The V-308 rapid focus nanopositioning stage has a resolution of 10 manometers and is intended for surface metrology and microscopy.
Features include:
- Adjustable travel range limitation to a total of 1 to 7 mm
- The user can adjust integrated weight force compensation to 1 kg
- High-dynamics direct drive
- Heavy-duty crossed roller guide
- Minimum incremental motion of 10 nm
- Suitable optional accessories, e.g., objective holders
V-308 Voice Coil Focus Drive for Precision Industrial Automation
Video Credit: PI (Physik Instrumente) LP
V-308 Voice Coil PIFOC for Microscopy & Life Sciences
Video Credit: PI (Physik Instrumente) LP
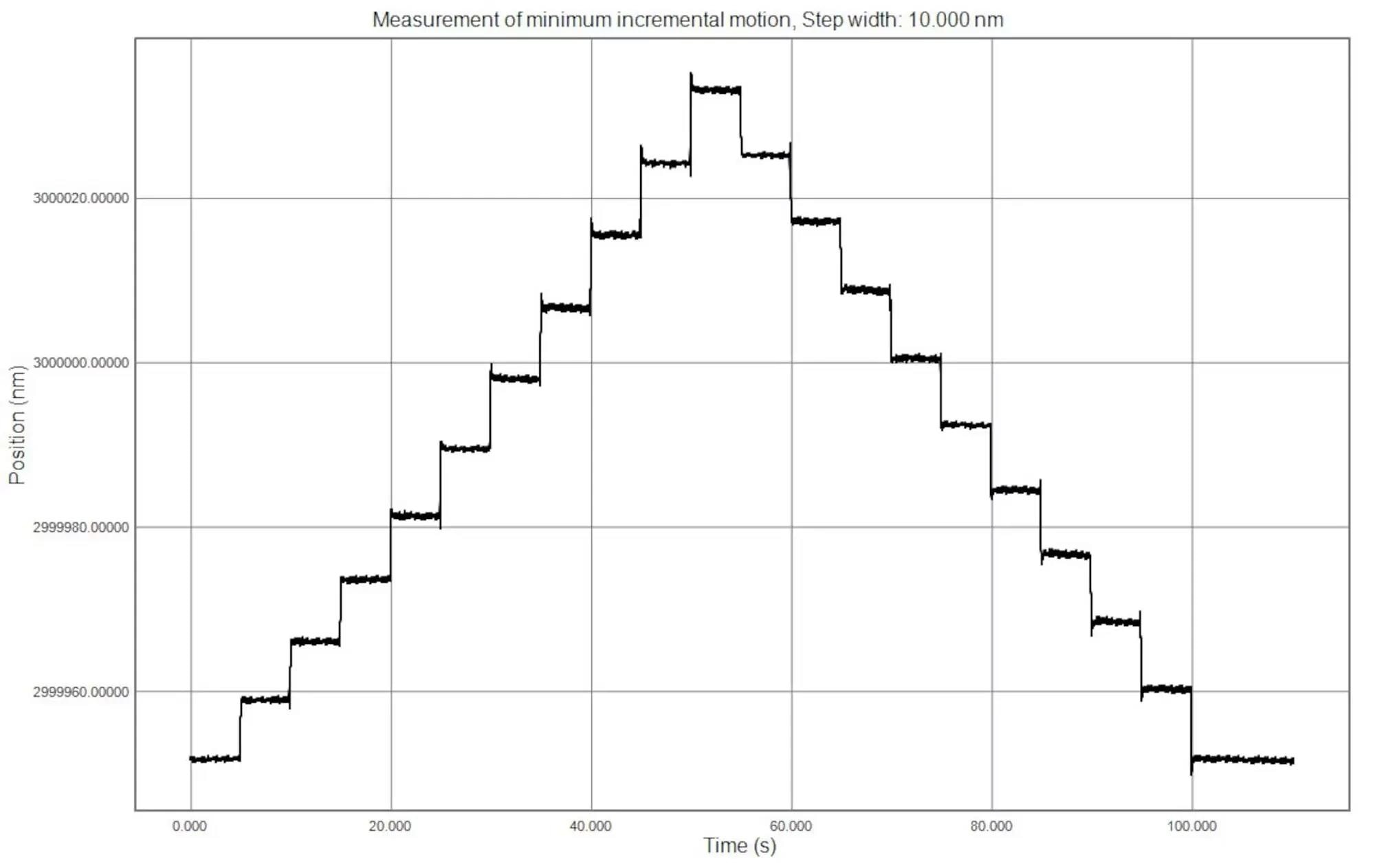
V-308.753030: Measurement for proving the minimum incremental motion of 10 nm. Image Credit: PI (Physik Instrumente) LP
