A paper recently published in the Journal of Materials Research and Technology demonstrated the effectiveness of nano-graphene mixed electrical discharge machining (EDM) for efficient machining of a nickel-titanium (nitinol) shape memory alloy (SMA). The paper also displayed the viability of using the heat transfer search (HTS) technique for multi-response optimization in the powder-mixed EDM (PMEDM) of SMAs.
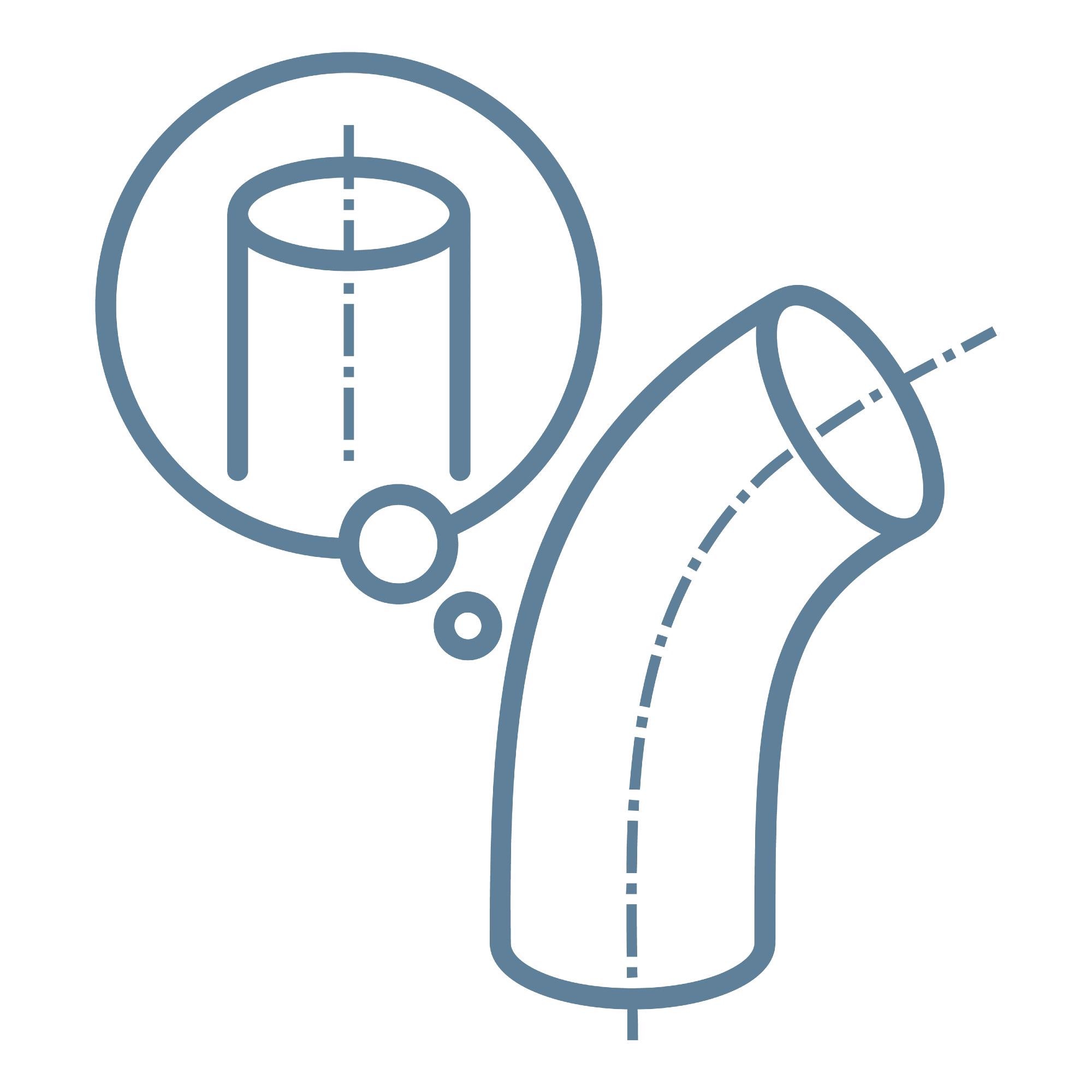
Study; Machining parameter optimization and experimental investigations of nano-graphene mixed electrical discharge machining of Nitinol Shape memory alloy. Image Credit: Dmitry Kovalchuk/Shutterstock.com
Importance of SMAs
SMAs are often used in various applications such as actuators, biomedical devices, and automotive components owing to their excellent characteristics. Among different SMAs, nitinol SMAs have gained considerable attention owing to their exceptional properties such as shape memory effect (SME), superelasticity, and pseudoelasticity. Additionally, nitinol SMAs are resistant to wear and corrosion and possess energy storage capabilities and excellent biocompatibility.
