Silk is a protein fiber produced naturally by insect larvae for the purpose of manufacturing a cocoon, with some of the best-known silk obtained from the mulberry silkworm. Recently, scientists have developed a new approach to nanofiber production inspired by the head bobbing of silkworms.
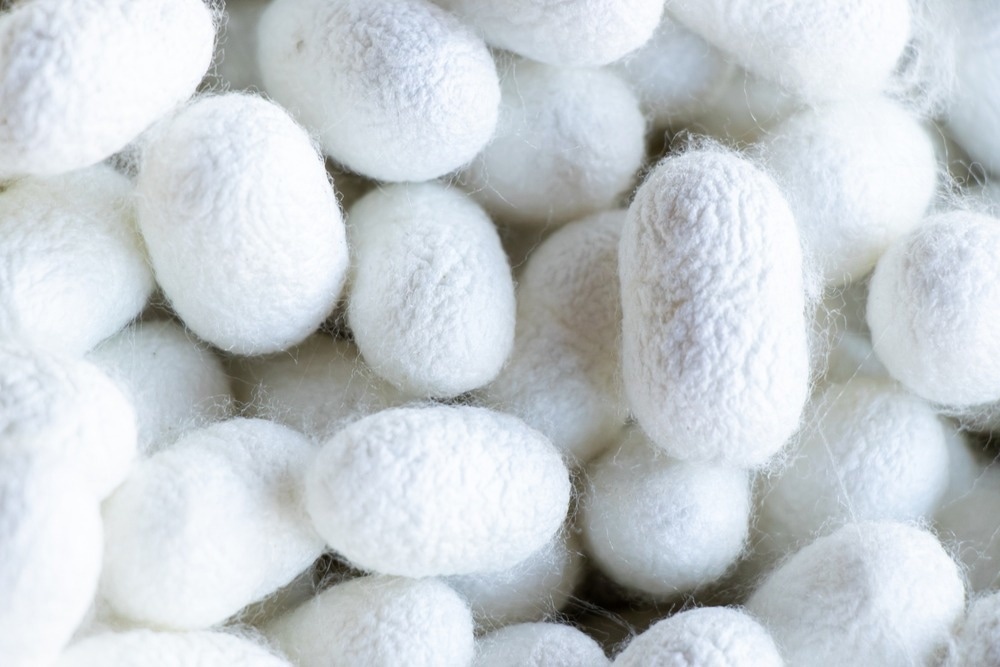
Image Credit: Bankrx/Shutterstock.com
The new approach does not require as much equipment as conventional methods and could have applications in wound dressings.
Traditionally, silk is harvested by collecting and unraveling silk cocoons to obtain fibers, though the process is arduous and has relatively low throughput. In nature silkworm larvae secrete fibroin and sericin proteins from specially adapted salivary glands that mix to produce silk and begin by sticking the silk to a surface and then pulling their head away in a particular motion to draw the silk out.
Silk fibers have also been produced in the laboratory from liquid silk protein by spinning methods such as blow spinning, electrospinning, wet spinning, and melt spinning. These require relatively significant forces to drive the fluids through nozzles or spinnerets, often leading to inconsistent fiber thickness.
In this new research, the silk extrusion mechanism of silkworm larvae was more closely mimicked in the lab using a method termed micro-adhesion guided (MAG) spinning. Consistent micro and nanofibers were produced using this method, opening us the future biomedical applications of nanofibers.
What are Nanofibers?
Nanofibers are fibers that are only several nanometers thick. While their use has been observed across several industries, such as in flexible electronics, their applications in the biomedical sector have received the most interest. For example, several wound dressings have been developed over the past few years utilizing these nanoscale materials.
However, despite these developments, nanofiber spinning methodologies remain slow. These methods also still carry the risk of producing clumpy fibers, significantly reducing the practical use of the produced nanofibers.
How are Silk Fibers Manufactured?
