As part of an Editorial collaboration with the Graphene Flagship, AZoNano is highlighting members of the Graphene community that are working on exciting developments involving graphene. In this interview, we speak with Sixonia Tech about the company's highlight product, E-Graphene, as well as their thoughts on the future of Europe's graphene industry.
Please could you introduce yourself and your role at Sixonia Tech?
My name is Martin Lohe, and I am the CEO and co-founder of Sixonia Tech.
How did you become involved with the company?
I had my first contact with graphene during a post-doctoral position in 2015 when the hype around it was still at its peak. I was leading an industry project targeting graphene's industrial production and I was starting to build a research group at the Technical University of Dresden, Germany. During our experiments, we made some groundbreaking discoveries that ultimately led to the foundation of Sixonia Tech as a spin-off from the university in 2017.
Who is Sixonia Tech, and what are its core aims?
We are a young nanotech company with a game-changing solution removing the traditional roadblock to scalable graphene commercialization: the discrepancy between quality, processability and cost.
We are enabling the use of graphene as a “wonder material” to its fullest potential in various fields of application ranging from energy storage, smart textiles to air filtration, to name a few.
Our core aim is to enable new technologies and to make existing ones more efficient and sustainable.
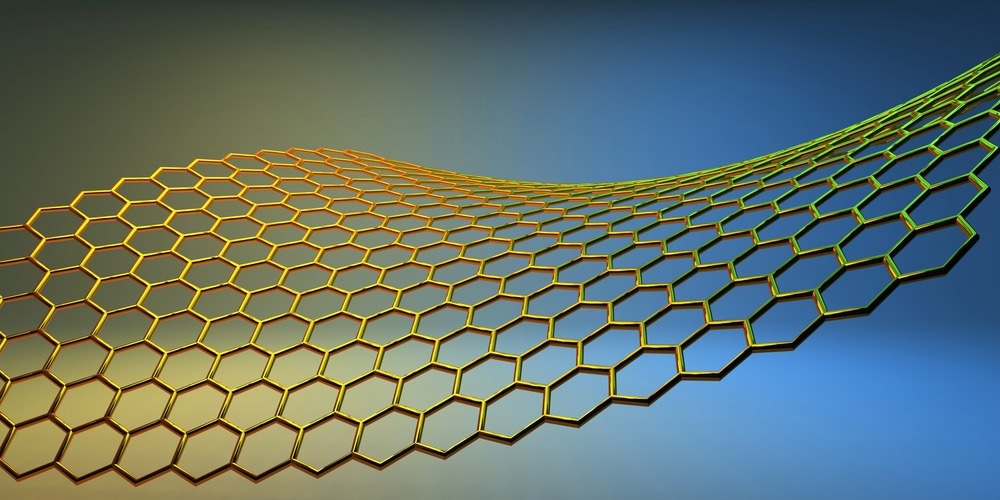
© Shilova Ekaterina/Shutterstock.com
Could you explain how electrochemical exfoliation works and its role in graphene production?
Electrochemical exfoliation is a technology that separates the layers of graphene within a graphite raw material in a very energy efficient, sustainable and “gentle” way. In principle, it works similarly to the process that happens in a battery during charging: we are intercalating ions between the individual layers, pushing them apart to allow us to separate them from each other.
As a concept, electrochemical exfoliation has been known in the scientific community for many years, but so far, only very few companies have attempted to scale this process to a commercially relevant scale. Furthermore, most bulk graphene producers today still rely on the more traditional concepts of purely mechanical or chemical processes.
What are E-Graphenes and why was it important for the company to develop them?
As I have indicated earlier, when I started working with graphene, I soon realized there was a discrepancy between quality and processability with the traditional production methods – and it felt like that was standing very much in the way of widespread commercial adoption.
As a scientist, I was honestly not concerned too much about the costs back then. Still, it turned out that our process is very competitive in that regard, which is why we made the decision to commercialize the technology. To distinguish our products from the graphenes obtained by other methods, we called them electrochemical graphenes, or in short E-Graphenes.
What is characteristic of Sixonia Tech’s graphene materials compared to other commercially available options?
Our process allows us to attach functional groups to the individual graphene platelets during the exfoliation step – using the same electrochemical process that we use to exfoliate the graphite – but without destroying the inherent properties of the material.
We can produce graphenes that are easily processable and tailored to individual customer needs without the need for additives while maintaining their conductivity.
One of the barriers to the wide-scale use of graphene is the efficient, cost-effective mass production of high-quality graphene materials. What trends in the graphene industry have you observed that are hoping to address this problem?
Most bulk graphene producers that have entered the market early on are relying on two technologies: graphene oxide-based materials or mechanically exfoliated materials. Both processes are mass scalable at a reasonable cost.
But the devil is in the detail here: First, no two graphenes from different suppliers are really the same and secondly, as indicated above, these graphenes are per se unable to combine high-quality AND ease-of-use.
This does not mean that these products are bad; it just means that the majority of producers cannot rely on their customers to successfully integrate the materials into a final or semi-finished product, as the processing requires a lot of experience and expertise with the particular graphene material.
Therefore, what we have seen in recent years is that graphene producers are also engaging in product development themselves and delivering at least “pre-processed” formulations (such as masterbatches) that are then easier for the customers to integrate.
