The MCR Evolution series from Anton Paar features two high-end models — MCR 702e MultiDrive and MCR 702e Space MultiDrive — which are the most flexible rheometers in the market. Besides all conventional rheological test modes, they can be equipped with an additional lower drive unit.
This aspect enables users to perform rheological tests using two torque transducers and drive units simultaneously, thereby paving the way for multiple possibilities for users’ research. There are no restrictions when it comes to the used test modes, accessories, temperature devices and measuring systems, as well as no restrictions on measurement precision.
Moreover, MCR 702e Space MultiDrive offers the highest working space and thus renders it easy to work with additional instruments and other accessories. In simple terms, this system is the most preferred to cover all feasible rheological applications at present and in the future.
MCR 702e MultiDrive
- This model is the high-end rheometer for advanced rheological research
- Ready for DMA in tension, torsion, compression or bending mode
- One rheometer with two drive units offers all working modes
- More than 200 accessories for limitless possibilities in research and development
MCR 702e Space MultiDrive
- This model is the preferred rheometer for advanced rheological research and Dynamic Mechanical Analysis
- Maximum working space enables easy combination with more mechanical or optical setups, for example, a confocal microscope
- The rheometer can be used for work in a glovebox, even under an inert gas atmosphere
Key Features
One Rheometer, All Rheological Working Modes
Thanks to the combination of two air-bearing-supported rotational drive units, users can perform rheological measurements in Separate Motor Transducer (SMT) and Combined Motor Transducer (CMT) modes.
A single air-bearing-supported EC motor in the CMT mode can help users to leverage the motor’s real-time position control (TruStrain™) and carry out “classic” stress-controlled tests.
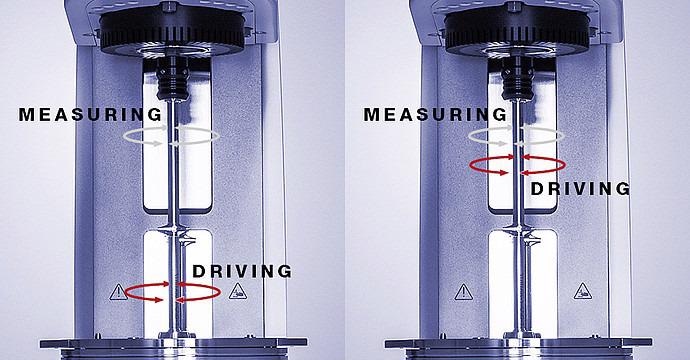
Image Credit: Anton Paar GmbH
In the SMT mode, one motor is run exclusively as a torque transducer, whereas the other motor is used only as a drive unit. This helps achieve the most perfect rheological results even in the transient regime of the measurement (for example, start-up shear and stress relaxation) and across a wide range of amplitude and frequency in oscillatory measurements.
All the working modes of the MCR 702e MultiDrive and MCR 702e Space MultiDrive models help users to complete the successful MCR series and contribute to making the MCR rheometers the most cited instruments in scientific rheological investigations.
Push Back the Limits of Material Characterization with Counter-Movement Mode
While working in the counter-movement mode, the rheometer uses the air-bearing-supported EC motors both as drive units and as torque transducers. Both motors are configured to readily move in opposite directions, which can be used, for instance, to form a fixed stagnation plane in a sample for sophisticated structure analysis of materials under shear using the microscope.
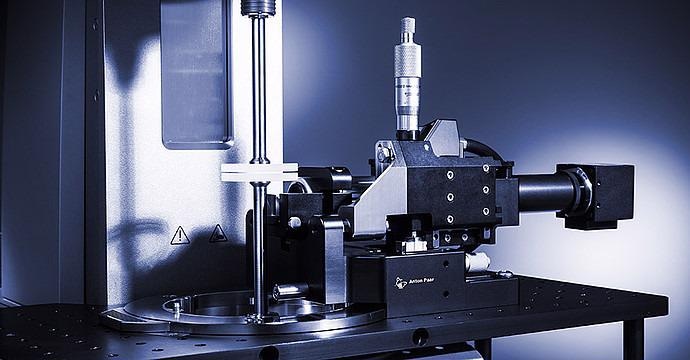
Image Credit: Anton Paar GmbH
This mode can also be used with a universal extensional fixture to perform extensional tests down to minimal measured torques. When it comes to speed, the counter-movement mode just “doubles the score” — up to a maximum speed difference of 6000 rpm, thus considerably widening the shear rate range for high-shear applications.
Ready for DMA in Torsion, Tension, Bending, Compression and More
As an alternative to a lower rotational drive, users can insert an additional lower linear drive to carry out DMA in compression or bending mode with measuring systems like three-point bending, parallel plates, or cantilever.