Cut specimens as per L9 design. Image Credit: Vora, J et al., Journal of Materials Research and Technology
Limitations of Traditional Machining Methods
In several industrial applications, precise machining of advanced alloys such as nitinol SMA is a crucial requirement. Machining of nitinol using traditional machining methods leads to poor surface quality and chip breaking, burr formation, excessive tool wear, and lower cutting efficiency owing to the pseudoelasticity, high chemical reactivity, high toughness, and ductility of the alloy. Thus, traditional machining can diminish the alloy properties.
EDM as a Potential Solution
Non-conventional machining processes, such as EDM, are more suitable for the precise machining of SMAs. Machining of advanced alloys using EDM can produce good dimensional accuracy and surface finish.
The EDM process involves a non-contact operation between the work material/alloy and the electrode, where the work material is eroded during the machining process through a recurring spark. The work material and tool are immersed in a dielectric fluid during the erosion process.
The EDM process can be applied to any conductive material irrespective of physical and metallurgical properties due to the non-contact nature of the operation and is suitable for the fabrication of complex profile geometries. Thus, the process is a better alternative for machining difficult-to-cut materials.
However, high-frequency sparks that occur during EDM generate high temperatures, which produce several defects on the machined surface such as increasing dimensional deviation (DD), pore and crack formation, debris formation, and higher surface roughness (SR), leading to lower machining efficiency. Minimizing the surface defects, DD, and SR is crucial for increasing the efficiency of the EDM process.
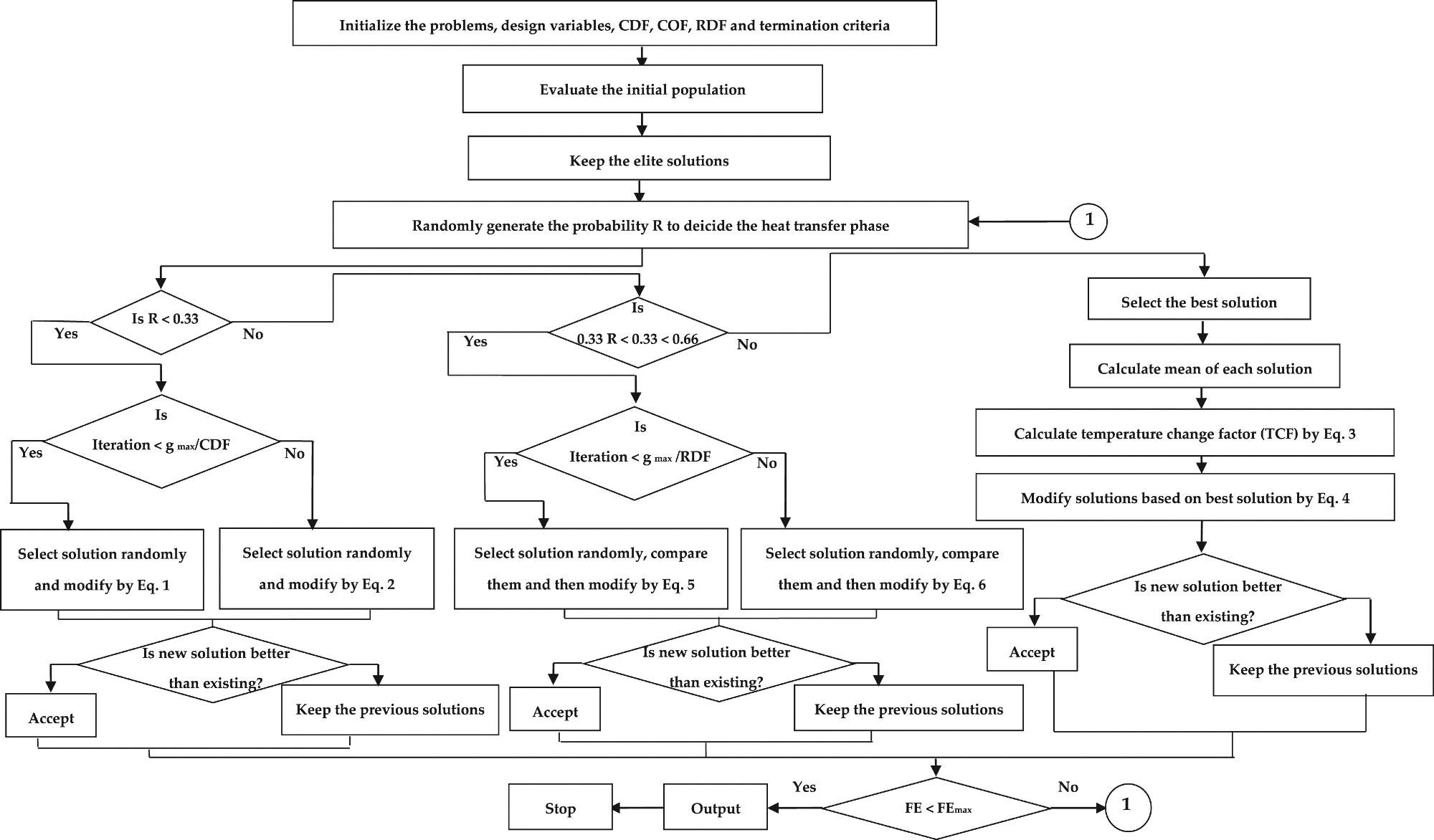
