AZoNano speaks to Steve Wilcenski from BNNano about its cutting-edge boron nitride nanotubes, critical for the future of robust composite materials manufacturing.
Can you offer an overview of what BNNano does and how the company was established?
We are an advanced manufacturing company that produces the patent-pending NanoBarb™, a unique and enhanced boron nitride nanotube. When NanoBarbs are added to materials, it improves natural properties, changing them into extraordinary materials. We are focused on materials such as aluminum, polyester, and copper, and are seeking to transform, revitalize, and revolutionize industrial commodities.
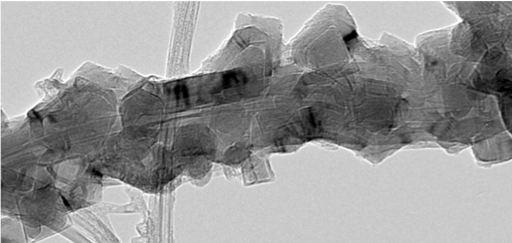
A transmission electron microscope (TEM) image of BNNano's NanoBarbTM. Image Credit: BNNano.
BNNano was formed in 2016 by myself (Steve Wilcenski) and Jason Taylor. Jason and I met in 2000 while working at Cree Inc. in Durham, North Carolina. We often discussed starting a company to make materials that would disrupt industries and provide game-changing solutions. We began to read research about boron nitride nanotubes and noted the tremendous potential for this material but a lack of boron nitride nanotubes' commercial sources. In 2015, we began to discuss how we could make it and grow a business around it.
We refined our plan, quit our jobs, and formed BNNano in 2016. We knew this was a risk, but we took the chance with the direct support of close family, friends, and angel investors.
In January 2017, we opened our manufacturing facility in Burlington, NC. We have been manufacturing Boron Nitride NanoBarbs™ and developing products that incorporate Boron Nitride NanoBarbs™ ever since. BNNano is currently the only company globally with a commercially viable manufacturing process for boron nitride nanotubes.
What are boron nitride nanotubes and how have they been used so far? What key features make them such unique and robust materials?
Boron nitride nanotubes are a nanomaterial that was first synthesized in the laboratory in the mid-90s. Since then, small quantities of boron nitride nanotubes have been made, and studies have shown how remarkable the material is.
Boron nitride nanotubes are electrically insulating and have a very high thermal conductivity - an extremely rare combination. They have oxidation resistance and are thermally stable >850 ◦C. They are of high strength and very elastic and flexible. BNNano is helping to establish and develop new commercial applications.
We are working with customers on a wide range of applications. Some customers are developing next-generation thermal management solutions to address the challenges of high-density and high-power electronics. For example, textile customers require stronger, tougher, and more fire-resistant polyester, while additive manufacturers are developing new materials for 3D printing applications.
We are supporting hypersonics, enhanced aluminum alloys, water purification, and many more. We have also shipped materials to all branches of the US military, NASA, and government labs worldwide. We are excited about our growing list of customers and their progress in completing new applications' development and qualifications.
Can you explain the differences between carbon nanotubes and boron nitride nanotubes?
Boron nitride nanotubes have a few key advantages over carbon nanotubes (CNT). Boron nitride nanotubes are structurally similar to CNTs. They are both shaped like hollow tubes or cylinders and have nanometer dimensions and are microns in length. They are both high aspect ratio nanomaterials. CNTs only have Carbon atoms, and boron nitride nanotubes have alternating boron and nitrogen atoms.
There are some key differences and advantages with boron nitride nanotubes. These include the following:
Boron nitride nanotubes are electrical insulators as well as excellent thermal conductors. CNT’s are electrical conductors, so they cannot be used in places where you need electrical shielding. This means boron nitride nanotubes can be used to cool electronics without causing electrical problems.
Boron nitride nanotubes can withstand higher temperatures (above 850 ◦C) than CNTs, which allows them to be added into materials such as metals and ceramics that need higher temperatures to be processed. High temperatures destroy CNTs.
Unlike CNTs, boron nitride nanotubes can also effectively absorb neutron radiation.
BNNano is the only company that currently has a commercially viable manufacturing process for boron nitride nanotubes. Can you explain the process and how it differs from other processes that have been developed?
We do not discuss the process as this is a closely guarded trade secret.
What we can say is that we thought about it differently from the beginning. Jason and I have a strong background in commercializing new technologies and taking things that have been done on a very small scale and developing ways to mass-produce them. When we took on the challenge to manufacture boron nitride nanotubes, we wanted to make a material that satisfied business requirements - to be low cost and high quality. We did not try to make a “perfect” material, we made an engineering material.
