogenic and/or environmentally sensitive materials that can be geological, biological or industrial materials.
Then, under inert gas, vacuum, and cryo conditions, they can be transported to a coating system, such as the EM ACE600 or EM ACE900, and/or SEM systems.

Image Credit: Leica Microsystems GmbH
Standard Workflow Solution—Create Synergies with the EM TXP
Mechanical preparation is often required prior to the use of the EM TIC 3X to get as close as possible to the area of interest. A special target surfacing system called the EM TXP was created for cutting and polishing samples before subsequent procedures using tools like EM TIC 3X.
The EM TXP is specifically made to saw, mill, grind, and polish samples before analysis. It excels with challenging specimens where pinpointing and preparing difficult targets becomes a simple task.

Image Credit: Leica Microsystems GmbH