Most silk fiber spinning techniques utilize externally provided forces, such as flowing air, pressure, or electrostatic, to feed liquid silk protein through one or many fine needles to generate pre-fibers, which are solidified either by cooling or the addition or removal of solvents.
However, this is not how silkworms draw silk in nature, instead using a contact spinning approach of adhering the silk to a surface and pulling away, allowing high surface area and air contact to quickly coagulate the silk proteins.
Similar contact spinning approaches involving pressing a flat plate onto a plate coated in liquid silk protein have proven successful in producing silk fibers in the lab, though they suffer from poor reproducibility.
MAG spinning innovatively utilizes an array of needles that press into a plate coated in a compatible array of wells containing a capillary-controlled quantity of protein. In this manner, the thickness of silk fibers generated can be fine-tuned by tailoring the needle and well size, as well as other parameters such as draw speed and needle contact degree.
Interestingly, the group also replicated the specific head motions of silkworm larvae to produce weaved or thick strands of silk. A straight up and down motion produced silk fibers approximately 10 μm in diameter, while applying a vibratory back and forth motion to the needle array allowed the silk fibers to interlink and cross over, providing a webbed silk fiber with similar average fiber thickness and a rotational motion produced one wrapped strand almost 50 μm in diameter.
Once the silk fibers are produced between the contact plates, they are collected by a third plate moving in from a perpendicular position to the fibers, to which they adhere and can be collected for examination and use. The group also imaged the silk fabrics generated by multiple collection passes at different angles, which produced weaved material with differing porosity for various applications. In another example of MAG spinning, the group exchanged the previously described needle array of the contact plate with polymer foam of varied porosity, soaked in liquid silk protein. It was found that fibers generated by this method were less homogeneous in diameter, with mixes of thick and thin fibers in a ratio dependent on foam pore size, producing an interwoven fabric.
What are the Clinical Applications of Silk Nanofibers?
Interestingly, Ni et al. discuss this technique of silk fabric generation as a simple and convenient method of producing and applying sterile, biocompatible, and easily washed-away nanofiber-based wound dressings.
Nanomaterials have been widely explored for wound dressing applications, observing use as scaffolds and injectable fillers in surgery. This is often due to their biocompatible nature and further association with regenerative properties such as enhanced cell migration and proliferation, angiogenesis, and re-epithelialization.
In terms of silk-based nanomaterials, both the fibroin and sericin components of silk have been found to present antibacterial properties, and also engage in antioxidant activity. The structure of sericin is also similar to that of serum albumin, which is one of the major protein constituents of blood and, thereby, is heavily consumed during the wound healing process.
Within the silk nanofiber the fibroin chains form the core and provide structure, while sericin weaves around it to provide a flexible coating. Specially tailored wound dressings that apply a pure sericin layer directly to the skin followed by a protective fibroin layer have been developed and show some improvement over mixed fabrics, with even greater biocompatibility, indicated by lower local inflammatory cytokine response when applied to the skin.
Ultimately, spray-on wound dressings containing fibroin and sericin could be available to allow the quick and convenient application of protective and flexible silk barriers, potentially supplemented with additional wound-healing additives.
References and Further Reading
Ni, Z., Zhu, Z., Ji, Y., He, X., Fu, X., Yang, W., & Wang, Y. (2022). Biomimetic Microadhesion Guided Instant Spinning. Nano Letters, 22(23), pp. 9396–9404. https://doi.org/10.1021/acs.nanolett.2c03297
Chouhan, D. & Mandal, B. B. (2020). Silk biomaterials in wound healing and skin regeneration therapeutics: From bench to bedside. Acta Biomaterialia, 103, 24-51.
Disclaimer: The views expressed here are those of the author expressed in their private capacity and do not necessarily represent the views of AZoM.com Limited T/A AZoNetwork the owner and operator of this website. This disclaimer forms part of the Terms and conditions of use of this website.