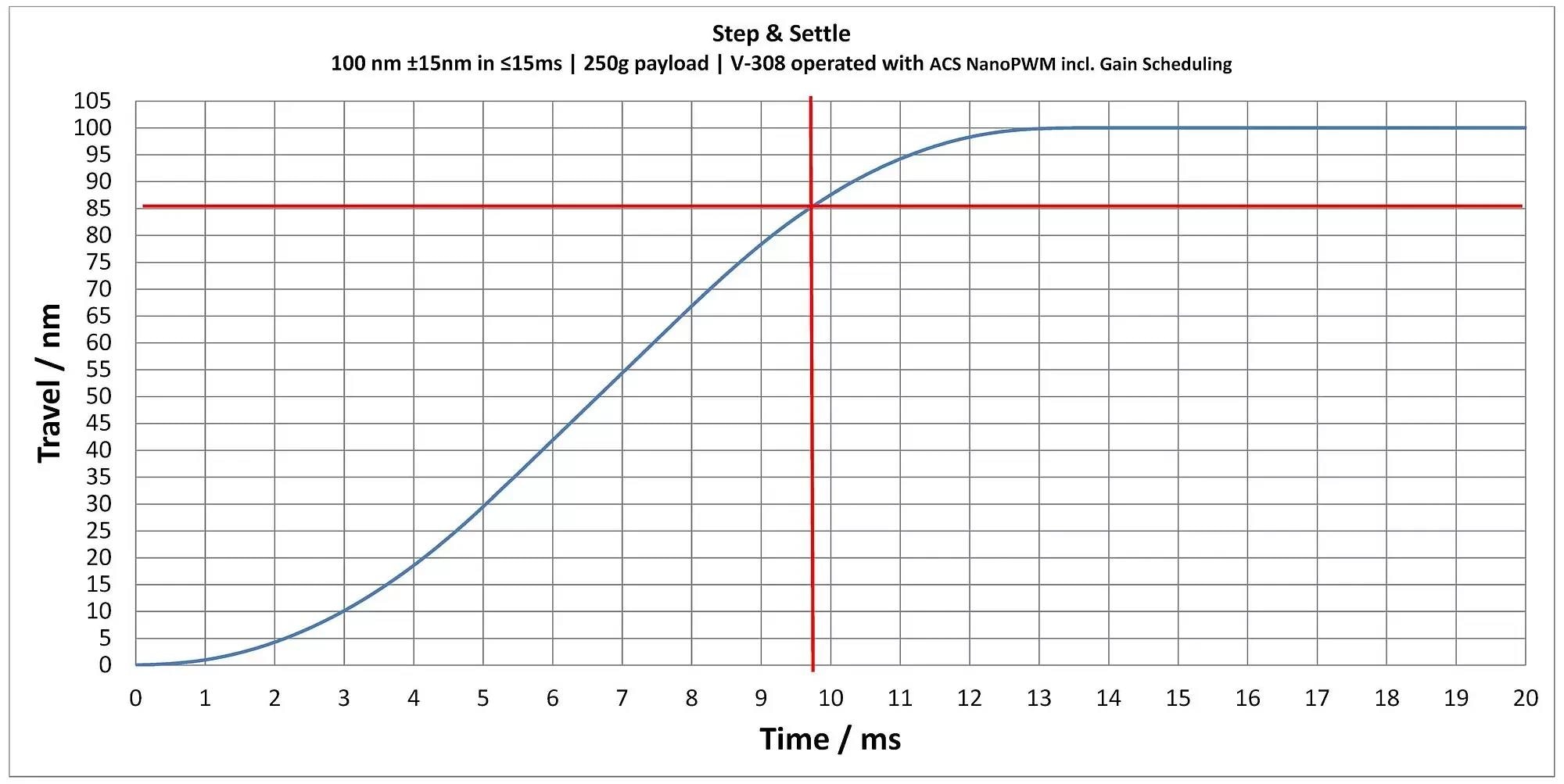
V-308 settling time with 250 g load at a step of 100 nm in an error band of +/-15 nm. Image Credit: PI (Physik Instrumente) LP
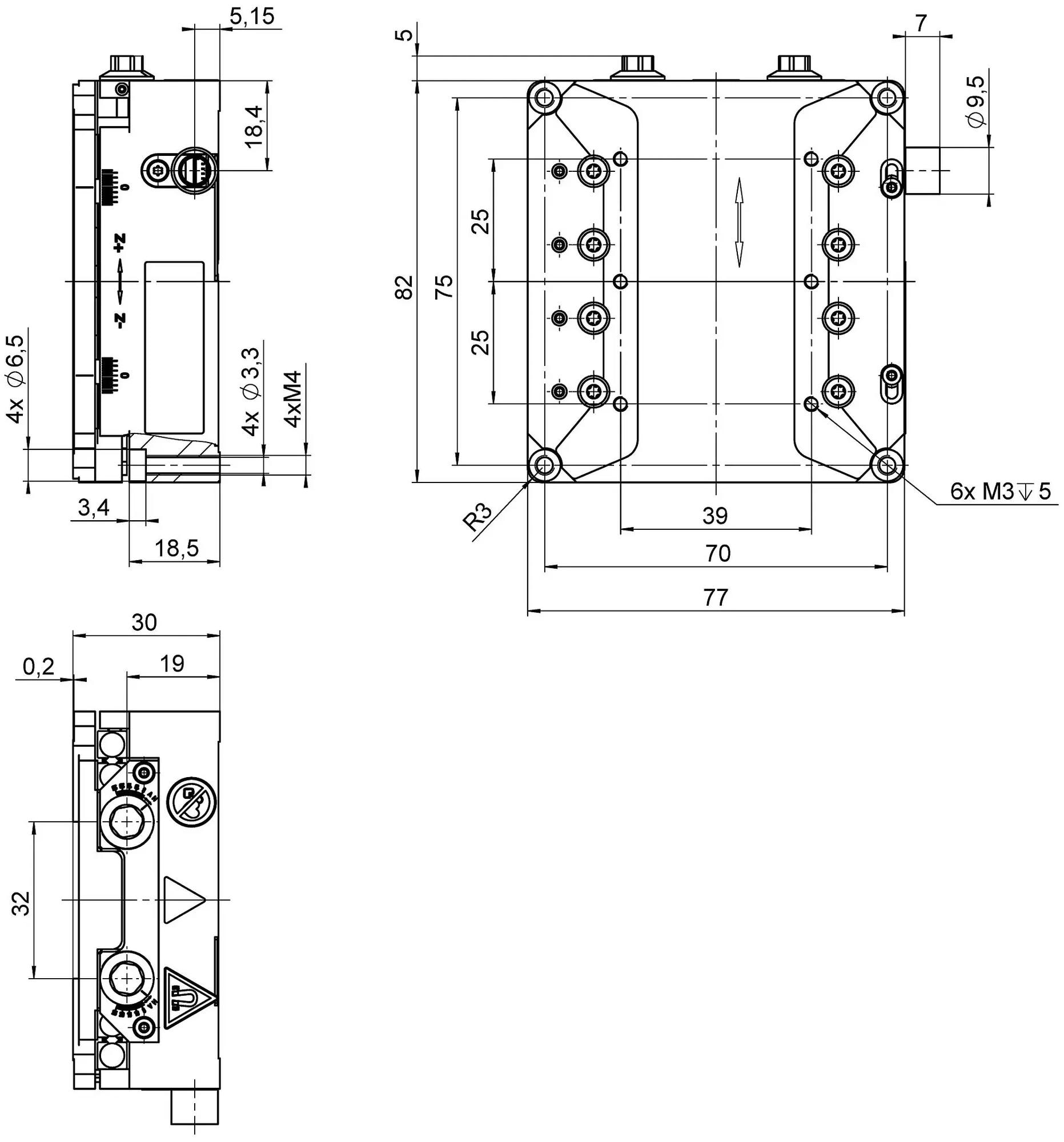
V-308.753030, dimensions in mm. Image Credit: PI (Physik Instrumente) LP
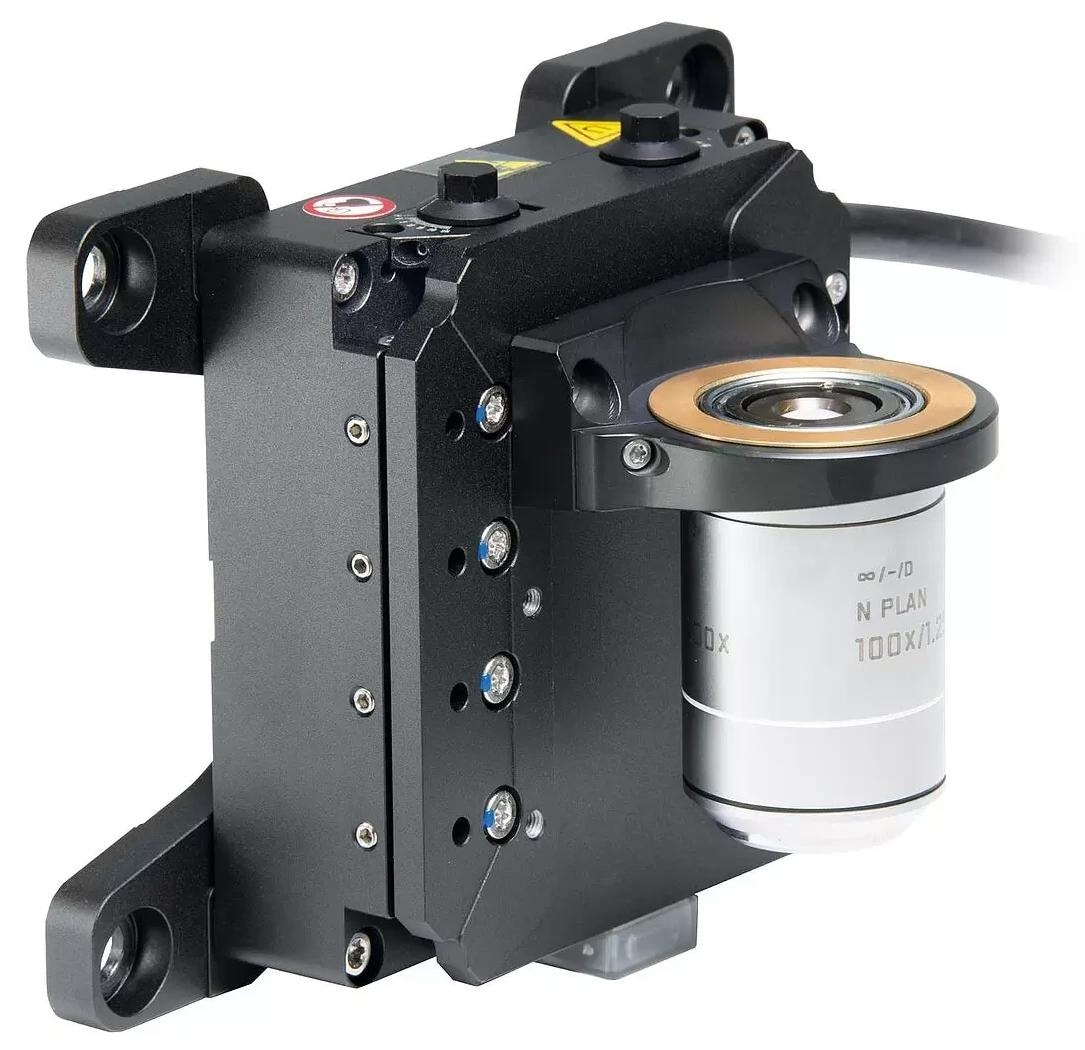
V-308 with V-308.AP1 adapter plate, V-308.OH1 objective holder, P-725.11L thread adapter, and objective. Image Credit: PI (Physik Instrumente) LP
Product Description
Z Positioning of Objectives With PIFOC
Many examinations or microscopy technologies need sample positioning in the Z direction, i.e., along the optical axis of the objective. It is also possible to shift the objective itself in the Z direction. PI provides PIFOC solutions for this purpose.
Integrated Weight Force Compensation
The product has magnetic weight force compensation. Even when no power is applied, this keeps a load of up to 1 kg aligned vertically to the motion axis. The user can adjust the weight force compensation.
PIMag® Voice Coil Motor
Voice coil motors are direct drives. The force of the drive element is delivered directly to the load to be moved in direct drives, which do not employ mechanical transmission elements, such as a coupling, drive screw, or gearhead.
Voice coil drives comprise a permanent magnet and a winding body positioned in the magnetic field’s air gap. When current runs through the winding body, it moves in the permanent magnet’s magnetic field.
Voice coil drives are ideal for applications requiring high dynamics and high velocity over short ranges due to their low weight and friction-free drive principle. Because these drives are hysteresis-free, they can also support high scan frequencies and precision positioning.
Crossed Roller Guide
The line contact of the toughened rollers in crossed roller guides replaces the point contact of the balls in ball guides. As a result, they are significantly stiffer and require less preload, which lowers friction and allows for smoother running. Crossed roller guides also have a high guiding accuracy and load capacity. Cages with force-guided rolling elements avoid cage creep.
Direct Position Measuring
Nonlinearity, mechanical play, or elastic deformation do not affect position measuring because it is carried out directly at the motion platform with utmost accuracy.
