Probably one of the most famous art sculptures in the world recreated in an entirely new perspective: Thanks to significant advances in the development of the CERES additive micro-manufacturing system, Michelangelo’s David exists now in the size of a little ant.
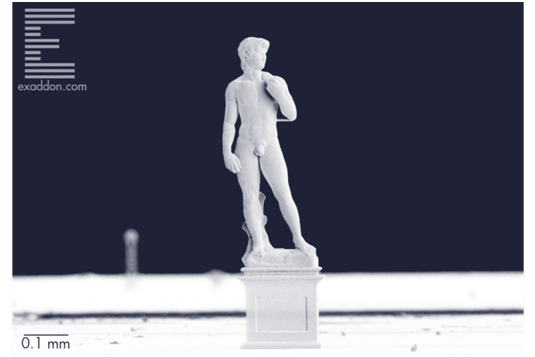
During the creative period of Michelangelo (lived 1475-1564) it must have been a huge effort to craft the David sculpture from a solid marble block. The creation and handling of the heavy and bulky work of art must have required some well-thought-through handling processes.
The work presented here required much less effort in terms of handling because the new “David” is tiny in size. However, the engineering behind might have required a similar amount of effort as 500 years ago for the original full-scale David.
Over the last two years, the ongoing development of the CERES hardware and especially that of the printing process has led to the ability to additively manufacture metal objects, from the size of small bacteria to little ants. Thanks to these advances, we can present probably one of the most famous art sculptures in the world in an entirely new perspective: David from Michelangelo is now available in pure copper and on a microscopic scale.
“It is more than just a copy and downsized model of Michelangelo’s David”, says Dr. Giorgio Ercolano, R&D Process Engineer Exaddon AG, who made the minuscule model. “Our deep understanding of the printing process has led to a new way of processing the 3D computer model of the statue and then converting it into machine code. That’s what makes the new David statue so extraordinary.” Dr. Ercolano explains: “This object has been sliced from an open-source CAD file and afterwards was sent directly to the printer. This slicing method enables an entirely new way to print designs with the CERES additive micromanufacturing system.” The “David” is the largest object created by the new additive manufacturing method from Exaddon AG so far.
Tiny David. With the CERES in microscale and with copper additively manufactured David from different perspectives.
CERES, the additive micromanufacturing system
The CERES printer is a stand-alone system that prints complex pure metal objects at the nanometer to micrometer scale with pinpoint accuracy aligned on existing objects or surfaces. The amount of metal printed ranges from 1 μm3 to 6'000'000 µm3 per structure, a range that is unobtainable by most other techniques.
The printing technology, originally invented at ETH Zurich, uses a tiny pipette with a 300-nm-wide opening to do local electrodeposition of metals, in this case copper. The hollow nanopipette is brought into proximity (~1 µm) of a conductive surface and a metal ion-containing liquid is dispensed. A negative potential applied to the surface reduces the delivered copper ions to solid atoms, which deposit just below the pipette opening. Once the gap between surface and pipette is filled with the solid copper atoms, the pipette moves to the next position, repeating the deposition and like this, a 3D object is created.