Jan 14 2016
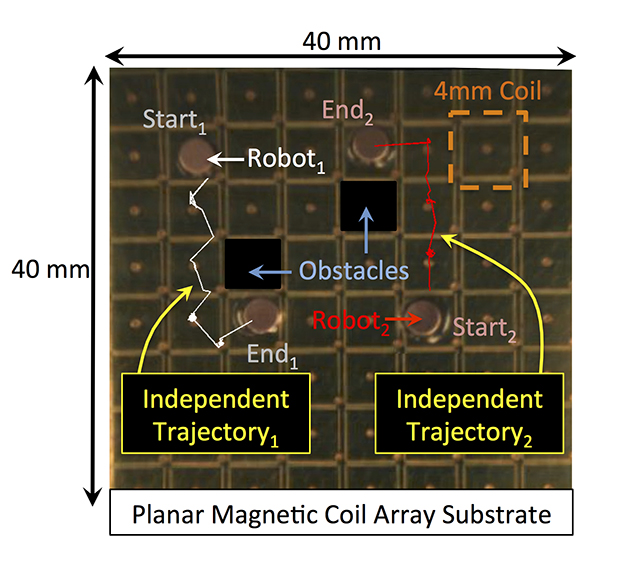
Image Credit: Purdue University image/David Cappelleri
Researchers from Purdue University are using a technology likened to "mini force fields" to independently control individual microrobots operating within groups, an advance aimed at using the tiny machines for manufacturing and medical applications.
The overall aim is "to be able to control them individually so we can have some robots here doing one thing, and some robots there doing something else at the same time."
The team developed a system for controlling the robots with individual magnetic fields from an array of tiny planar coils. The reason for this is down to the size of the robots meaning that they can't power themsleves.
The magnetic fields act as an external source of power however, the question is then about how these robots can be individually programmed.
We need to know, if a robot is here and it needs to go there, how much force needs to be applied to the robot to get it from point A to point B? You can think about using teams of robots to assemble components on a small scale, which we could use for microscale additive manufacturing.
David Cappelleri - Purdue University
The coils are made by printing a copper pattern with the same technology used in the manufacturing of printed circuit boards. They can be scaled to about four millimeters.
Independently controlled microbots working in groups might be useful in building microelectromechanical systems, or MEMS, minuscule machines that could have numerous applications from medicine to homeland security.
Cancer cells have different stiffness characteristics than non-cancer cells, and in some of our previous work we put force sensors on the end of these robots to figure out which ones are stiffer than others.
David Cappelleri, Purdue University
Research is still ongoing with attempts to use microscale prototypes to assemble components for MEMS devices.
Localized Magnetic Field Control for Microrobots