Application Fields
Microscopy
Multiphoton fluorescence microscopy, deep tissue inspection, digital slide scanning microscopy.
Biotechnology
Genome sequencing with the Solexa-Illumina method, Immuno-Assay fluorescence.
Medical Devices
Scanning laser ophthalmology, automated cell counters/flow cytometers.
Biomedical Research
Optical and magnetic tweezers.
Laser Materials Processing
Laser micromachining, laser ablation.
Semiconductor Industry
Semiconductor/wafer inspection.
Specifications
Source: PI (Physik Instrumente) LP
Motion |
V-308.753030 |
Tolerance |
Active axes |
Z |
|
Travel range in Z |
7 mm |
|
Acceleration in Z, unloaded |
8 m/s² |
max. |
Maximum velocity in Z, unloaded |
200 mm/s |
|
Flatness (Linear crosstalk in X with motion in Z) |
± 0.75 µm |
max. |
Straightness (Linear crosstalk in Y with motion in Z) |
± 0.75 µm |
max. |
Yaw (Rotational crosstalk in θX with motion in Z) |
± 50 µrad |
max. |
Pitch (Rotational crosstalk in θY with motion in Z) |
± 50 µrad |
max. |
Roll (Rotational crosstalk in θZ with motion in Z) |
± 50 µrad |
max. |
Positioning |
V-308.753030 |
Tolerance |
Integrated sensor |
PIOne: Incremental linear encoder |
|
System resolution in Z |
1 nm |
|
Bidirectional repeatability in Z |
± 0.5 µm |
typ. |
Bidirectional repeatability in Z, 100 nm step |
± 25 nm |
|
Positioning accuracy in Z, calibrated |
± 0.6 µm |
typ. |
Positioning accuracy in Z, uncalibrated |
± 4 µm |
typ. |
Minimum incremental motion in Z |
0.01 µm |
typ. |
Settling time in Z (100 nm step, ± 15 nm error band) |
15 ms |
|
Settling time in Z (250 nm step, ± 15 nm error band) |
15 ms |
|
Position noise in Z |
3 nm |
max. |
Sensor signal |
Sin/cos, 1 V peak-peak |
|
Sensor resolution |
1 nm |
|
Sensor signal period |
2 µm |
|
Reference switch |
Optical, direction sensing (reference edge track), 5 V, TTL |
|
Reference switch repeatability |
0.5 µm |
|
Drive Properties |
V-308.753030 |
Tolerance |
Drive type |
Voice coil |
|
Nominal voltage |
48 V |
|
Nominal current, RMS |
1.15 A |
typ. |
Peak current, RMS |
3.5 A |
typ. |
Drive force in negative direction of motion in Z |
4.2 N |
typ. |
Drive force in positive direction of motion in Z |
4.2 N |
typ. |
Peak force in negative direction of motion in Z |
9.45 N |
|
Peak force in positive direction of motion in Z |
9.45 N |
|
Force constant |
2.7 N/A |
|
Motor constant |
1.37 N/√W |
typ. |
Resistance phase-phase |
3.9 Ω |
typ. |
Inductance phase-phase |
0.85 mH |
|
Back EMF |
2.7 V·s/m |
max. |
Permissible maximum temperature for positioner components |
50 °C |
|
Mechanical Properties |
V-308.753030 |
Tolerance |
Guide |
Crossed roller guide |
|
Moved mass in Z, unloaded |
200 g |
|
Permissible push force in X |
10 N |
max. |
Permissible push force in Y |
10 N |
max. |
Permissible push force in Z |
10 N |
max. |
Overall mass |
600 g |
|
Mass without cable |
450 g |
|
Material |
Aluminum, anodized |
|
Miscellaneous |
V-308.753030 |
Tolerance |
Connector |
HD D-sub 26-pin (m) |
|
Recommended controllers / drivers |
C-414, G-910, ACS SPiiPlus + NPMpm (NanoPWM incl.)
|
|
Cable length |
1.5 m |
|
Operating temperature range |
10 to 50 °C |
Note on sensor resolution and minimum incremental motion: With C-414 motion controller at an interpolation of 211
Note on settling time: With gain scheduling (only with NanoPWM)
>Note on positioning accuracy and repeatability: Following ISO 230-2
Note on nominal current, peak current: Max. 10 s at 70 °C coil temperature
Note on nominal current, RMS: Value without cooling; with cooling: 1.55 A; with horizontally aligned positioner, with perforated plate made of steel, 200 mm × 250 mm × 12 mm
Note on inductance: Value at 100 mHz
The specifications apply to room temperature (22 °C ± 3 °C). The specifications can deviate outside of this range.