Transparent conductive thin films are crucial in various semiconductor devices, including solar cells, liquid crystal displays (LCDs), light-emitting diodes (LEDs), and sensors. Indium tin oxide (ITO) is a popular choice for these applications due to its excellent electrical conductivity, optical clarity, and unique nonlinear properties. Various methods can be used to create ITO thin films, such as magnetron sputtering, thermal evaporation, plasma ion-assisted evaporation, and activated reactive evaporation. Among these, sputtering is particularly favored for producing films with a dense structure and high transparency.
The electrical resistivity in ITO determines its efficiency as a conductor, directly impacting the performance of devices into which it is integrated. A material with suboptimal resistivity may cause excessive heat dissipation and degrade the device's overall reliability, leading to inefficiencies or failures in electronic and photonic applications. As such, understanding the factors that influence ITO resistivity, such as film thickness, grain size, composition, and deposition techniques, ensures that the material can be tailored for specific applications, providing the optimal balance between electrical conductivity and optical transparency.
This article presents a study on the electrical resistivity in sputtered ITO films. Nine ITO films of varying thicknesses were prepared under identical growth conditions, achieving a growth rate of 1.43 nm/s. The electrical resistivity of the ITO films was then determined by measuring their thickness and sheet resistance, where observed variations in resistivity and film thickness across the wafer correlated to growth conditions. For a similar study that analyzed ITO film stress and grain size, please refer to this previously published article, “A Review of Thickness-Dependent Stress in Indium Tin Oxide (ITO) Thin Films”.
Surface Metrology Techniques
The resistivity of a conductive film can be calculated using the following equation:
ρ = Rs • tf
where ρ is the resistivity, Rs is the sheet resistance, and tf is film thickness.
Figure 1 shows the surface metrology techniques used in the electrical resistivity measurement. To evaluate the resistivity of ITO films deposited on a glass substrate, the film thickness and sheet resistance must be measured. These parameters can be measured using a spectral reflectometer and a four-point probe (4PP), respectively.

Figure 1. Surface metrology techniques used in the electrical resistivity measurement. Image Credit: KLA Corporation
The thickness of the ITO films was measured using a Filmetrics® F50-UVX reflectometer from KLA Instruments™, which utilizes a light source covering wavelengths from 190 - 1700 nm. This setup enables thickness measurements ranging from 5 nm to 250 µm with an accuracy of ± 1 nm. The ITO film sheet resistance (Rs) was determined using the Filmetrics® R50 four-point probe (4PP) system.
Electrical Resistivity of ITO
Figure 2a shows the thickness map for the thickest ITO film, measured using a 115-point map across the entire 100 mm diameter wafer, excluding a 5 mm edge. The center thickness is 615 nm, while the edge thickness is 510 nm. The thickness gradually decreases from the center to the edge, forming a circular distribution due to the sample's rotation during deposition.
Figure 2b shows the sheet resistance (Rs) map of the same wafer, showing that the center and the edge exhibit high resistance, approximately 4.6 Ω/sq, while the area in between has the lowest Rs, around 3.3 Ω/sq. According to the equation ρ = Rs x dITO, if the ITO film had uniform resistivity across the wafer, Rs should be inversely proportional to the film thickness. However, a monotonic change in Rs from the center to the edge was not observed. This discrepancy between the ITO thickness map and the Rs map suggests a variation in ITO resistivity from the wafer center to the edge.
Figures 2c and 2d depict the thickness and sheet resistance maps from a thinner ITO sample. The ITO thickness ranges from 75 – 89 nm, decreasing from the center to the edge. The sheet resistance at the wafer edge is high, at 116 Ω/sq, while it decreases to 25 Ω/sq toward the center. The center of the wafer shows an Rs value of approximately 50 Ω/sq.