Can you offer a brief overview of BNNano’s Boron Nitride NanoBarbTM?
We wanted to solve or at least address the common problems seen in other nanomaterials such as carbon nanotubes, focusing on making an engineering material.
We looked for existing materials that make things stronger and immediately thought of rebar, which is used to make more robust concrete structures. Nanotubes have a relatively smooth surface, so we wanted to make the outside surface less smooth.
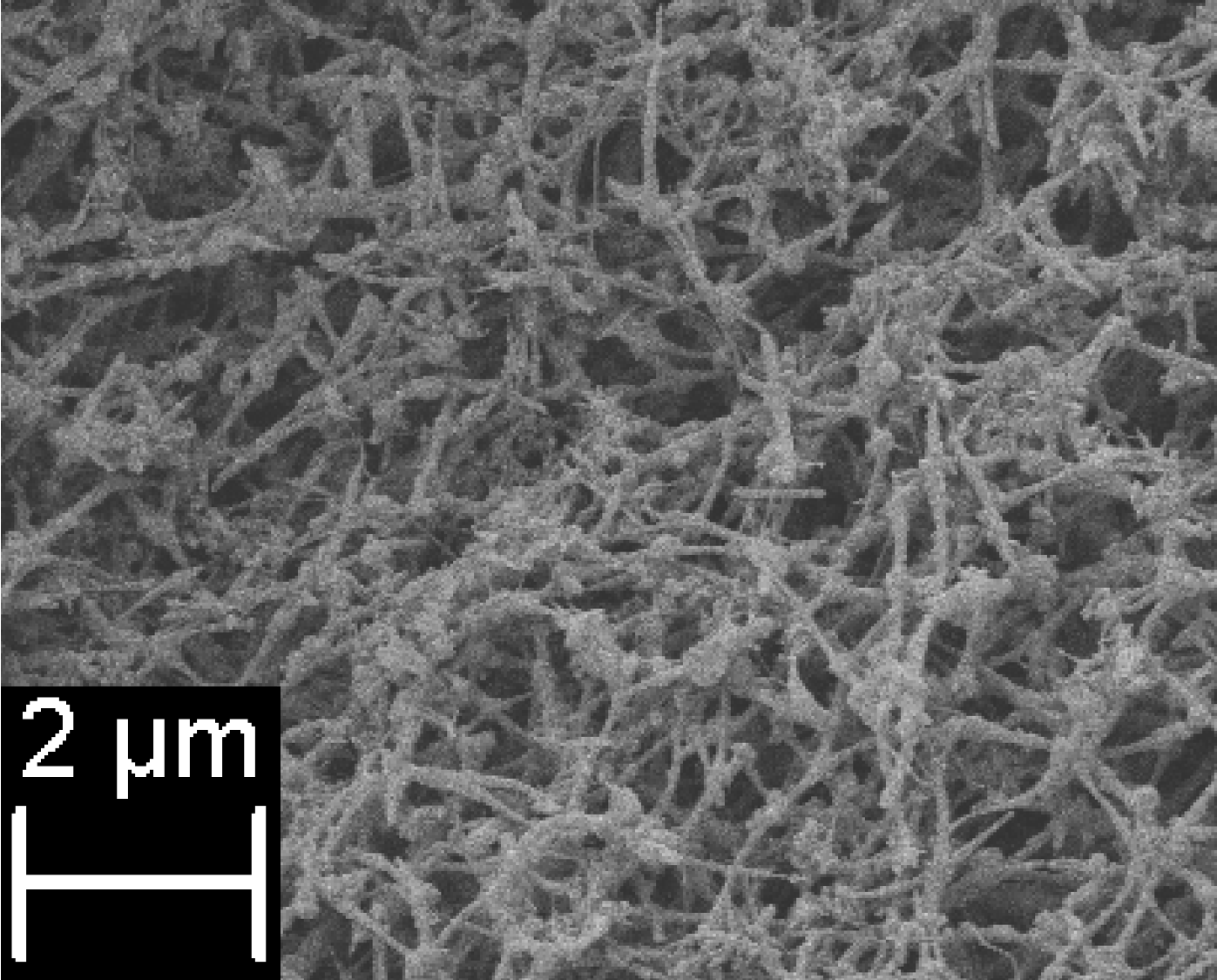
A scanning electron microscope (SEM) image of BNNano's NanoBarbTM. Image Credit: BNNano.
