Graphene meta-aerogels with multiple functions have shown great promise for future domestic and military applications. In a study published in Nature Communications, a laser-engraving approach for producing graphene meta-aerogels with unique properties was demonstrated.
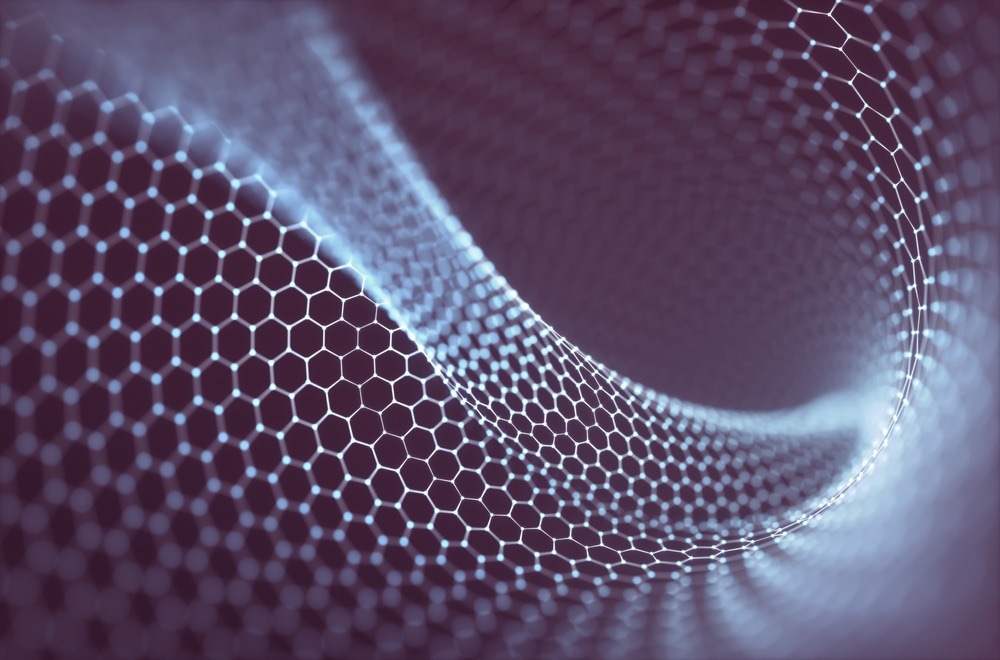
Study: Superelastic graphene aerogel-based metamaterials. Image Credit: ktsdesign/Shutterstock.com
What are Graphene Meta-Aerogels?
Three-dimensional graphene meta-aerogels derived from their allotropic monoliths, such as sponges and foams, have emerged as highly appealing carbon-based metamaterials. They possess remarkable qualities like superior compressibility, ultralight weight, and excellent electric conductance and thermal insulation.
Main Challenges for Graphene Meta-Aerogels
There are significant difficulties in achieving novel features in graphene meta-aerogels. For example, the absence of multiscale morphological control from tunable macro- to well-arranged micro-structures limits graphene meta-aerogels use in applications like wearable electronic devices, soft robotics, and stimuli-sensitive systems.
Figure 1. Traditional engraving and laser-engraving for graphene aerogels (GAs) with arbitrary geometries. a Schematic illustration of traditional engraving for tools and artwork, such as a pair of chopsticks, a bowl, and a sculpture of steed. b Schematic illustration of laser-engraving on GA with arbitrary shapes. c The peony flower pattern of GAs with fine structures as small as a fifty cents coin after laser-engraving. d The pieces of GAs with elaborate shapes and rabbets can be reversibly assembled into a stereoscopic eagle. e The GAs with serpentine structure, stretched reversibly with 1200% tensile strain. f The GAs with re-entrant structure, showing reversible strains of 133%. g The spiral GAs stretched reversibly with 900% and even up to 5400% tensile strain. © Wu, M., Geng, H. et al. (2022).
Synthesis Methods for Graphene Meta-Aerogels
Freeze-drying is a commonly used process for defining the macrostructure of graphene meta-aerogels. This method can help obtain graphene meta-aerogels having the natural appearance of molds, which may to some degree organize the configurations of graphene layers, resulting in porous, cellular, and hyperbolic frameworks.
With this approach, however, achieving exact and particular forms with superior performance is challenging.
3D printing is another interesting extrusion approach for producing lattice and periodic graphene meta-aerogels with configurable architectures. Nonetheless, the requirement for using a high content of graphene oxide (GO) distribution for achieving adequate viscosity poses a constraint in downsizing the printed structures.
Achieving High Stiffness and Elasticity in Graphene Aerogels
The macro-mechanical characteristics of graphene meta-aerogels are heavily influenced by their internal microstructure. Graphene meta-aerogel deformation involves three operations in the order of linear elasticity, collapsing, and densification during the compression phase, as per the open cell model.
When the walls of graphene reach their peak bending moment and ultimately collapse, micro-scale hinges are formed.
