A team of researchers recently published a paper in the Journal of Micromechanics and Microengineering that successfully demonstrated the effectiveness of the nanograss technique in enhancing the adhesion of Parylene C substrate, a frequently used polymer in micro-electromechanical systems.
Study: Adhesion enhancement strategy for Parylene C substrate by nanograss technique. Image Credit: Jack Soldano/Shutterstock.com
Where is Parylene C Used?
Parylene is primarily used in the aerospace, biomedical, and electronics industry owing to its excellent biocompatibility and barrier properties.
Parylene C is used most extensively among all Parylene variants owing to its manufacturing advantages. Specifically, the polymer is considered the most suitable choice as an encapsulation layer in micro-electromechanical systems (MEMS) devices owing to its pinhole-free and conformal coating behavior at room temperature.
However, a number of limitations, such as the weak adhesion between Parylene C and other materials, are hindering the use of Parylene C in MEMS. Weak adhesion of Parylene C also restricts the long-term application of the polymer in wetting processes such as potassium hydroxide (KOH) etching. Chemical and mechanical approaches can potentially help in overcoming the limitation.
Chemical approaches involve the modification of the polymer surface or the introduction of an interlayer with chemicals, while mechanical approaches involve the fabrication of additional mechanical structures on the surface to enlarge the volume/surface ratio without using any chemicals.
The mechanical approach is considered more suitable than the chemical approach as it does not lead to any changes in the surface properties, such as crystallinity and phase, of Parylene C. Additionally, chemical approaches lack universal applicability as the use of additional materials can hinder process compatibility owing to containment.
In previous studies, a metal or silicon (Si) was mostly used as a substrate layer in place of a Parylene to investigate the adhesion enhancement through the mechanical approach.
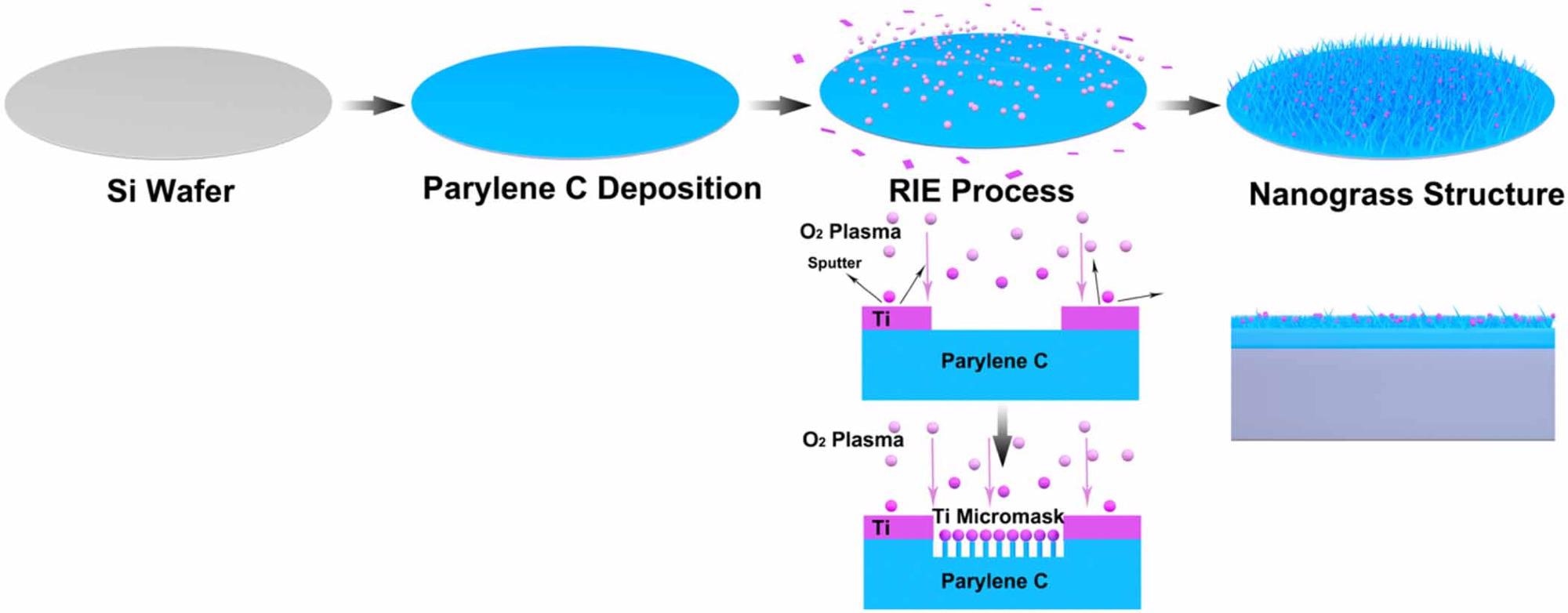
Figure 1. Fabrication process of the nanograss structure. © Xu, H., Jin, Y., Chen, L. et al. (2022)
The Nanograss Technique
In this study, researchers initially introduced a short-time oxygen plasma reaction ion etching (RIE) process with titanium (Ti) in the etching chamber between the first layer of Parylene C film deposition/the substrate and the second layer of metal or Parylene C coatings to enhance the adhesion between Parylene substrate and metals or Parylene.
