PI's A-352 large overhead XY/XYZ gantry posting system is available for precision automation.
Features
- XY gantry available for overhead motion. Travel ranges to 1 m × 2 m
- Accuracy recirculating ball bearing guides
- The modular platform is adaptable
- Various travel ranges. Options and tailored adaptations
- An absolute encoder is available
- Comes with high-performance ironless linear motors
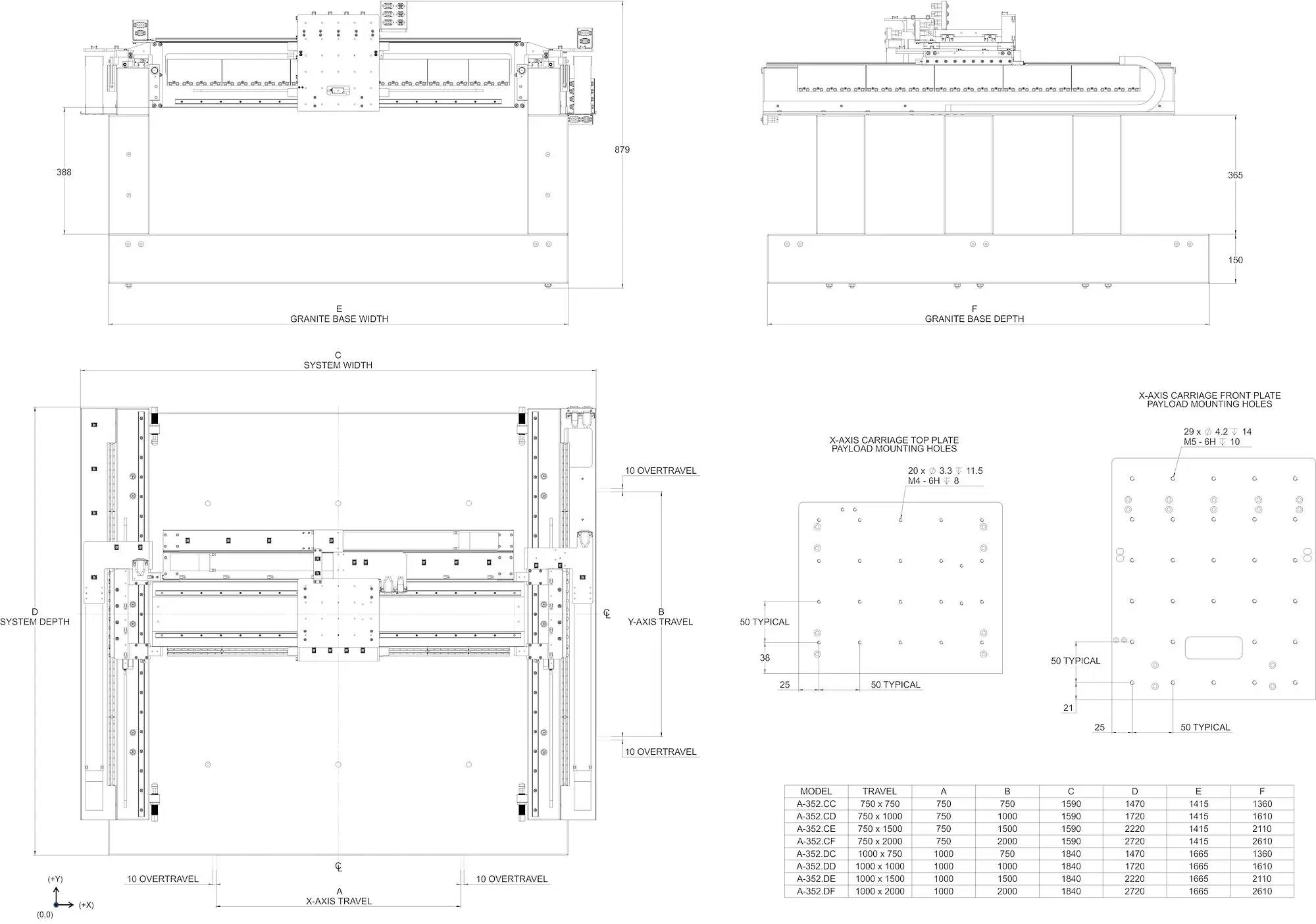
A-352 gantry system, dimensions in mm. Image Credit: PI (Physik Instrumente) LP
Overview
The MGS gantry system has been developed to optimize throughput for overhead motion applications. This stage is ideal for 3D printing, assembly, pick-and-place, inspection, alignment, and industrial automation applications.
The MGS uses preloaded linear mechanical bearings developed to provide improved stiffness and accuracy. Optional stainless steel guide rails could be delivered.
The gantry axis has guaranteed dual linear motors and dual linear encoders. Ironless linear motors offer smooth motion and no attractive forces or cogging. The linear motor and encoders are noncontact devices, so no backlash, wear, or maintenance issues arise
The A-352 has been coupled with first-in-class controllers and drive modules from ACS that provide excellent servo performance, advanced control algorithms to enhance dynamic performance and error compensation, and an extensive range of software development tools.
Application Fields
- Digital printing
- Scanning
- Electronics assembly and inspection
- AOI (Automatic Optical Inspection)
- Automation
Options and Customized Adaptations
- Granite base
- Work height could be customizable
- Support stands with and without vibration isolation
- Extra drag chains
- Liquid cooling of the linear motors
- Performance motors could be increased
Specifications
Source: PI (Physik Instrumente) LP
Motion |
Unit |
Bridge axis |
Gantry axis |
Travel range
|
mm
|
750, 1000
|
750, 1000, 1500, 2000
|
Guide
|
|
Recirculating ball bearing guide (lubrication and surface finish can be customized)
|
Drive
|
|
1 ×
Ironless 3-phase linear motor
|
2 ×
Ironless 3-phase linear motor
|
Measuring system
|
|
Absolute linear encoder, 1 nm sensor resolution, BiSS-C, steel measuring scale
|
2 ×
Absolute linear encoder, 1 nm sensor resolution, BiSS-C, steel measuring scale
|
Max. load capacity
|
|
30 kg
|
Positioning accuracy, calibrated (1)
|
µm
|
±2
|
Bidirectional repeatability
|
µm
|
±1
|
XY orthogonality
|
µrad
|
25
|
Max. velocity, unloaded (2)
|
m/s
|
2
|
1
|
Moved mass
|
kg
|
4.5
|
Depending on the travel range of the bridge axis:
750 mm: 65 kg
1000 mm: 80 kg
|
(1) Accuracy values assume short time duration and do not consider the long-term effects of thermal drift on the stage.
(2) Depends on the motor selected, controller performance, duty cycle, load, and other application-specific parameters.
Drive properties |
Unit |
Per motor winding |
Nominal voltage
|
V DC
|
70
|
Peak voltage
|
V DC
|
300
|
Force constant, RMS
|
N/A
|
27.5
|
Nominal force
|
N
|
210
|
Peak force
|
N
|
720
|
Nominal current, RMS
|
A
|
7.6
|
Peak current, RMS
|
A
|
26.2
|
Back EMF, phase-phase
|
V·s/m
|
22.5
|
Resistance, phase-phase
|
Ω
|
51.7
|
Inductance, phase-phase
|
mH
|
1.4
|
Miscellaneous |
|
Materials
|
Hardcoat aluminum
Guide rails made of steel, cleanroom grease (guide rails made of stainless steel on request)
Mounting hardware made of stainless steel
|