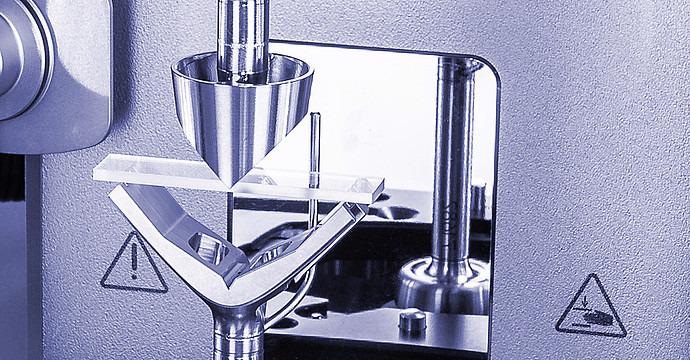
Image Credit: Anton Paar GmbH
Moreover, together with geometries for rectangular samples, films and fibers, the linear drive can be used to carry out DMA in tension while the upper rotational drive is used for DMA in torsion — both in a single test definition. Furthermore, the linear drive can perform thermomechanical analysis, relaxation tests or creep and creep recovery tests.
The Best now Better: The Device for Applications that were Previously Unthinkable
The new MCR 702e Space MultiDrive has been engineered to offer an exclusive maximized workspace underneath the rheometer support plate, on both sides of the instrument. This enables not just simple installation of accessories but also easy integration with additional external setups apt for sophisticated material characterization.
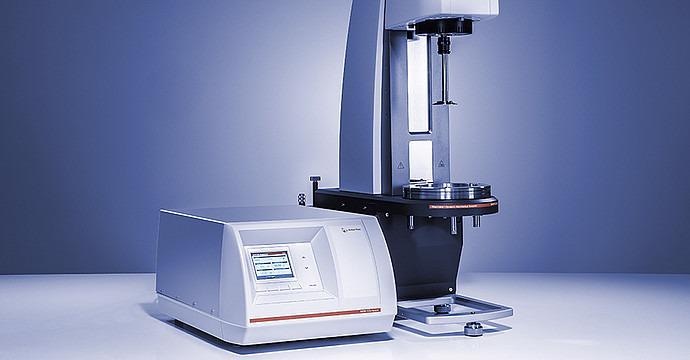
Image Credit: Anton Paar GmbH
For instance, the MCR 702e Space MultiDrive enables users to blend confocal microscopy and rheology. Moreover, the separate electronics box of the rheometer enables the rheometer to be set up where space is constrained or in a laboratory glovebox, even when an inert gas (nitrogen, argon) atmosphere is used, for example, for high-temperature measurements on samples with a specific hazard level.
Measure and Control the Temperature Where it Matters
The high-precision temperature control units together with Anton Paar’s novel optoelectronic technology enables users to control the greatest influence of all — temperature. The technology allows contact-free data transmission based on photovoltaic effect and light emission. This allows the temperature to be determined without any impact on the torque sensitivity in Separate Motor Transducer (SMT) mode and counter-movement mode.
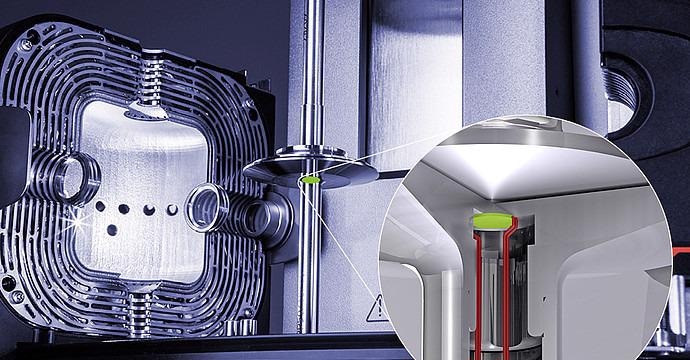
Image Credit: Anton Paar GmbH
The sensor is placed directly in the measuring system very near to the sample (at a distance of just 1 mm), thus reducing potential offsets between the sample temperature and the temperature measured at the sensor. This allows the sample temperature to be accurately determined even during step- or ramp-like temperature changes.
More than 200 Accessories and Smart Features to Fit All Applications
The MCR 702e MultiDrive and MCR 702e Space MultiDrive models can be readily fitted with any temperature device, measuring system and/or application-specific accessory from the Anton Paar MCR range to perform standard and advanced rheological analyses of the users’ sample.
Thanks to the patented Toolmaster™ feature, all connected devices and measuring systems are automatically recognized and configured. Moreover, the QuickConnect function enables the measuring systems to be connected with a single hand. Both these features guarantee minimum work and the highest flexibility required to adapt the configuration to users’ needs.