Certain parameters in the RIE process that include etching times, oxygen plasma flowrate, and radio frequency (RF) power were varied to tune the nanograss feature size and density. Later, they investigated the effectiveness of their method by performing scratch tests to quantitively evaluate the adhesion strength of the prepared samples.
Surfactant-coated Si wafers were utilized as the substrate for the deposition of Parylene C to easily separate the Parylene C to metal (P-M) and Parylene C to Parylene C (P-P) bilayer structures. A commercial SCS PDS2010 deposition equipment was used to perform the Parylene C deposition.
A Parylene C substrate along with a Ti mask on its top was prepared, and then oxygen plasma etching was carried out on the prepared sample in an RIE chamber. A Keysight G200 nano-scratch tester was employed to measure the interfacial adhesion between P-M and P-P in ambient air and at 20% humidity and 25 °C temperature.
Scanning electron microscopy (SEM) analysis was performed to characterize the fabricated nanograss.
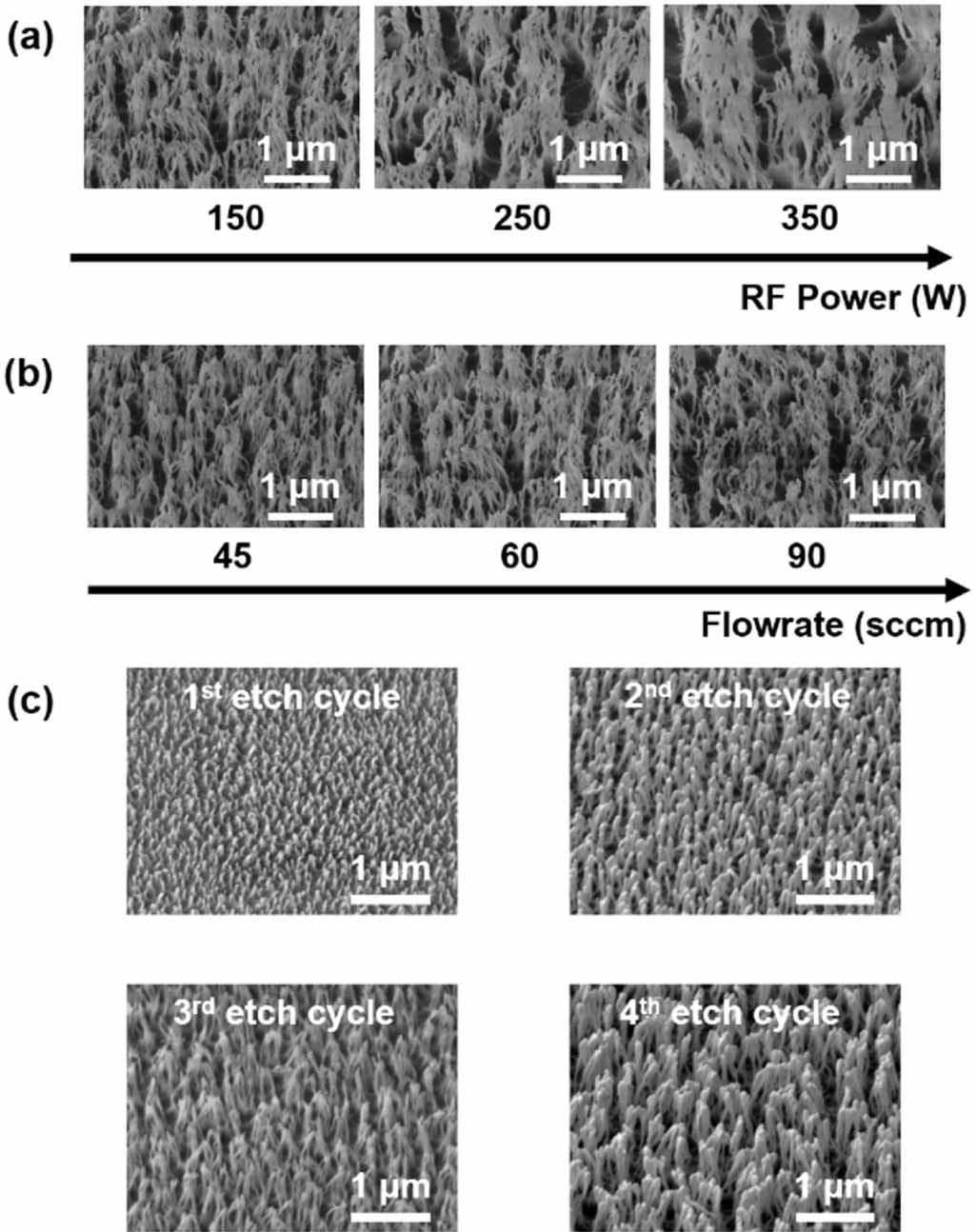
Figure 2. SEM images of the nanograss structures. (a) RF power affected nanograss and (b) flowrate affected nanograss. (c) Nanograss with variable etching cycles. © Xu, H., Jin, Y., Chen, L. et al. (2022)
Observations
The RIE process led to the successful fabrication of Parylene C nanostructures/nanograss on the Parylene C substrate owing to the oxygen plasma bombarding, along with the generation of sputtered nanoparticles as nanomasks.
The Ti nanoparticles were sputtered off during the oxygen plasma etching process and deposited on the Parylene C films to form micro-masks. Eventually, Parylene C nanostructures/nanograss were formed on the top of the Parylene C film. Multiple nanograss feature sizes were obtained successfully by tuning the oxygen flow rate, etching times, and RF power.
The density and feature size of the nanograss remained unchanged at different RF power values of 350 W, 250 W, and 150 W with fixed etching time and oxygen flowrate. Thus, the low RF power of 150 W was selected as ideal for nanograss preparation.
At 150 RF power and a fixed etching time, the density and size of the nanograss structures remained the same at oxygen flow rates of 90, 60, and 45 sccm. However, the 45 sccm oxygen flowrate was found unsuitable for long-term etching. Thus, 60 sccm was selected as the optimal oxygen flowrate to fabricate nanograss.
