Nanotechnology, like 3D printing, has been the focus of extensive research and development over recent years. Both are in the process of revolutionizing broad and varied sectors and, in some cases, have already done so. The concept of their synergy is a natural progression in their respective developments and is already promising an equally revolutionary and far-reaching impact.
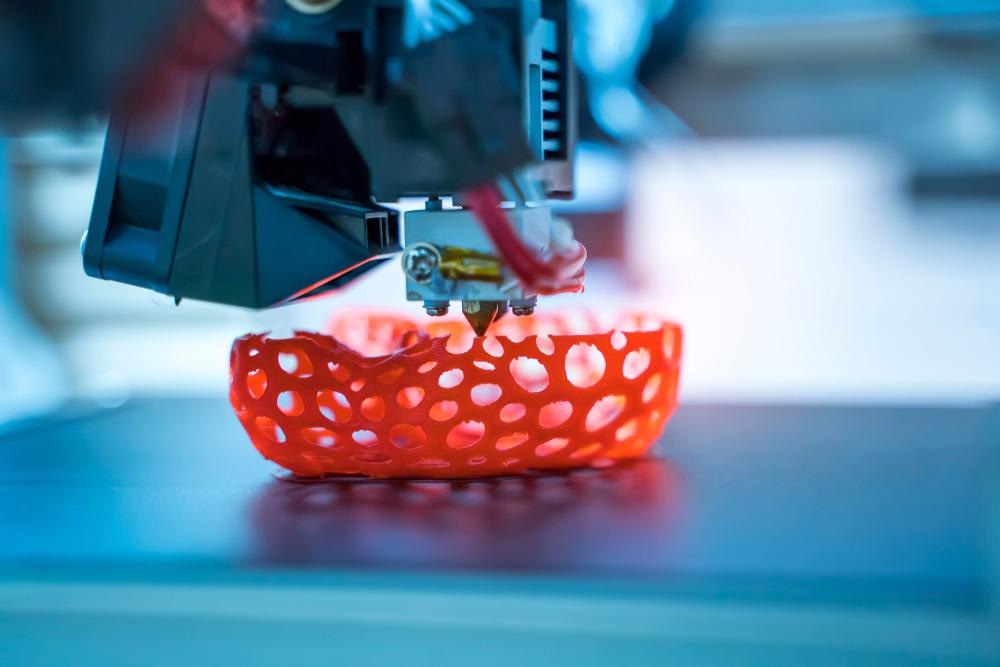
Image Credit: asharkyu/Shutterstock.com
The benefit of combining the two technologies can broadly be thought of as two-fold and stem from slightly differing concepts: applying 3D printing to nanotechnology and applying nanotechnology to 3D printing. The former enhances the complexity and design flexibility of nanoscale structures using 3D printing, and the latter enhances the characteristics of printed products using nanomaterials' advanced and tailorable properties.
3D printing at the nanoscale is commonly achieved via multiphoton lithography (MPL), a process which relies upon the photopolymerization of a light sensitive resin from the non-linear two-photon absorption phenomenon at the focal point of a pulsed laser.
The MPL process is capable of exceptional spatial resolution (commonly ~50nm) and, more recently, adequate printing speed for commercialization. This has been achieved alongside the familiar benefits afforded by 3D printing: high design flexibility and product complexity, minimal material wastage, and on-demand production.
Applications for this process are thus plentiful and reside in biomedical, microrobotics, and photonics sectors to name a few.
Alternatively, by incorporating nanoparticles (NPs) into the traditional 3D printing host material (e.g. polymer or ceramic matrices), a nanocomposite is formed. This can then be used as a feedstock material in printing processes such as fused-deposition modelling (FDM), selective laser sintering (SLS) or stereolithography (SLA).
Nanoparticles in this context are termed nanofillers and include carbon-nanotubes, nanowires, graphene, quantum dots, gold, silver, and titanium oxide. Their incorporation into the host matrix can translate the exceptional properties of nanomaterials to macroscale geometries and rectify one of the most prevalent issues of 3D printing, the limited feedstock materials that are compatible with the process.
Industries and Applications
The potential benefits of 3D printing nanocomposites are likely to be soon realized in all existing uses of 3D printing.
Today, however, such potential has been proven primarily in the biomedical and electronic industries. For example, the acrylic polymer polymethylmethacrylate (PMMA) has been used in the surgical fixation of artificial joints for decades despite its mechanical weakness and poor biocompatibility. However, by incorporating carbon-nanotubes and hydroxyapatite (HAp) NPs into the polymer, these flaws are rectified, and the resulting matrix is drastically improved for biomedical applications.
In the electronics industry, there has been a continuing pursuit for higher performance dielectric capacitors to be used in electric vehicles and wind generators, among other applications. The key to this performance is the energy density of the capacitor.
Luo et al. (2020) displayed that by 3D printing poly(vinylidene fluoride–chlorotrifluoroethylene) (P(VDF–CTFE)) incorporated with barium titanate (BaTio3) nanowires, the high shear environment from the printing process aligned the nanowires in the print direction and gave an energy density 55% higher than that of the equivalent ‘non-aligned’ nanocomposite at the same level loading.
