Atomic force microscopy (AFM) is one of the most versatile and powerful microscopic technologies used to study materials at nanoscale dimensions.
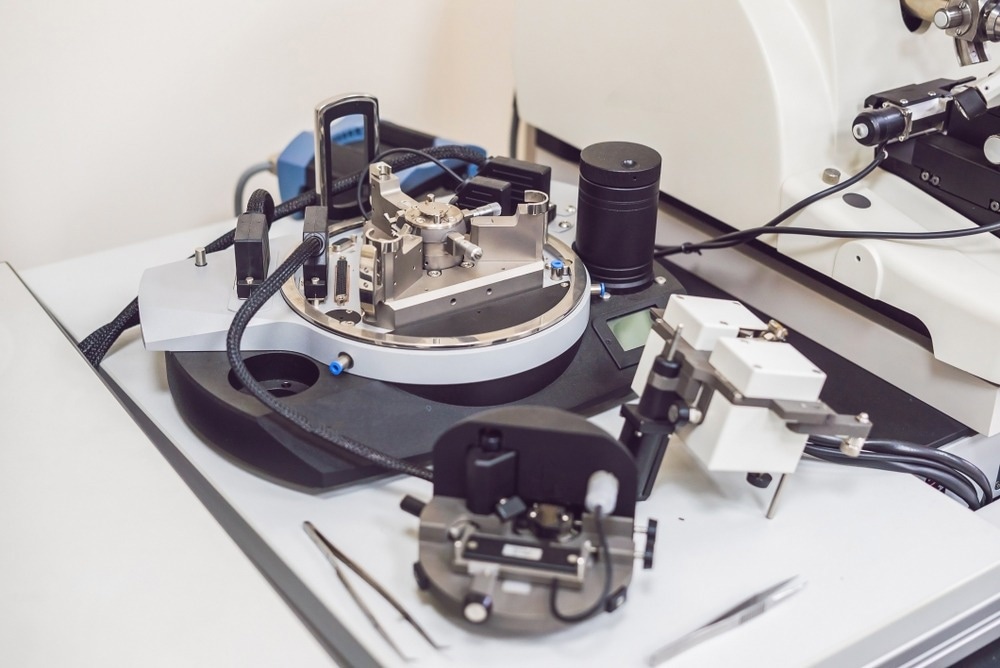
Image Credit: Elizaveta Galitckaia/Shutterstock.com
Two of the primary advantages of AFM are the ability to secure three-dimensional (3D) images and measure various types of surfaces. It generates images at atomic scale resolution with minimal sample preparation. This article discusses the various aspects of AFM, particularly factors that affect the accuracy of AFM images.
AFM and Nanotechnology
AFM is commonly used to characterize nanoparticles, which include valuable data related to their qualitative and quantitative properties. For instance, it provides information about the physical properties (e.g., morphology, surface texture, roughness, etc.) as well as the size, volume distribution, and surface area of the nanomaterials.
Scientists stated that several nanomaterials of varying size, i.e., ranging from 1 nm to 8 μm, can be characterized in the same scan. Importantly, AFM can characterize nanomaterials in multiple mediums, such as controlled environment, ambient air as well as liquid dispersions. This technology is used to study nanocomposites based on their spatial distribution with otherwise uninformative topographies.
The software-based image processing of AFM data provides quantitative data on individual nanoparticles. Researchers highlighted some of the advantages of using AFM for characterizing nanoparticles over other microscopies (e.g., scanning electron microscope-SEM and transmission electron microscope-TEM). They stated that AFM provides higher resolution with 3D images, which helps measure the height of nanoparticles.
In contrast, SEM/TEM images provide two-dimensional images and, therefore, have limited quantitative estimation abilities. Additionally, compared to SEM/TEM processes, AFM is easy to operate, cost-effective, and requires relatively less laboratory space for nanoscale imaging.
Factors that Affect AFM Imaging
Typically, AFM is equipped with a cantilever consisting of a sharp probe that scans a specimen surface. The cantilever is made up of silicon or silicon nitride, whose tip radius curvature is measured at a nanoscale. At one end of the cantilever, a beam is attached with a piezoelectric displacement actuator, which is controlled by the AFM. The other end contains the probe tip that interacts with the specimen.
When the probe is close to a surface, it experiences an attractive or repulsive force due to surface interactions. As a result of the force, the cantilever deflects, which is measured using a laser beam through a position-sensitive photodiode (PSPD).
