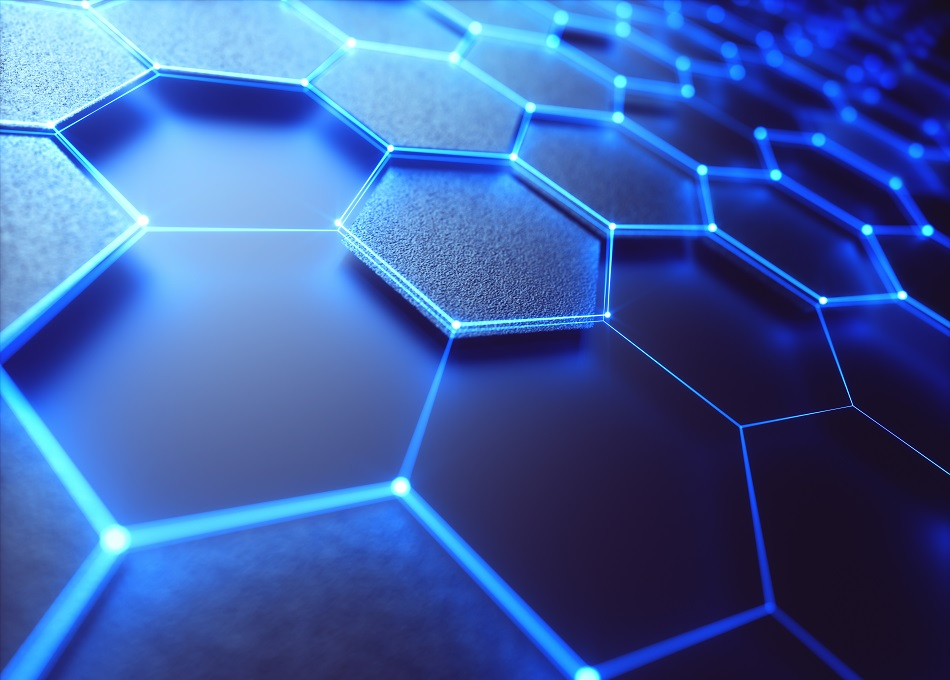
Image Credit: ktsdesign/Shutterstock.com
Dry exfoliation, also called mechanical exfoliation, is the process of splitting a layered material into atomically thin sheets. This type of exfoliation can be carried out both mechanically and electrostatically, as well as by using electromagnetism in air, a vacuum or inert environments.
In 2004, Dr. Andre Geim and Dr. Konstantin Novosolev at the University of Manchester first isolated graphene with the so-called “Scotch-tape” method. This method involves applying an adhesive tape to graphite and pulling it away to take off a single layer of graphene. It is still used today to obtain single atomic layer flakes.
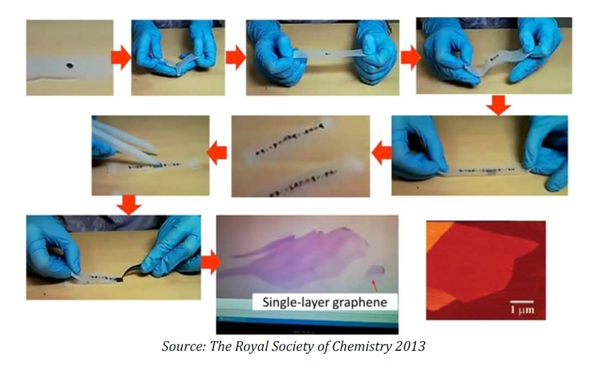
Figure 1. Illustration of Scotch-tape based micromechanical cleavage.
Dry Exfoliation Details
There are a number of different techniques and processes that can be used in order to split graphite into graphene. Micromechanical cleavage, anodic bonding, laser ablation, and photoexfoliation, dry ball milling, and detonation are common techniques for splitting graphite layers into several layers, or a single layer of graphene.
Micromechanical Cleavage
Micromechanical cleavage, also known as micromechanical exfoliation, has been used by crystal growers and crystallographers for decades. As early as 1999, researchers were using a type of micromechanical cleavage on graphite to create films of graphene made of several layers. For the most part, it was this method that allowed Geim and Novolselov to split graphite to obtain a single layer of graphene.
Since then, micromechanical cleavage has been optimized and can produce high-quality layers with their size limited by the single-crystal grains in the original graphite sample. However, micromechanical cleavage is not suitable for large-scale applications, but it is the method of choice when carrying out fundamental research on graphene in smaller batches.
The basic idea of mechanical cleavage is to separate the layers from the bulk highly ordered pyrolytic graphite (HOPG) surface. To perform the Scotch tape dry exfoliation method, Scotch tape is pressed onto a highly ordered pyrolytic (HOPG) surface and then pulled off very carefully. After numerous repetitions, the graphite layer becomes thinner after each pull until there is just a single layer of graphene left.
This particular method provides high-quality, large-area graphene flakes that have all of the valuable qualities that make graphene such a promising material for so many applications.
The main drawback of the Scotch tape method is that it is not scalable, and is limited solely to laboratory research. However, there is an alternative micromechanical technique inspired by the Scotch tape method. This method is called the three-roll mill machine technique and uses a polymer adhesive. You can see a schematic of this process in the Figure below.