Operating process for HTS technique. Image Credit: Vora, J et al., Journal of Materials Research and Technology
Significance of Nano-Powders to Improve EDM Efficiency
The addition of a proper amount of nanopowders in the dielectric fluid during the EDM process can enhance the machining efficiency. Specifically, the inclusion of nanoparticles can effectively reduce the SR, DD, micro-pores, and micro-cracks of the machined surface in the PMEDM method. The density, size, and conductivity of the nano-powders critically influence their effectiveness.
Graphene nanomaterials, specifically nano-graphene, are more suitable as nano-powders for the EDM process owing to the large surface area and unique bonded network of graphene. Several studies have demonstrated the effectiveness of nano-graphene in the PMEDM process for reducing radial and axial DD and lowering the SR. Thus, the use of nano-graphene in the EDM process can potentially improve EDM performance.
Multi-Response Optimization Using HTS
The EDM process comprises several machining responses and variables. Thus, a proper combination of process parameters at definite/specified levels is required to achieve different contradictory responses.
New algorithms have been developed where algorithm-specific variable regulation is non-essential. The easy-to-implement and faster HTS algorithm represent a parameterless method that can establish an improved convergence in the outcome direction.
Until now, the combined effect of the design variables on the response variables in the PMEDM method for processing nitinol SMA has not been thoroughly evaluated in previous studies.
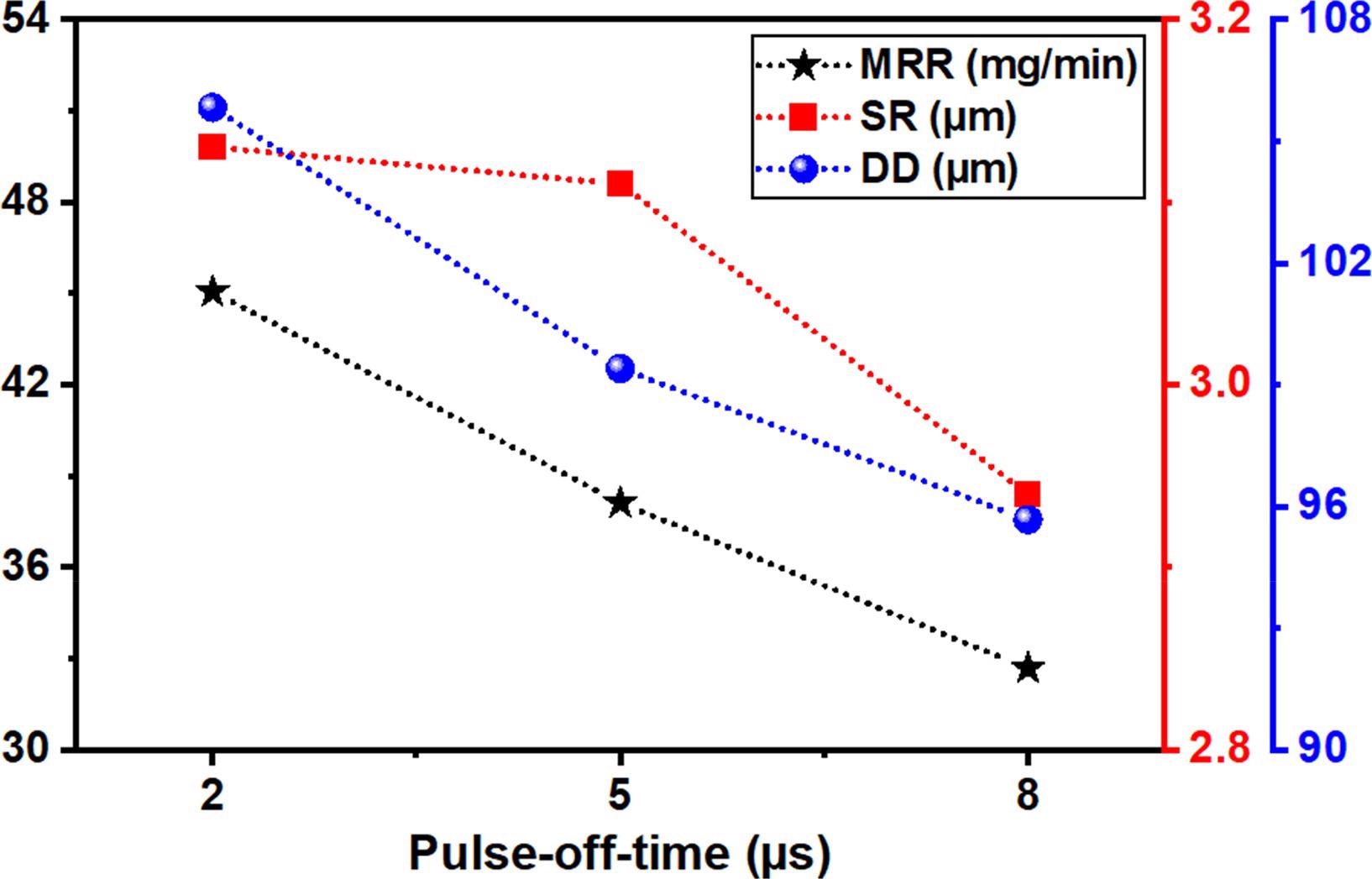
Influence of Toff on MRR, SR, and DD. Image Credit: Vora, J et al., Journal of Materials Research and Technology
Performance Evaluation of Nano-Graphene Mixed EDM
