German and US researchers have produced a super-sharp, strong, and resilient carbon tip that has earned top place as the industry's current benchmark. Funded by the EU, the diamond-like tip is 3,000 times more wear-resistant at the nanoscale than a silicon oxide tip, making it ideal for use in atomic imaging, probe-based data storage, and other emerging applications. Findings from the study are published in the journal Nature Nanotechnology.
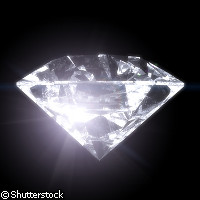
The research was part of PROTEM ('Probe-based terabit memory'), a project that received EUR 5.3 million under the 'Information society technologies' (IST) Thematic area of the Sixth Framework Programme (FP6). Collaborators on the current study include IBM Research-Zurich in Switzerland, and the US-based University of Pennsylvania and University of Wisconsin.
In their paper, the authors write that greater 'understanding of friction and wear at the nanoscale [the length scale applicable to nanotechnology] is important for many applications that involve nanoscale components sliding on a surface'. These emerging applications include nanolithography, nanometrology and nanomanufacturing.
Diamond-like carbon, they explain, is often used as a surface coating in certain types of applications that require low friction and wear because of its resistance to wear at the macroscale. Until now, the issue has always been the material's resilience to wear at the nanoscale because manufacturing diamond-like carbon structures with nanoscale precision is complex.
Another key difference between the macroscale and the nanoscale is that defects, cracks and other conditions that control material strength and wear at macroscopic scales are not as important at the nanoscale.
The new nano-sized tip produced by the researchers wears away at a significantly lower rate than that of a silicon oxide tip (the current state of the art). At a rate of one atom per micrometer of sliding on a substrate of silicon dioxide, the material has now set a new standard.
'[The diamond-like carbon material] is known to possess low friction in humid conditions, and we find that, at the nanoscale, it is three orders of magnitude more wear-resistant than silicon under ambient conditions,' they conclude.
The tip comprises carbon, hydrogen, silicon and oxygen, all combined together on the end of a silicon microcantilever (used in atomic force microscopy). Instead of simply coating the tip with wear-resistant materials, the scientists developed the material from scratch. They used a molding technique to produce the tips on the silicon microcantilevers, and a bulk processing technique that would allow for mass commercial manufacturing in the future.