These are just two examples of the multitude of nanocomposites used in 3D printing to achieve previously unfeasible product characteristics. They can generally be categorized on account of the nanoparticles themselves: carbon-based NPs, ceramic-based NPs, metal-based NPs, magnetic-based NPs, semiconductor-based NPs, polymeric NPs, and liquid-based NPs.
Challenges
Challenges to the widespread uptake of this promising technology do remain, the most influential of which lies in the synthesis of the feedstock material. The homogenous dispersion of nanoparticles throughout the host matrix is vital in avoiding local stress concentrations and achieving enhanced material properties.
This proves difficult due to the tendency of nanoparticles to agglomerate, requiring the use of specialized surfactants to lower the interfacial tension, the adoption of a colloidal processing approach, or the careful control of nanoparticle concentration with an effective feedstock mixing method (such as wet or solution mixing).
Further challenges include the anisotropy from the forced alignment of nanoparticles in the printing direction (for extrusion-based methods), nanoparticles altering the rheology and thus printability of the host material, and the high porosity of printed nanocomposites (for SLS methods).
These ‘nanoparticle-specific’ challenges are faced alongside those typical for 3D printing; unsuitability for mass production, frequent post-processing requirements, high energy consumption, restricted build size, and high capital costs.
Future Research
Future research will undoubtedly continue to add increasingly advanced and diverse nanocomposites to the catalog of printable materials. An exciting avenue this could take is in the fabrication of intelligent, stimuli-responsive structures through 4D printing.
Specifically, shape memory polymers (SMP) are emerging as a promising category of materials suitable for the incorporation of nanoparticles.
Alongside the synthesis of novel materials, future research will further optimize the printing process for existing nanocomposites. This includes refining the fabrication techniques for homogenous nanocomposite feedstock material, individually perfecting processing parameters (potentially through developing modeling tools given the increasing range of printable materials), and increasing the printing speed to facilitate mass production.
A final research direction of interest is with the health concerns of nanoparticle emission from the printing process. Youn, Seo, Han, and Jeon (2019) found that the high concentration of nanoparticles in the air from printer operations is a cause for concern for the respiratory tract of operators. With the predicted uptake of the technology, this concern will only be exacerbated and require further investigation and solutions.
Despite the challenges mentioned, the 3D printing of nanocomposites will undoubtedly reach widespread commercialization and be a critical aspect of future manufacturing due to the unique advantages it displays.
Continue reading: Advancing the Synthesis of Freestanding Nanostructures with 3D Printing.
References and Further Reading
Perevoznik, D., Nazir, R., Kiyan, R., Kurselis, K., Koszarna, B., Gryko, D. and Chichkov, B., (2019) High-speed two-photon polymerization 3D printing with a microchip laser at its fundamental wavelength. Optics Express, 27(18), p.25119. Available at: https://doi.org/10.1364/OE.27.025119
Arora, M., Chan, E., Gupta, S. and Diwan, A., (2013) Polymethylmethacrylate bone cements and additives: A review of the literature. World Journal of Orthopedics, 4(2), pp.67-74. Available at: https://doi.org/10.5312/wjo.v4.i2.67
Clarissa, W., Chia, C., Zakaria, S. and Evyan, Y., (2021) Recent advancement in 3-D printing: nanocomposites with added functionality. Progress in Additive Manufacturing. Available at: https://doi.org/10.1007/s40964-021-00232-z
Luo, H., Zhou, X., Guo, R., Yuan, X., Chen, H., Abrahams, I. and Zhang, D., (2020) 3D printing of anisotropic polymer nanocomposites with aligned BaTiO3 nanowires for enhanced energy density. Materials Advances, 1(1), pp.14-19. Available at: https://doi.org/10.1039/D0MA00045K
Eguiluz, A., Ferrández-Montero, A., Yus, J., Sanchez-Herencia, A. and Ferrari, B., (2021) Dispersion of Ni nanoparticles into Ti(C,N) colloidal filaments for 3D printing by FFF. Open Ceramics, 5. Available at: https://doi.org/10.1016/j.oceram.2021.100064
Cholleti, E. and Gibson, I., (2018) ABS Nano Composite Materials in Additive Manufacturing. IOP Conference Series: Materials Science and Engineering, 455, p.012038. Available at: https://doi.org/10.1088/1757-899X/455/1/012038
Cortés, A., Cosola, A., Sangermano, M., Campo, M., González Prolongo, S., Pirri, C., Jiménez‐Suárez, A. and Chiappone, A., (2021) DLP 4D‐Printing of Remotely, Modularly, and Selectively Controllable Shape Memory Polymer Nanocomposites Embedding Carbon Nanotubes. Advanced Functional Materials, p.2106774. Available at: https://doi.org/10.1002/adfm.202106774
Youn, J., Seo, J., Han, S. and Jeon, K., (2019) Characteristics of nanoparticle formation and hazardous air pollutants emitted by 3D printer operations: from emission to inhalation. RSC Advances, 9(34), pp.19606-19612. Available at: https://doi.org/10.1039/C9RA03248G
Disclaimer: The views expressed here are those of the author expressed in their private capacity and do not necessarily represent the views of AZoM.com Limited T/A AZoNetwork the owner and operator of this website. This disclaimer forms part of the Terms and conditions of use of this website.