In this study, researchers investigated the performance of nano-graphene mixed EDM of nitinol SMA in terms of the overall effect of PC, pulse-on-time (Ton), pulse-off-time (Toff), and current on the material removal rate (MRR), DD, and SR of the machined surface. Researchers used the HTS technique for multi-objective optimization and assessed the extent of performance improvement of the EDM process by the addition of nano-graphene.
Nanographene was synthesized using the modified hydrothermal method. Nitinol SMA was machined using a nano-graphene mixed EDM process. A die-sinking EDM was employed for the process, with EDM oil serving as the dielectric fluid. Different concentrations of nano-graphene were mixed with the EDM oil in the working tank.
Ton, Toff, nano-powder concentration (PC), and current were selected as the key design variables, while MRR, DD, and SR were selected as the key response variables in the EDM process. A profilometer SJ-410 and an optical microscope were utilized for SR measurement and DD assessment, respectively.
The Minitab 17 software was employed to perform statistical analysis of the design variables using main effect plots, residual plots, and analysis of variance (ANOVA), while the Taguchi’s L9 (3 ^4) design was used to perform the experiments. Multiple and single responses were optimized using the HTS algorithm.
Non-dominated Pareto fronts were developed using the HTS method to realize a complete set of solutions. Researchers also performed validation trials to assess the suitability and ability of the HTS technique and used field emission scanning electron microscopy (FESEM) to determine the influence of nano-graphene particles on the machined surface morphology.
Significance of the Study
In the ANOVA results, Toff, Ton, and PC were identified as the highest contributing parameters with 45.72 percent, 29.37 percent, and 75.18 percent effect on DD, SR, and MR, respectively. Design variables PC, Toff, and Ton considerably impacted the MRR value, while all design variables impacted the DD and SR.