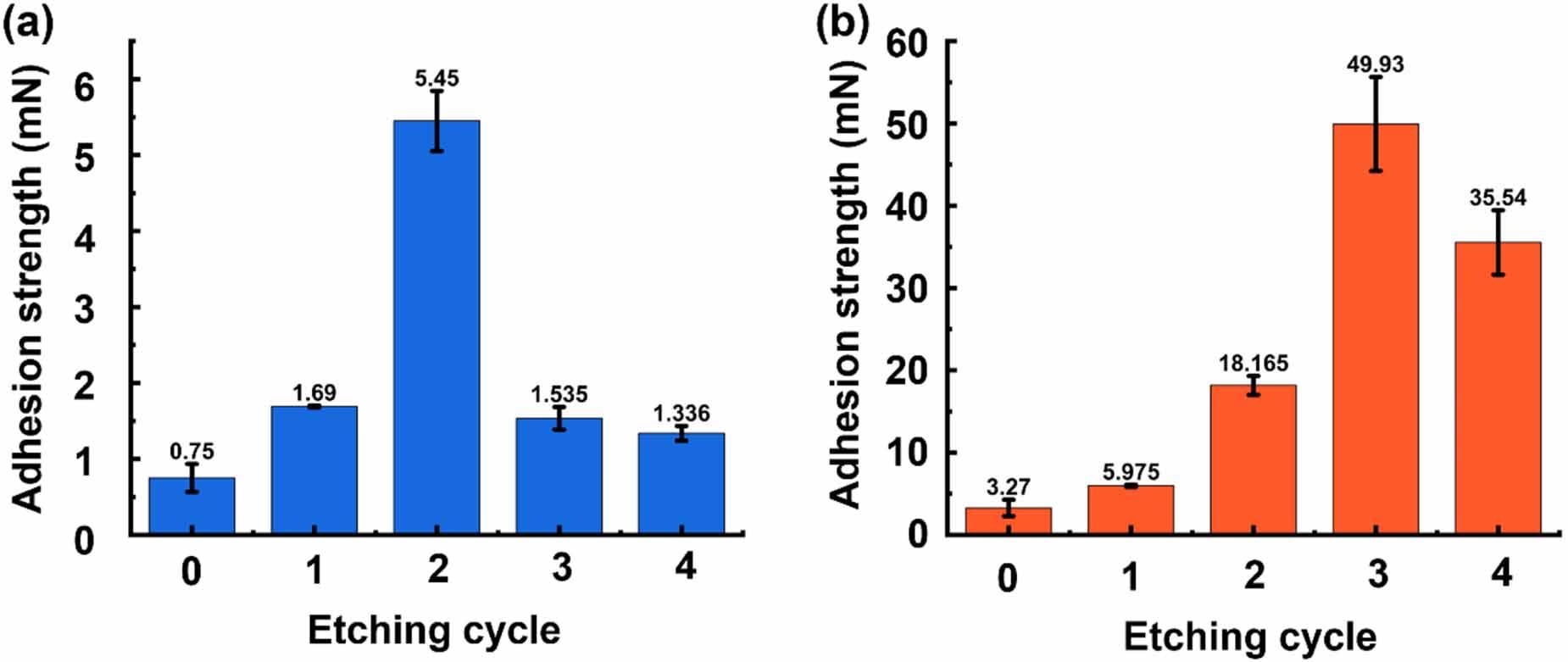
Figure 3. Interfacial adhesion results as a function of different etching cycles. (a) P-M and (b) P-P. © Xu, H., Jin, Y., Chen, L. et al. (2022)
Finally, the size and density of the nanograss were determined at 60 sccm oxygen flowrate and 150 W RF power with different etching times. An etching for 75 s was considered as one cycle, and the etching times ranged from 1 to 4 cycles.
The size of the nanograss increased considerably while the density decreased with the rising number of etching cycles. The observations indicated that both nanograss density and size were directly proportional to the etching time with low oxygen flowrate and RF power.
The adhesion strength was maximum with smaller etch cycles of P-M samples. Scratch test results demonstrated that the adhesion in Parylene samples treated with nanograss enhanced substantially compared to the untreated Parylene samples, with P-P samples showing greater adhesion than P-M samples.
Taken together, the findings of this study demonstrated that the precisely controllable, chemical-free, robust, and easy-to-realize adhesion enhancement approach based on the nanograss technique can be used effectively in different Parylene MEMS applications.
Reference
Xu, H., Jin, Y., Chen, L. et al. (2022) Adhesion enhancement strategy for Parylene C substrate by nanograss technique. Journal of Micromechanics and Microengineering. https://iopscience.iop.org/article/10.1088/1361-6439/ac57ae
Disclaimer: The views expressed here are those of the author expressed in their private capacity and do not necessarily represent the views of AZoM.com Limited T/A AZoNetwork the owner and operator of this website. This disclaimer forms part of the Terms and conditions of use of this website.