From our thin film and crystal growth experience, we thought of how rock candy is formed and how it looks. We set out to develop a way to nucleate crystals of another form of boron nitride. What we have with the NanoBarbTM is a boron nitride nanotube with nanocrystals of boron nitride on the outside, and it really does look like rock candy. This surface morphology of NanoBarbsTM provides a much better ‘connection’ to the material.
How are you able to develop high-quality boron nitride nanotubes at a low-cost?
When we developed our process, we spent a significant amount of time developing the supply chain and ‘bill of materials’ needed to manufacture our Boron Nitride Nanobarbs™. We also prepared for the cost curve reduction over time, so we rejected the common ways to make boron nitride nanotubes and only explored inexpensive ways to make high-quality material with easy expansion. We thought about the business side as much as the technology side.
How does the NanoBarbTM make polymers and composites tougher? How is this useful in applications such as defense?
We have been using additives to make things better and stronger for centuries. Think of the bricks used to build the pyramids. They added straw to the clay as a high aspect ratio additive to make the clay stronger. BNNano is doing essentially the same thing. When boron nitride nanotubes are added to polymers and composites, it augments what makes that material special. If an application requires a polymer for strength, when enhanced with NanoBarbs, it makes it stronger, and exponentially so. This allows you to use less material and retain the same capability.
Our material can do the same thing with aluminum. Think of what you could do for the military if you could reduce the amount of structural aluminum needed in land, air, or sea vehicles. What could you do if you used aluminum as ballistic protection in place of steel? What could you do if you could make polyester more like Kevlar? You would be on your way to making everything lighter, stronger, and faster.
How important is NanoBarbTM for the advancement of future technologies?
We think they are critical. Almost all industries' shared goal is to make things lighter, stronger, and faster, from microelectronics to automotive, space, and aerospace. As we push for new technologies such as hypersonic travel, advanced biomedical applications, and greener energy creation, we need new materials. Boron Nitride NanoBarbs™ can help advancements in all of those places.
What are the key industries and applications that BNNano’s Boron Nitride NanoBarbTM is used in, and how will it transform them?
We are focusing on developing our NanoBarb™ aluminum and copper but our technology is applicable to transforming a number of industries. Mobile electronics, defense, and aerospace are primary industries where our material is applicable and can revolutionize.
Our NanoBarbs™ can be used to improve thermal management of mobile electronic components, as well as make military equipment lighter, more corrosive resistant, and more blast-resistant. It is also used in particular aircraft parts to help make them hypersonic.
NanoBarbs™ are also applicable to the water filtration and fireproofing industries.
We also believe that NanoBarbs™ may be a key enabler in several industries such as next-generation rechargeable batteries and other industries.
We are not just focused on high-value applications. With our low costs, we are beginning to work in markets and applications that have traditionally been excluded from nanomaterials due to price issues.
Is there potential for this technology to be adopted worldwide? What are the challenges that may be faced, and how could these be overcome?
Yes, as production volumes increase and other providers come online, many potential applications can be addressed.
Right now, the challenges are supply and cost. We will continue to expand our capacity to address the growing demand. However, to service worldwide demand, we expect there will need to be new entrants to the marketplace.
What is BNNano’s biggest industry goals, and what steps will be taken to achieve them?
Our goal is to continue to improve the quality and reduce the cost of our materials. As we continue to lower costs, we can introduce our material into more industries and applications. These new applications drive demand and the need to expand and grow. We are planning a major production expansion in 2021.
It is our vision that we will be able to aggressively grow BNNano and bring manufacturing jobs back to the US.
Where can readers find more information?
www.bnnano.com
About Steve Wilcenski
Steve Wilcenski is the CEO and one of the founders of BNNano. For over 20 years, Steve has been an active member of teams designing and developing technologies and products on the micro and nanoscale. These technologies have been implemented in human bodies, have explored the surface of Mars, and have left the solar system.
Many of these products have enabled disruptive technologies for markets, including Defense, Aerospace, Biomedical, Automotive, Communications, and Consumer Electronics.
Before co-founding BNNano, Steve was the President and General Manager for the MEMS Business Unit of MEMSCAP, SA. Steve earned a B.S. in Material Science and Engineering from North Carolina State University, an M.S. in Chemistry from Clemson University, and an MBA from North Carolina State University.
Disclaimer: The views expressed here are those of the interviewee and do not necessarily represent the views of AZoM.com Limited (T/A) AZoNetwork, the owner and operator of this website. This disclaimer forms part of the Terms and Conditions of use of this website.