Oct 1 2015
The University of Twente is receiving an EU grant for a Marie Sklodowska-Curie project titled 'Laser4Fun' involving the machining of surfaces with lasers. Laser machining is making a huge advance and there is enormous interest from industry. The UT researchers are becoming increasingly successful in adding a particular function to an existing surface with lasers. This results, for example, in bacteria-free medical equipment in hospitals, or water and oil repellent products in the packaging industry.
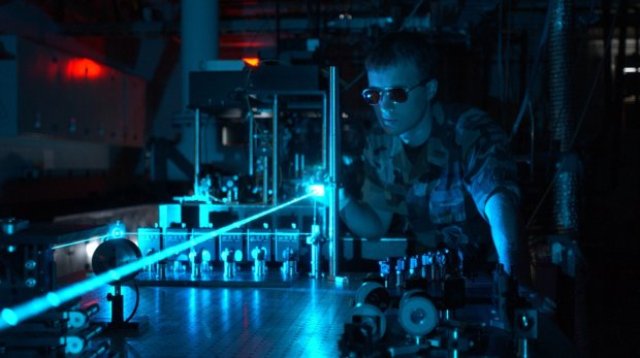
Gert-Willem Römer, laser researcher at the University of Twente, particularly works with lasers with an extremely short pulse duration. This involves picoseconds or even femtoseconds. "That is so short as to be almost incomprehensible", says Römer. "We know that light travels about 300,000 kilometres in 1 second. In one picosecond, however, light only travels about 0.3 millimetres. The major advantage of such an extremely short laser pulse is that there is almost no thermal response from the material that is being processed. The material therefore does not melt, but is, as it were, removed 'cold', since chemical bonds are broken. As a result, it is as though atoms 'break' from the material, rather than melting, vaporizing and blowing away."
Using the latest laser techniques, many surfaces of existing products can be accurately treated. The technique can replace the special coatings that are currently applied to existing materials for surface improvement.
No more ketchup residues
"Keeping surfaces free from bacteria is an important application", says Römer. "For example, you do not want bacteria to flourish on medical instruments in operating theatres. The food industry can also benefit from, for example, bacteria-free food processing equipment. With the laser-machined surfaces it is possible to prevent cells from adhering strongly to the surface, or to ensure that they do adhere. Water or oil-repellent products are another important application. An example includes a ketchup bottle from which you want to extract the very last drop and do not want any remains to stick to the inside of the bottle. A cleaner, completely empty bottle is also much more environmentally friendly when recycling.
Advantages over lithography
Micro machining with short pulse lasers has major advantages over photolithography, a technique which is used for making chips. “Photolithographic techniques are optimized mainly for processing silicon, the base material from which chips are made," explains Römer. "With a short pulsed laser, however, almost any material can be treated. Metals, polymers, glass, semiconductors, you can process virtually anything with lasers. In addition, in contrast with lithography, the machining with the laser can be performed in normal environmental conditions. Laser processing is thus more easily accessible and much cheaper in comparison. Micro machining with lasers is especially interesting for operations on a scale of between 100 nanometres and 100 micrometres.”
Scaling up
The biggest challenge in the project is to realize a higher laser processing speed. In order to apply the latest techniques further on an industrial scale, scaling-up is required. Römer: "We are working on a laser technique called Direct Laser Interference Patterning (DLIP) where multiple laser beams are combined to create an interference pattern of multiple 'laser spots'. This enables us to perform the operation much faster than with one single laser spot. We are also working in the project on hybrid technologies in which we combine the laser treatment with other techniques. You can, for example, first treat the material with a laser and then, with an etchant, remove the material that has been modified with the laser."
More information
Laser4Fun (fun = functional) is receiving a European Marie Curie “European Training Network” grant of 3.5 million euros. From the grant as many as 14 Early Stage Researchers will be recruited for research positions in the frame of a PhD doctoral programme, targeting a PhD degree. This European Training Network involves joint research training of the PhD-candidates at 10 partners from in and outside academia. The aim is for the researcher to experience different sectors and develop their transferable skills by working on joint this research project. Academic partners, besides the University of Twente, participating in the project are Fraunhofer-IWS, Technical University of Madrid, CNR in Italy, University of Birmingham, Leibniz-Institut für Polymerforschung. Industrial partners in the project are BSH group, Alphanov, Robert Bosch and Airbus. The project will run for four years and started on 1 September 2015. Project website: www.laser4fun.eu
The research at the UT is coordinated by Gert-Willem Römer, senior lecturer of the Applied Laser Technology chair in the Faculty of Engineering Technology Department of Mechanical Engineering Automation. Römer teaches the Laser material processing subject within the Mechanical Engineering master's degree and other technical UT degree programmes. Laser micromachining is one of the topics covered. Besides the usual lectures, students attend practicals with, for example, assignments being performed with short-pulsed lasers.