AFM images the topography of the specimen by scanning the cantilever over the sample. A feedback loop is used to control the height of the probe above the sample surface, and, thereby, the laser position is constantly maintained, which helps generate an accurate AFM image. In a nutshell, when the probe tip interacts with the sample, the sample deforms until there is an increase in the contact area. Accurate estimation of this deformation determines the resolution and reliability of AFM images.
AFM operates at various modes based on the nature of the probe-surface interaction. Some of the modes include intermittent contact mode, contact mode, and non-contact mode. As the name suggests, in contact mode, the probe tip literally contacts the surface. In this mode, the interaction between the tip and the surface is repulsive. The non-contact mode is the opposite extreme. However, in the intermittent contact mode, the cantilever oscillates perpendicularly near the specimen surface.
The selection of the imaging mode is the key determining factor for image resolution. Researchers stated that using aqueous buffer solutions is ideal for imaging samples because it helps preserve biological samples in their native state.
The vibration environment of the AFM instrument affects the resolution in vertical imaging, where the cantilever is vertically placed concerning the specimen. However, the resolution of the AFM image, associated with the horizontal cantilever position to the specimen, is affected by the diameter of the tip utilized for scanning. Generally, the AFM instrument has a vertical resolution of below 0.1 nm and X-Y resolutions of approximately 1 nm.
Generation of Accurate AFM Images
To obtain accurate AFM images, the axial displacements of the piezoelectric stage must be suitably calibrated using various standards. For instance, the height of a sample can be measured accurately by calibrating AFM using step height reference standards. The reference calibration standards contain three calibration gratings, certified by the National Institute of Standards and Technology (NIST).
Intermittent contact mode is suitable for nanoparticle characterization, which is fixed to a substrate via a weak physical force. For accurate imaging, the amplitude of the oscillation must be kept greater than 10 nm, and ideally between 100 nm to 200 nm.
Several studies have shown that the properties and dimensions of the cantilever and the probe tip play an important role in obtaining sensitive and high-resolution AFM images. Therefore, several features must be considered while selecting an AFM cantilever for imaging. Some of the key features include tip radius and geometry of the probe, as it affects the overall representation of surface features. Typically, researchers use tips with radii less than 10 nm for nanoparticle imaging.
It is important to have stable cantilevers for successful imaging in intermittent contact mode. The stability of the cantilever can be maintained by providing suitable energy that can overcome the adhesive forces between the tip and the sample. Scientists stated that cantilever stiffness of around 40 Nm-1 can be used to overcome the issues with adhesive forces.
AFM Image Processing
After the AFM image is generated in real-time, it can be viewed, modified, and analyzed using the software provided by the AFM manufacturer. Typically, AFM images are line-wise flattened to remove residual effects of the image developing process, such as thermal drift and non-linear scanning.
Most AFM software packages provide automated particle analysis functions containing cross-sectional line profiling, which helps measure particles' height based on pixel data. It is important to analyze a group of particles as well as an isolated particle for characterization.
References and Future Reading
Heath, G.R., et al. (2021) Localization atomic force microscopy. Nature, 594, pp. 385–390. https://doi.org/10.1038/s41586-021-03551-x
Zahl, P & Zhang, Y (2019) Guide for Atomic Force Microscopy Image Analysis To Discriminate Heteroatoms in Aromatic Molecules. Energy and Fuels, 33(6), pp. 4775–4780. https://doi.org/10.1021/acs.energyfuels.9b00165
Martin-Jimenez, D., et al. (2019) Bond-Level Imaging of the 3D Conformation of Adsorbed Organic Molecules Using Atomic Force Microscopy with Simultaneous Tunneling Feedback. Physics Review Letters, 122. DOI: https://doi.org/10.1103/PhysRevLett.122.196101
Extance, A (2018) How atomic imaging is being pushed to its limit. Nature, 555, pp. 545-547. doi: https://doi.org/10.1038/d41586-018-03305-2
Klapetek, P., et al. (2011) Atomic force microscopy analysis of nanoparticles in non-ideal conditions. Nanoscale Research Letters, 6(1), pp. 514. https://doi.org/10.1186/1556-276X-6-514.
Grobelny, J., et al. (2011) Size Measurement of Nanoparticles Using Atomic Force Microscopy. Methods in Molecular Biology. DOI: https://doi.org/10.1007/978-1-60327-198-1_7.
Disclaimer: The views expressed here are those of the author expressed in their private capacity and do not necessarily represent the views of AZoM.com Limited T/A AZoNetwork the owner and operator of this website. This disclaimer forms part of the Terms and conditions of use of this website.