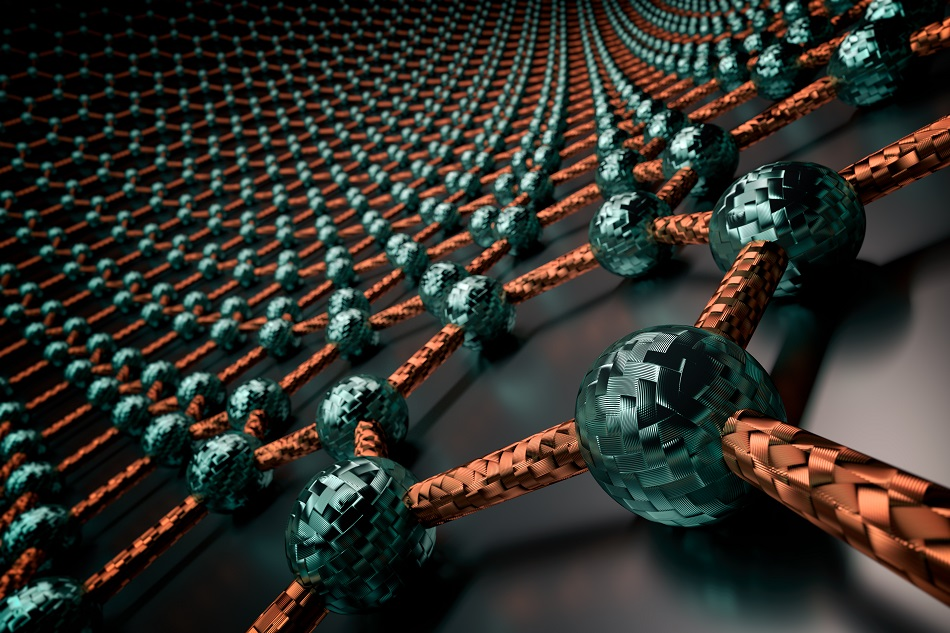
Image Credit: Forance/Shutterstock.com
Chemical sensors are devices that detect the presence of specific chemical compounds called analytes. The recognition element of the chemical sensor is sensitive to the presence of specific chemical compounds, which are converted into a measurable signal by a transducer with the value of the generated signal directly proportional to the concentration of the analyte.
Chemical sensors can be broken down into gas and electrochemical sensors, and are always being developed to meet the demands in chemical production and processing, as well as promoting the widespread uptake of chemicals in a range of industries, from food, biomedical, pharmaceuticals, and industrial safety, to environmental protection and security.
Gas Sensors
A graphene-based sensor for detecting gas molecules works by measuring alterations in the electrical conductivity of the material. Graphene-based gas sensors operate by adsorbing a gas molecule on the graphene’s surface, which acts as donors or acceptors of electrons.
Studies have demonstrated that it is possible to measure quantum scale changes in conduction with graphene. With this in mind, the possibility of pushing these sensors to their optimal level to detect single gas molecules seems plausible. This ultimate sensitivity can be linked to several factors, including the temperature at which the measurements are taken and the flow rate of the target gas.
In this application, graphene boasts the benefit of being an extremely low-noise material. Because of this, even at the limit of no carriers and a few extra electrons, graphene’s carrier concentration is able to change considerably. Additional to this benefit is the fact that graphene in this application enables the creation of four-probe devices on monocrystals. This guarantees that any influence of the contact resistance in limiting sensitivity is eradicated.
Electrochemical Sensors
It has also been shown that graphene is an effective chemical sensor in electrolyte-gated configurations. Graphene-based top-gate insulators can be fabricated as thin as 1 to 5 nm in an electrolyte, with a concentration of several millimolar. Even the best, top-gate graphene field-effect transistors (FETs) with atomic layer deposition (ALD) do not match these levels.
In electrochemical DNA sensors, electrode material for oxidase biosensors like glucose sensors, and in environmental analysis, in particular, in heavy metal ion detection, graphene-based electrochemical sensors have been developed. Research has demonstrated that graphene outperforms carbon nanotubes in three areas: direct electrochemistry of an enzyme, electrochemical detection of small biomolecules, and electroanalysis. Despite this success, it is not yet possible to produce the graphene required for these applications in bulk, although that is rapidly changing.
Photoelectric Sensors
The market for photoelectric sensors is essentially the same as indium-tin-oxide (ITO) replacements in transparent conductors. Graphene’s high electrical conductivity and near transparency make it an appealing option for transparent electrodes in photovoltaic cells and photoconductive sensors.
Samsung has already manufactured a touch-screen display product that uses graphene in place of ITO, although it isn’t clear whether this is a commercial venture or simply a demonstration of graphene-based touch-screen displays as a possibility for the future. Whichever may be true, the key advantage for graphene over ITO is that it is more compatible with flexible screens.