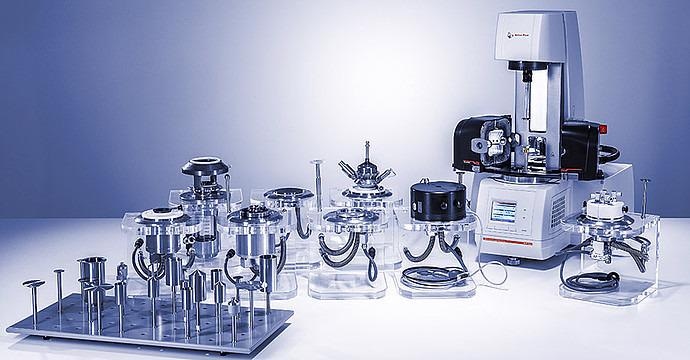
Image Credit: Anton Paar GmbH
Technical Specifications
Source: Anton Paar GmbH
|
|
MCR 702e MultiDrive
MCR 702e Space MultiDrive |
Technical Data |
Unit |
Configuration with
1 EC motor |
Configuration with
2 EC motors |
Bearing design |
- |
Air, fine-pored carbon |
Motor design |
- |
Electronically Commutated (EC) - Permanent Magnet Synchronous Motor |
Displacement transducer design |
- |
High-resolution optical encoder |
Normal force measurement design
(US Pat. 6167752, 1996) |
- |
360° capacitive sensor, non-contacting, fully integrated in bearing |
Active thermal management of
bearing and normal force sensor |
- |
Yes |
Yes |
Working modes |
- |
Combined Motor Transducer (CMT) |
Separate Motor Transducer (SMT),
Counter Movement [1] |
Minimum torque (rotation) |
nNm |
1 |
1 |
Minimum torque (oscillation) |
nNm |
0.5 |
0.5 |
Maximum torque |
mNm |
230 |
230 |
Minimum angular deflection
(set value) |
µrad |
0.05 |
0.05 |
Maximum angular deflection
(set value) |
µrad |
∞ |
∞ |
Minimum angular velocity [2] |
rad/s |
0 |
0 |
Maximum angular velocity
Maximum speed |
rad/s
1/min |
314
3000 |
628
6000 |
Minimum angular frequency [3] |
rad/s |
10-7 |
10-7 |
Maximum angular frequency [4]
Maximum frequency |
rad/s
Hz |
628
100 |
628
100 |
Normal force range |
N |
-50 to 50 |
-50 to 50 |
With Exposed Support Plate
(WESP / Space) [5] |
- |
Yes |
Yes |
Dimensions (W x H x D) |
mm |
444 x 753 x 586
Space:
212 x 767 x 554 |
444 x 753 x 586
Space:
212 x 767 x 554 |
Weight |
kg |
48
Space:
51 |
58
Space:
61 |
Additional Device Features |
Device display with remote control of software
(decoupled from measuring sensor for mechanical and electromagnetic interference prevention) |
- |
Yes |
Yes |
Direct strain/stress controller |
- |
Yes |
Yes |
TruRate™ / TruStrain™
(sample adaptive controller) |
- |
Yes |
Yes |
Raw data (LAOS, waveform) |
- |
Yes |
Yes |
Normal force profiles (set and read) |
- |
Yes |
Yes |
Velocity profiles, tack, squeeze |
- |
Yes |
Yes |
Automatic gap control/setting (AGC/AGS) |
- |
Yes |
Yes |
Electronic trim lock for measuring geometry |
- |
Yes |
Yes |
Fully automatic temperature calibration |
- |
Yes |
Yes |
TruGap™ (permanent control of the real measuring gap) (US Pat. 6499336, 2000) |
- |
Optional |
Optional |
T-Ready™ [6] (detection of sample temperature equilibrium time)
(US Pat. 8904852, 2011) |
- |
Yes |
Yes |
Toolmaster™ (measuring geometries and accessories, storing of zero-gap)
(US Pat. 7275419, 2004) |
- |
Yes |
Yes |
QuickConnect Coupling for measuring geometries
(one-hand operation, screwless) |
- |
Yes |
Yes |
Trimming mirror
(360° blind sample spot prevention) |
- |
Yes |
Yes |
Three-point support of device
(three robust feet for tool-free one hand alignment) |
- |
Yes |
Yes |
Three-point support for mounting of measuring cells (wobble prevention, no misalignment after changing of cells) |
- |
Yes |
Yes |
Maximum temperature range |
°C |
-160 to +1000 |
-160 to +600 (950 [7]) |
Maximum pressure range |
bar |
up to 1000 |
n/a |
Ready for DMA in torsion and tension |
- |
Yes |
Yes |
Ready for Linear Drive
(DMA in tension, bending and compression)
(US Pat. 9574983, 2015) |
- |
Yes |
Yes |
Ready for tribology |
- |
Yes |
Yes |
Ready for powder flow and shear rheology |
- |
Yes |
Yes |
[1] US Pat. 8453496
[2] In controlled shear stress (CSS) mode. In controlled shear rate (CSR) mode depending on measuring point duration and sampling rate.
[3] Theoretical value (duration per cycle = 2 years)
[4] Higher frequencies are possible using multi-wave functionality (942 rad/s (150 Hz) or even higher, depending on measuring system and sample)
[5] MCR 702e Space MultiDrive: Unique maximized workspace below the rheometer support plate and on both sides of the instrument
[6] Depending on used temperature device
[7] Customized systems used in CTD 1000