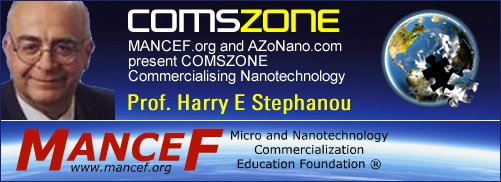
Abstract
Assembly, packaging, and testing activities account for 85% of the cost of many microsystems. This is primarily due to the lack of backend standards or general methodology. This presentation focuses on concurrent microengineering and the need for designing for micromanufacturability. Specifically, how to design a microsystem so that it can be assembled, packaged, and tested with high yield, low cost, and short cycle time with low volume automation. The goal is for the product to be designed concurrently with the fabrication process and the assembly work cell. Special attention is devoted to tolerance analysis, error propagation, and their impact on product performance. We present a rigorous mathematical framework and its implementation into a software tool that allows the designer to rapidly evaluate tradeoffs among cost, cycle time, and yield. We will illustrate how The Texas Microfactory™ is using this unique proprietary tool for pilot production of complex microsystems.
Introduction
Recently, increasing market inclination towards low-cost portable systems with complex functionality has opened up great avenues for miniaturization technology. Unlike the past surface-micromachined and monolithically fabricated MEMS products, newer microsystems have significantly grown in design complexity as well as material heterogeneity. In order to address these issues, alternative production technologies are being investigated rigorously. Assembly in micro-domain is a pioneering concept that sets new paradigms for manufacturing of robust, low-cost, and mass-producible microsystems. This is achieved through simple designing of heterogeneous micro-components followed by precise manipulation and assembly of these components to construct the envisaged complex system.
However, assembly based manufacturing of microsystems poses several unique challenges due to certain intrinsic reasons such as unavailability of standards for component design and fabrication, stringent tolerance budgets, workspace constraints, and surface effects due to scaling. Consequently, selectivity of manipulation systems, sensors, control schemes, and automation can result in a significantly large number of iterations in establishing the production cycle for an acceptable yield, which renders the manufacturing process hugely expensive and time consuming.
At ARRI's Texas Microfactory™, we exercise a holistic approach towards microscale manufacturing where, using a complex mathematical framework, different aspects in pilot production are evaluated concurrently to estimate the cost functions such as yield, throughput, cost, and performance. Using an indigenously developed iterative software tool, an acceptable combination for these cost functions is searched for and the corresponding input parameters are selected for the manufacturing process.
Results
|
Figure 1. ARRI's microspectrometer consisting of Silicon MEMS parts, glass ball lenses and beamsplitter cube, IC laser source and detector integrated on 1cmx1cm silicon die with device resolution of 5nm for visible wavelength and 25nm for near infrared wavelength.
|
Table 1: Cost function comparison for microspectrometer manufacturing
Parameters |
Projections for a pure open loop control based assembly
|
Projections for a pure closed loop control based assembly
|
Projections for a custom designed hybrid control scheme
|
Overall Yield |
20%
|
99.9%
|
92.5%
|
Cycle time |
6 - 10 minutes
|
50 - 80 minutes
|
20 - 35 minutes
|
Sensors requirement |
0
|
4
|
2
|
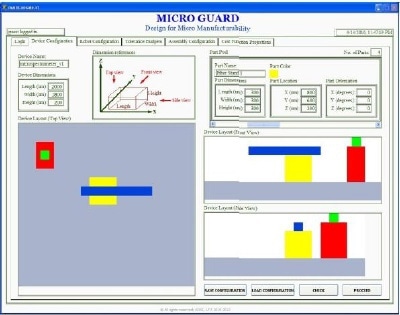
|
Figure 2. Snapshots of the software tools for design for micromanufacturability: (top) manufacturing cost function estimator, (bottom) process simulator in virtual 3D.
|
Copyright AZoNano.com, MANCEF.org
Disclaimer: The views expressed here are those of the author expressed in their private capacity and do not necessarily represent the views of AZoM.com Limited T/A AZoNetwork the owner and operator of this website. This disclaimer forms part of the Terms and conditions of use of this website.