A graphene-based photodetector works by measuring photon flux. It measures this by converting the energy of the absorbed photons to an electrical current. Graphene-based photodetectors have a much wider operating wavelength range than conventional detectors based on group IV and III-V semiconductors. Additionally, graphene possesses superior carrier mobility over other materials, meaning its response time is much quicker than that seen in other photodetectors, which should translate into ultrafast optical sensors.
Magnetic Field Sensors
Initially, it seems as though graphene would not be a suitable choice for magnetic field sensor applications. The room temperature Hall coefficient for a typical InAs sensor is far better than a graphene-based one, but, when it is clear that graphene is only 0.34 nm thick, while InAs is 12 nm thick, it becomes obvious that it does have an attractive Hall effect resistance compared to InAs. In addition, graphene does not have to be hidden under additional layers, unlike typical two-dimensional electron gas devices, which does lend it some advantages in Hall effect sensing.
While some recent studies have been able to overcome this issue to some extent, graphene-based magnetic field sensors have suffered from thermal excitations of the electrons at room temperature dominating over this magnetoresistance effect in graphene.
Mechanical Sensors
Mechanical sensors detect changes in physical properties, for example, detecting when stress has been exerted on material by sensing the physical deformation affecting the material. Mechanical sensors are also able to detect a change in the resonant frequency, as well as to measure mass, force, pressure, strain, velocity, acceleration, and weight.
Researchers have previously shown that graphene can be successfully used as strain and pressure sensors. In graphene-based strain and pressure sensors, graphene is utilized as an active material to sense physical signals, including strain and pressure. Because of its high levels of electrical conductivity, graphene materials are often used as a conducting layer or electrodes of graphene-based strain and pressure sensors.
Conventional transduction methods of graphene-based strain and pressure sensors include resistive, capacitance, and piezoelectricity. Resistive sensors convert external forces into a variation of resistance, which can be directly detected by a pre-built detection circuit through alterations in the electrical signals. It acquires a resistive sensing signal through the change of the resistance, and the resistive effect being characteristic of graphene.
Ultrahigh sensitivity is awarded to graphene-based resistive sensors because of graphene’s high conductivity and favorable mechanical properties. As a common type of strain and pressure sensor, the advantages of graphene-based resistive sensors are numerous and include:
- A wide detection range
- Simple equipment construction
- Signal testing.
Capacitive sensors can detect different forms of force by converting mechanical stimulus signals into displacement signals. The change of displacement results in a change in capacitance, and because of graphene’s high levels of conductivity, attractive mechanical properties, and large specific surface area, it makes for a great choice for the electrical conductor and electrode in capacitive sensors.
Highly sensitive and fast-responding piezoelectric materials are widely used in pressure sensors that convert pressure into electrical signals. When mechanically deformed, a piezoelectric material generates an electric charge, which also works in the opposite effect, so that when an external electric field is applied to piezoelectric materials, they become mechanically deformed. Studies into this have shown that graphene can be engineered to take on piezoelectric properties.
Research has also shown that single-layer graphene can realize a negative piezoelectric effect, and two-layer and multi-layer graphene can realize a positive piezoelectric conductance effect. Graphene-based piezoelectric sensors have been used to detect continuous static pressure signals and perpendicular vibrations because of their ultrafast response time and ultrahigh sensitivity.
Flexible Sensors
Graphene-based materials have shown potential in flexible and stretchable strain and pressure sensors, photodetectors, Hall sensors, electrochemical sensors, and biosensors.
Graphene’s electrical properties do not degrade when mechanical strain is applied to it because of its inherent flexibility. As a result, graphene has been considered as an ideal material for making highly stretchable and flexible sensors and other electronic devices.
Investigating this area further, research has shown that flexible strain sensors can be made of piezoresistive graphene, microfluidic liquid metal, and stretchable 151 elastomers. In order to achieve flexible electrical contacts with graphene sensing elements, liquid metal was put into microfluidic channels as interconnect material.
There could be an application for flexible strain sensors in wearable electronics, especially for monitoring purposes during sport and exercise. A flexible strain sensor of this type has already been developed by researchers using a graphene-based composite fiber with compression characteristics, which was integrated into wearable strain sensors. The sensor structure was made up of a highly elastic yarn consisting of polyurethane as the core fiber and polyester fibers as the scaffold.
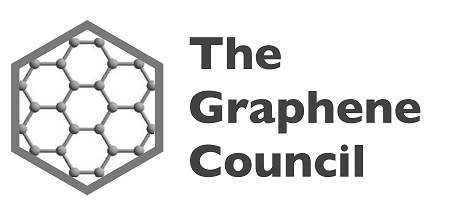
This information has been sourced, reviewed and adapted from materials provided by The Graphene Council.
For more information on this source, please visit The Graphene Council.