Nov 7 2019
XG Sciences, Inc. a market leader in the design and manufacture of graphene nanoplatelets and advanced materials containing graphene nanoplatelets, and Terrafilum®, an eco-friendly, high quality filament producer for the 3D printing industry, today announced a joint venture agreement to develop, produce and market 3D printing filaments and coatings using graphene-based materials.
First isolated and characterized in 2004, graphene is a single layer of carbon atoms configured in an atomic-scale honeycomb lattice. Among many noted properties, monolayer graphene is harder than diamonds, lighter than steel but significantly stronger, and conducts electricity better than copper. Graphene nanoplatelets are particles consisting of multiple layers of graphene.
Graphene nanoplatelets have unique capabilities for energy storage, thermal conductivity, electrical conductivity, barrier properties, lubricity and the ability to impart physical property improvements when incorporated into plastics, metals or other matrices.
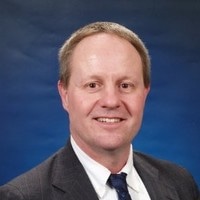
Chris Jackson, President of Terrafilum, points out, “The full potential for 3D printing is starting to be unlocked. The addition of XG’s graphene formulations into our eco-friendly filaments will transform products allowing a greater variety of parts to be created at faster production rates using less energy.”
3D printing has been great for prototyping and limited run production parts, but companies have been challenged to move into high volume production due to material limitations such as direction specific structural weaknesses, a lack of conductivity, a sparse selection of ESD robust filaments, an overall lack of part performance and slow production times.
Graphene-enhanced filaments help solve product related problems, historically associated with FDM (Fused Deposition Modeling) printing, by enhancing z-direction strength, providing more ESD robust parts and creating overall lighter parts in less time.
“Marrying together well-established 3D printing technologies with our graphene-enhanced formulations makes the material difference in resolving the two most limiting factors in 3D printed parts, product strength and processing speeds,” said Dr. Leroy Magwood, Chief Technologist for XG Sciences.