The carbon nanotube and nanomaterials tool innovator Surrey NanoSystems is taking its 'next-generation semiconductor tool' message to the Asian semiconductor industry at nanotech 2008.
"There are fundamental barriers to progress in semiconductor integration, because of the need to find viable processes for next-generation interconnect and dielectric applications," says Duncan Cooper of Surrey NanoSystems. "Surrey NanoSystems has developed carbon nanotube processes and a nanomaterial deposition tool with the precision and repeatability necessary for these critical applications."
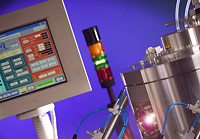
"Our presence at nanotech 2008 gives us an opportunity to meet with leading companies in the field, and we are additionally part of a JETRO* program to establish high-level contacts with key Japanese firms in this field," he adds.
Surrey NanoSystems' NanoGrowth tool for fabricating carbon nanotube and nanomaterial structures has an extremely high degree of precision and repeatability plus the ability to grow materials at low temperatures that are compatible with commercial semiconductor processes.
"The tool's intrinsic modularity allows users to gain automated control over all aspects of nanomaterial synthesis" adds Duncan Cooper. "We are able to discuss the processing techniques and results that the company has gained from our development partnership with the University of Surrey's Advanced Technology Institute, plus a parallel agreement that we have in place with a major laboratory that is helping us with independent test-bed services for our unique processes. We will bring our approach to high volume manufacture in tools aimed at the 32 nm process node and beyond."
The company's first tool is NanoGrowth 1000n, and comes with both CVD (chemical vapour deposition) and PECVD (plasma-enhanced CVD) processing capability. These two techniques provide great processing versatility for users. Among many quality-oriented architectural features are an ultra-high purity gas delivery system and flexible closed-loop control systems that allow users to define target tolerances to achieve a high level of repeatability during all phases of the process. Field-proven carbon nanotube fabrication programs are provided with the tool in the form of software templates that may be adapted easily by users for their own applications.
A high degree of hardware modularity further extends the capability of the tool's design, as it facilitates easy expansion and configuration to meet current and future fabrication requirements. Among many options are further processing techniques such as ICP (inductively coupled plasma), dual sputter sources for catalyst deposition - including a module for delivery of vapour-phase catalysts like ferrocene - and modules to add process stages for automated pilot production or high throughput. Included in the latter category are an automated wafer transport load/lock system, integrated etching capability, and a PECVD module for deposition of thin-film silicon-based materials.