In this process, polyvinyl chloride (PVC) is dissolved in dioctylphthalate (DOP) to generate the adhesive, which acts in the same way as the Scotch tape used in the method pre-dating this method, as micromechanical cleavage. Dispersion and exfoliation both occur in the adhesive, and while the three-roll mill machine is used widely in the rubber industry, meaning it is freely available for industrial production, it does make procuring pure graphene a challenge, as it leaves behind PVC and DOP.
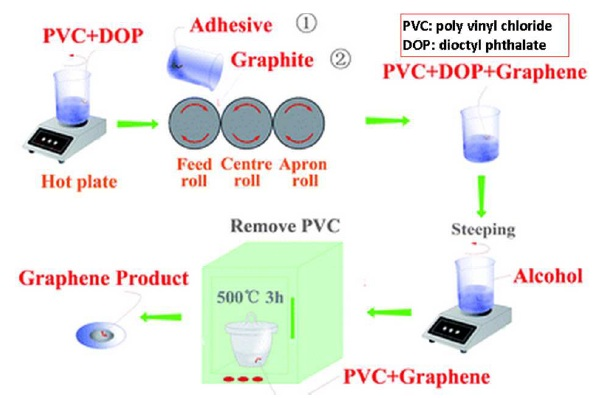
Figure 2. Schematic of the process of exfoliating graphene with a three-roll mill. Source: The Royal Society of Chemistry 2013.
Anodic Bonding
Anodic bonding is used by the microelectronics industry to bond silicon wafers to the glass to protect them from humidity and contamination. To carry out anodic bonding to produce graphene, graphite is pressed onto a glass substrate and a high voltage is applied between the graphite and metal back contact. After this, the glass substrate is heated.
During anodic bonding, a few layers of graphite stick to the glass through electrostatic interaction and can then be pulled off the glass. There are some variables, namely temperature, and applied voltage, used to control the number of layers. Reports have stated that the graphene flakes produced by anodic bonding are approximately a millimeter in width.
Laser Ablation and Photoexfoliation
Laser ablation uses a laser beam to remove material from a solid surface, and as a process to exfoliate graphene, is still early in its development and requires further research.
Photoexfoliation refers to cases when irradiation causes the detachment of an entire or partial layer.
In laser ablation, laser pulses are used to ablate and exfoliate graphite flakes to produce graphene. Controlling the laser energy can make it possible to determine the number of layers of graphene produced. Although the process has been carried out successfully in liquids, laser ablation works best when it is done in inert or vacuum conditions. Laser ablation performed in air can lead to the oxidization of the graphene layers.
Dry Ball Milling
Dry milling is another alternative to produce graphene. Graphite layers can be shifted by ball milling a mixture of graphite and chemically inert water-soluble inorganic salts. The ensuing water washing and sonication of the milling products can result in the production of graphene powders. There are also practical advantages to dry milling when the combined functionalization and exfoliation is required.
However, there are defects induced by the high-energy collisions from the grinding media. Despite this, the ball milling technique is still considered to be an intriguing method for large-scale production of graphene. The said defects induced by high-energy collision of grinding media are less clear, but the fragmentation and other defects cannot be avoided in the milling process.
There are both advantages and disadvantages to consider in the dry ball milling process and the defects that occur. On one hand, the process can be used to functionalize graphene and enables efficient exfoliation of graphite. On the other hand, dry ball milling will reduce the lateral flake size of the graphene and result in defects, in particular basal defects. The end use and application requirements of the graphene should be carefully considered when choosing dry ball milling as an exfoliation technique.
Detonation
The detonation technique for preparing graphene materials relies on a denotation-induced powerful shockwave and thermal energy for high-energy and violent exfoliation. Graphite oxide has often been used as a precursor in this extremely efficient process, and graphene oxide was produced instead of pristine graphene. To this date, there is no report of detonation producing pristine graphene.
Kansas State University physicists developed another form of detonation production using hydrocarbon gas, oxygen, and a spark plug. This alternative detonation process involves filling a chamber with acetylene or ethylene gas and oxygen. The mixture is ignited using a standard vehicle spark plug and the graphene material that results is collected. Chris Sorensen, a Cortelyou-Rust University distinguished professor of physics is the lead inventor and filed a patent titled, "Process for high-yield production of graphene via detonation of carbon-containing material."
Scalability and Market Position
The Scotch tape method is not suitable as a scalable production technique, but the other mechanical exfoliation techniques discussed may provide a promising starting point to beginning the scalable production of graphene. All of these techniques depend on essentially the same mechanism for exfoliation: shear or nominal force.
Despite their promise, there are issues remaining in all of these mechanical exfoliation techniques, in particular poor yield and the degree of exfoliation resulting in the fairly low yield of monolayer graphene. Additionally, all of these techniques cause fragmentation effects that complicate making large-area flake graphene a reality. However, there is still value in this form of graphene as an additive in composites and coatings.
Mechanical exfoliation techniques do pose more problems than those discussed above. There can also be uncontrollable defects, random sizes, and random numbers of layers of graphene, but this can be addressed through filtering and separation by lateral size and layer count.
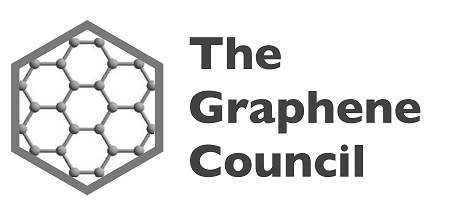
This information has been sourced, reviewed and adapted from materials provided by The Graphene Council.
For more information on this source, please visit The Graphene Council.