Nanocomposites can be broadly defined as a large range of systems that include one, two and three dimensional and amorphous materials, comprising dissimilar components which are blended at the nanometer scale. This definition encompasses colloids, porous media, gels and copolymers; however, it normally implies the solid combination of a nano-dimensional phase and a bulk matrix with differing properties because of differences in chemistry and structure. The nanocomposite’s electrical, mechanical, optical, thermal and catalytic properties is normally different from the constituent materials.
Nanocomposites can occur naturally, for example in the structure of bone and abalone shells.
Mechanically speaking, the key difference between nanocomposites and conventional composite materials is a high surface to volume ratio of the reinforcing phase or a high aspect ratio. These properties enhances the thermal and electrical conductivity of the nanocomposite and addition of carbon nanotubes or other nanoparticulates can provide improved optical properties, mechanical or heat resistance properties such as strength, stiffness and resistance to wear and damage.
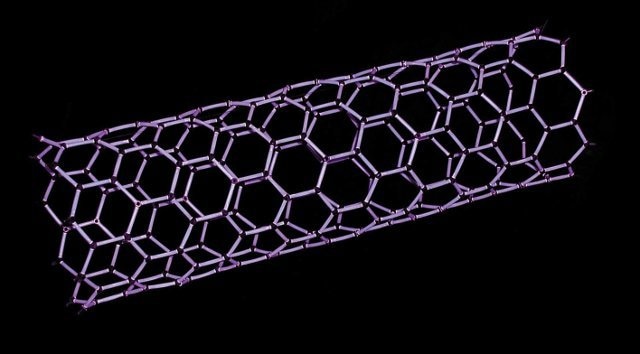
Carbon nanotube, oooo.
Polymer Nanocomposites
Polymer nanocomposites (PNC) comprise a polymer or copolymer with nanofillers or nanoparticles dispersed in the polymer matrix. The shape of the nanofillers can vary, and may include fibers, platelets or spheroids, but to fit the definition, and to provide the advantages, at least one dimension must be under 50 nm.
With most materials, a change in particle size from micro- to nano-scale causes a change in physical and chemical properties. One of the most important changes is the increase in surface area to volume ratio with decreasing particle size. This results in an increasing dominance of atom behavior on the particle surface. Since the nanoparticle surface area is high, interactions with other particles in the mixture become stronger, increasing the material's strength and heat resistance.
Challenges in Fabrication of Carbon Nanotube Polymer Matrix Composites
Carbon nanotubes (CNTs) are an ideal reinforcing agent for high-strength polymer composites, due to their superior magnetic, electrical and mechanical properties. Van der Waals interactions cause the CNTs to form stabilized bundles, making them are very difficult to disperse and align in a polymer matrix. A key challenge in preparing CNT-reinforced composites therefore lies in effective dispersion of CNTs into a polymer matrix. Effective tools are required for assessing the dispersion of the CNTs, as well as aligning and controlling CNTs in the matrix.
The techniques for dispersion of nanotubes in the polymer matrix include the following:
- Solution mixing
- Electrospinning
- Melt mixing
- Chemical functionalization of carbon nanotubes and
- In-situ polymerization
Applications of Carbon Nanotube Polymer Matrix Composites
Carbon nanotube polymer matrix composites can be used in a range of applications, two specialized applications of which are discussed below.
In a recent study led by David Carroll, Director of the Center for Nanotechnology and Molecular Materials at Wake Forest University, a new lighting device using field-induced polymer electroluminescence (FIPEL) technology was engineered using a mixture of novel materials. Carbon nanotubes have been used in this composite material to act as nanoantennae - they have a drastic impact not just for charge injection, but also on the electronic structure in the matrix, which significantly increases the efficiency of the lights. A degree of crystallization tends to occur within the polymer matrix around the nanotubes - this is strongly linked to the way the material works, and so is vital to control during the fabrication process.
A research team at the University of Surrey’s Advanced Technology Institute (ATI) and the School of Physics at Trinity College Dublin has collaborated to produce a carbon nanotube polymer composite that offers excellent performance as an electron emitter material. This material enables highly efficient large-area field emission displays, and also allow uses such as low power back lighting units in LCD televisions.
The nanotube concentration is controlled to enable efficient electron emission from the composite surface, reducing material wastage. By carefully choosing the right polymer and the right chemical treatment for the nanotubes, large area carbon nanotube-based electronics, including transparent plastic devices, are made possible. Dr David Carey, the lead researcher, stated that this research work proves how changing the structure of a material at the nanoscale can impact the properties on a larger scale, creating applications which would not otherwise be possible.
Conclusion
Carbon nanotubes have unusual properties, which could enable a wide range of advanced multifunctional materials. However, the results presently available show that adding large quantities of carbon nanotubes in polymer-based composites is not always possible - the nanotubes tend to agglomerate into clumps at higher concentrations, making the distribution uneven, which often makes the electronic properties unsuitable. Researchers are still working on solving some of these issues.
When limited quantities of nanotubes are incorporated into the polymer matrix, the optical, electrical and mechanical properties improve considerably, reaching values that are not seen in other materials. The exceptional properties obtained when carbon nanotubes are inserted into polymeric composites also signify a promising route for the design of ideal materials for aerospace-related structural applications. However, research in this field is still in its infancy.
References