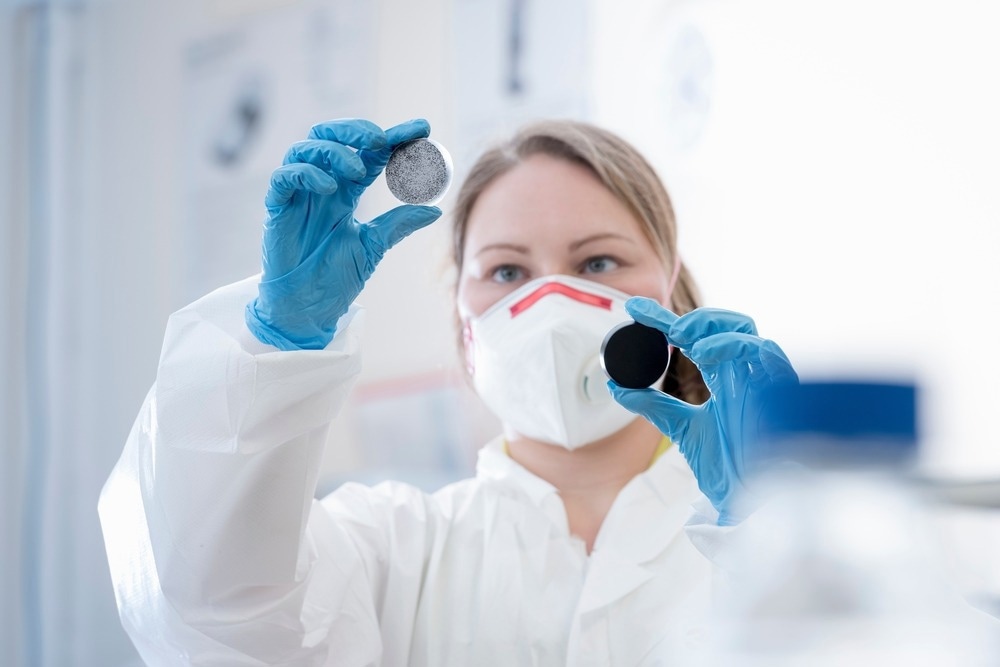
© Image Source Trading Ltd/Shutterstock.com
How did you become involved with the Graphene Flagship?
I became involved with the Graphene Flagship early in my career when I was still at the university. I was the admin for the Work Package 13 of the Flagship project, that was dealing with “Functional foams and coatings”.
In 2020 we were able to join the project with Sixonia as a full partner through an open call where we successfully applied with our Spearhead Project “AeroGraFT”, where we are developing novel air filters for aircraft cabin air systems together with Lufthansa Technik and several other partners. We are also involved in WP13 now, developing materials for anti-corrosion applications.
What are some of the benefits of your relationship with the Graphene Flagship, and why was it important to establish strong ties with such an organization?
I think being part of such a huge and diversified project provided a high level of visibility. It also enabled us to gain valuable insights into various value chains and expand our network with experts and partners we are now collaborating with beyond our scope within the project. Obviously, the funding also helped us develop our production technology further from a small lab setup to a working pilot plant so that we are now ready to scale our process at will.
The Graphene Flagship is catalyzing graphene R&D within Europe, cementing its place as a global graphene powerhouse. What more could be done to boost the European graphene industry?
The Graphene Flagship has now supported the innovation and research in 2D materials for over a decade. It is very important that the transfer from lab-state research towards commercialization is combined and supported in a joint effort between academia and industry and should gain continued support by the European Union, considering the growth potential and possible impact of these materials.
Best practices and success stories must be made visible and projects need sufficient funding in different development stages to successfully become industrial applications with a high impact.
Given our current stage of growth, we would appreciate the Graphene Flagship or its successor(s) to help boost young tech companies also in their growth-phase of finding and connecting with the right industrial and financial partners.
Are there any challenges that must be overcome to achieve this?
Taking Sixonia Tech as an example, we are facing the challenge of growing our team, production and customer base at the same time with securing sufficient funding.
Setting the right financial support in a blended finance product, combining private funds and public grants or financial structures tailormade for nanotech companies like ours would certainly boost the growth of companies coming out of projects like the Graphene Flagship.
What is there to look forward to from Sixonia Tech?
Sixonia has just celebrated its 6th birthday. After the first years of technological groundwork and more R&D-focused projects, we have entered the next phase, focussing on exploring market opportunities with international industry partners in various application streams.
Our material has been successfully tested with very positive feedback from several partners that motivates us for the next growth steps. I am thankful for the support of our very active board, which is supporting all our growth activities with their expertise and network and we are in good faith of being able to announce some new projects and collaborations soon.
Where can our readers go to stay up to date with the company’s activities?
People interested in the activities of Sixonia Tech can follow us on LinkedIn and our website, where we are establishing a continuous communication flow – news on the company, technology and market. There will be blog articles and referrals to projects we are working on. Stay tuned.
About Dr. Martin R, Lohe
Dr. Martin R. Lohe is co-founder and CEO of Sixonia Tech, a growing start-up that commercializes tailorable, functionalized, processable few-layer E-Graphenes and customized formulations. He has more than a decade of experience in the field of process development, optimization, upscaling and commercialization of inorganic specialty materials.
During his Ph.D. and Post-Doc in inorganic chemistry at the Technische Universität Dresden, he set up a university-based profit center for the production, upscaling and application of specialized, high performance adsorbent materials. During a Post-Doc in Mainz, at the Max-Planck-Institute for Polymer Research and while joining the Chair of Molecular Functional Materials as Industry Project Coordinator in 2015 he switched his research focus towards graphene and 2D materials.
Within the chair, part of the excellence cluster cfaed at TU Dresden, he built up the “Innovation and Industry Group”, led the ESF Junior Research Group “Graphenzentrum Dresden” and co-founded the spinout company Sixonia Tech in 2017.
Disclaimer: The views expressed here are those of the interviewee and do not necessarily represent the views of AZoM.com Limited (T/A) AZoNetwork, the owner and operator of this website. This disclaimer forms part of the Terms and Conditions of use of this website.