The bending stiffness of graphene walls (GWs) directly impacts the elastic modulus of a graphene meta-aerogel. Therefore, attempts have been undertaken to increase the bending stiffness of GWs using hydrothermal processing, molecular cross-linkages, and polymeric reinforcement to achieve higher stiffness and elastic modulus in graphene meta-aerogels.
Unfortunately, the specific bending stiffness of a film-like structure is fundamentally lower than that of a fibrillar or tubular material.

Figure 2. Fabrication and structure of graphene meta-aerogels (GmAs). a Schematic illustrations of fabrication procedures of the GmAs and a leaf with the optical photograph of the leaf skeleton. b TEM image of the graphene oxide (GO) sheets covering polyimide (PI) nanofibers. c–e The cross-section SEM images of GmAs at different scales. f Three GmAs support weight over 6000 times their weight without any macroscopic deformation. g A GmA (2 cm × 2 cm × 1.8 cm) stands on Setaria viridis. © Wu, M., Geng, H. et al. (2022).
Research Methodology
The team demonstrated a laser-engraving approach for producing graphene meta-aerogels with multi-functional macro-scale architectures and highly organized microscale frameworks in this study.
Graphene meta-aerogels could be quickly formed into various shapes, such as linear, planar, and three-dimensional lattice structures and hole bulks.
Graphene meta-aerogels have microscopic structures made up of interwoven sub-micrometer fibers and graphene films. The one-dimensional nanofiber-reinforced 2D film structure significantly increases the bending stiffness of GWs.
The facile fabrication method enabled the insertion of various functional elements into the structure, allowing for manufacturing items with pre-determined geometries and functionalities.
The team developed magnetically responsive aerogels and ceramic aerogels as prototypes, demonstrating a solid potential for multi-functional usage.
Important Findings of the Study
In this research, the team presented a laser-engraving approach for fabricating graphene meta-aerogels with distinct properties and multiple functionalities. They achieved this by using a one-dimensional nanofiber-reinforced 2D film structure.
This research uncovered a facile method for precisely regulating the graphene meta-aerogel structures from optimizable macro-scale to well-arranged micro-scale configurations.

Figure 3. Laser engineering meta-structures of GmAs with appealing properties. a The specific weight distributions of GmAs after laser-engraving. The pictures give specific weight and shapes of different GmAs. b a GmA (3.3 cm × 2.7 cm × 1 cm) with the ultralight specific weight of 0.1 mg cm−3 can overcome the gravity relying on the electrostatic force. c Photographs of the GmA (3.3 cm × 2.7 cm × 1 cm) with specific weight of 0.1 mg cm−3 before and after 50 compression cycles at 80% strain. d The snapshots of GmAs (0.8 cm × 0.5 cm × 0.8 cm) with different configurations during uniaxial compression, The snapshots of GmAs (0.8 cm × 0.5 cm × 0.8 cm) with different configurations during uniaxial compression, concave-shaped configuration (GmA−1.2) (upper row), pristine configuration (GmA) (middle row), and convex-shaped configuration (GmA+6) (lower row). e The finite element calculation shows the compression process of samples of concave-shaped (GmA−1.2) and convex-shaped (GmA+6) configurations, and the color reflects the distribution of displacement magnitude. f The Poisson’s ratio variations of GmA±n during uniaxial compression. ± represents the positive or negative Poisson’s ratio behavior of GmA. n means the n mm of major axis of the ellipses in the GmA, representing the changing hole size. g The snapshots of cross-section views of the GmA (0.8 cm × 0.5 cm × 0.8 cm) of the left and right asymmetry configuration and the finite element simulation process during compression process. h The snapshots of cross-section views of GmA (0.8 cm × 0.5 cm × 0.8 cm) of the upper and lower asymmetry configuration and the finite element simulation process during compression process. Source data are provided as a Source Data file. © Wu, M., Geng, H. et al. (2022).
The internal one-dimensional nanofiber-reinforced 2D frameworks guaranteed a steady bulk deformation mechanism, resulting in a considerable increase in flexibility, durability, and stiffness.
The laser-engraving approach produced arbitrary architectures of graphene meta-aerogels with exceptional properties, including high elasticity, considerably low specific weight, and a broad Poisson's ratio range.
In the compression phase, the interior deformation mechanism of graphene meta-aerogels was a steady bulk deformation instead of the micro-scale buckling observed in soft graphene aerogels. Therefore, graphene meta-aerogels outperformed the majority of carbon aerogels because of their excellent durability, stiffness and strength, and complete shape recovery following arbitrary compression.
The proposed technique may introduce polymers and particles into the framework, producing items with pre-determined forms and functions.
With the development of graphene meta-aerogels with exceptional capabilities, this study paves the way for the future development of multi-purpose aerogels with customizable meta-structures.
Reference
Wu, M., Geng, H. et al. (2022). Superelastic graphene aerogel-based metamaterials. Nature Communications, 13. Available at: https://www.nature.com/articles/s41467-022-32200-8
Disclaimer: The views expressed here are those of the author expressed in their private capacity and do not necessarily represent the views of AZoM.com Limited T/A AZoNetwork the owner and operator of this website. This disclaimer forms part of the Terms and conditions of use of this website.