Figure 2. (a) Thickness map and (b) sheet resistance map of ITO film on glass with a thickness of 615 nm at the center. (c) Thickness map and (d) sheet resistance map of ITO film on glass with a thickness of 89 nm at the center. Image Credit: KLA Corporation
To better understand the spatial distribution of the ITO thickness dITO and the sheet resistance Rs, and to calculate the point-to-point resistivity ρ, we conducted line scans of dITO and Rs across the wafer for all nine ITO samples. The line scans were performed from X = -45 mm to X = 45 mm at 1 mm intervals.
Figure 3a shows the line scan of the ITO thickness for all nine samples. The ITO thickness at the wafer center ranges from 15 nm to 615 nm, with all samples exhibiting a gradual decrease in thickness from the center to the edge.
Figure 3b presents the ITO sheet resistance line scan for all nine samples. For thin ITO films, RS at the center is generally lower than at the edge. However, for thicker ITO films, the sheet resistance does not show a monotonic change from the wafer center to the edge. By applying the equation ρ = RS x dITO to the data from Figures 3a and 3b, we obtained the resistivity map of the ITO films, as shown in Figure 3c.
Figure 3d depicts a schematic cross-section of a circular magnetron sputtering head. This configuration includes permanent magnets positioned behind the target, generating a high-density, torus-shaped plasma, with the substrate parallel to the target. This setup results in a distinct erosion track on the target surface adjacent to the high-density plasma torus.
For thick ITO films with dITO ≥ 89 nm, the lowest resistivity values are approximately 2 x 10-4 Ω·cm, which is close to the bulk resistivity of the ITO film. For thin ITO films with dITO ≤ 50 nm, the resistivity values range from 5 to 12.5 x 10-4 Ω·cm. This data illustrates the spatial distribution of resistivity ρ for all the ITO samples.
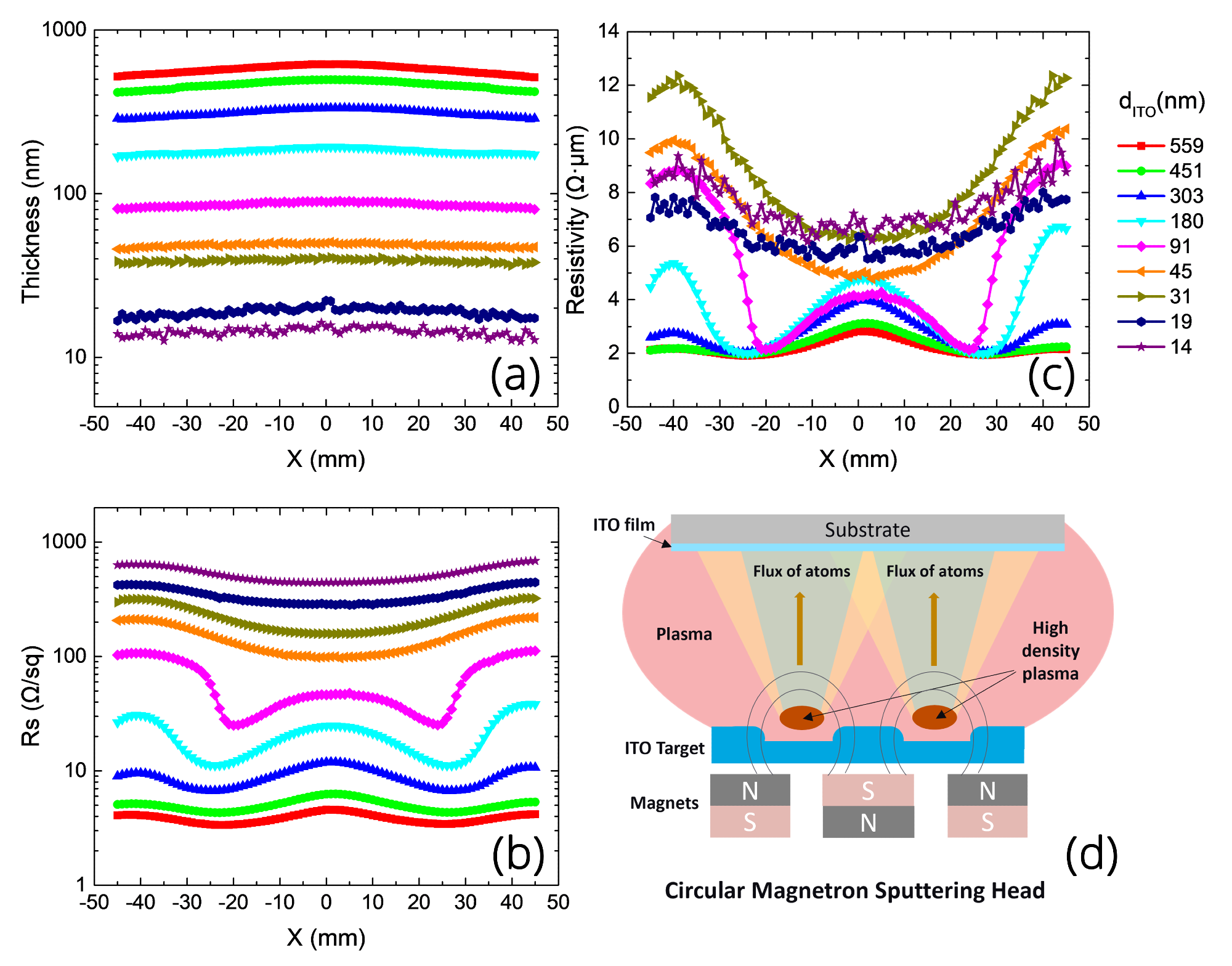
Figure 3. Log thickness (a) and log sheet resistance (b) line profiles of ITO films with center thickness ranging from 15 to 615 nm. Resistivity line profiles (c) of ITO films calculated from the thickness and sheet resistance results. Schematic cross section of a circular magnetron sputtering head (d). Image Credit: KLA Corporation
Studies have shown that when depositing metal oxide films using radio-frequency (RF) sputtering, the high flux of positive ions impacting the target at the erosion track releases low-energy secondary electrons. These electrons can easily attach to oxygen atoms, forming negative oxygen ions, which are then accelerated toward the substrate by the cathode sheath. This indicates that the spatial distribution of resistivity in relation to the erosion track on the target surface is influenced by energetic negative oxygen ions. The findings suggest that the primary factor affecting the deposited films' resistivity and band gap energy profiles is the metal depletion due to re-sputtering by these energetic negative oxygen ions.
The resistivity for these RF-sputtered ITO films shows significant spatial distribution, consistent with other studies on metal oxide films such as aluminum-doped zinc oxide. The results suggest that the growth conditions highly impact the resistivity distribution. Therefore, the uniformity of electronic properties needs to be monitored during the film deposition process.
Summary of Results
The study investigates the electrical properties of sputtered ITO films, focusing on their resistivity. Nine films of varying thicknesses were prepared under identical conditions, and their resistivity was measured. The results revealed a significant spatial distribution of resistivity, which was influenced by the films' growth conditions. This variation is attributed to energetic negative oxygen ions formed during RF sputtering, which cause metal depletion through re-sputtering.
The findings emphasize the importance of monitoring the uniformity of electronic properties during the film deposition process. It was observed that assessing thickness or sheet resistance alone is insufficient for effective ITO film process control. Instead, both factors must be combined to calculate resistivity accurately. This comprehensive approach provides a better understanding of the uniformity of electrical properties, offering valuable insights into improving the deposition process. Consequently, this can enhance the overall performance of ITO devices and reduce failure rates.

This information has been sourced, reviewed and adapted from materials provided by KLA Corporation.
For more information on this source, please visit KLA Corporation. For more information on KLA Instruments metrology products and applications, please visit the KLA Instruments website.