Residual plots validated the results of ANOVA statistics and the viability of multivariable correlations for better prediction of future results. A preferred combined positive trend of increasing MRR and decreasing DD and SR was observed in the results after the addition of two gram/liter nano-graphene in the dielectric oil.
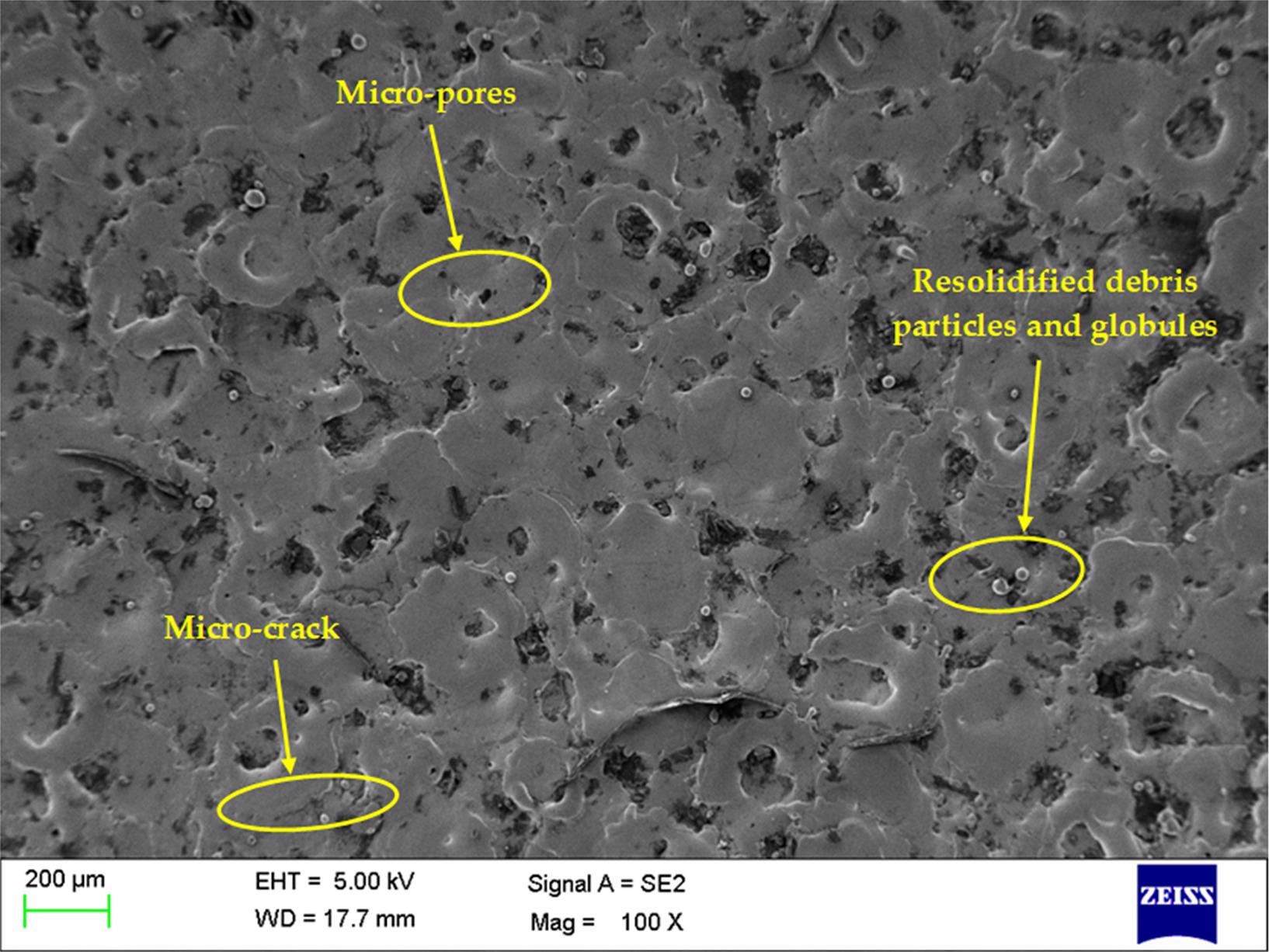
SEM analysis of machined Nitinol at Ton of 8 μs, Toff of 6 μs, PC of 2 g/L, and current of 6 A. Image Credit: Vora, J et al., Journal of Materials Research and Technology
Single-objective optimization results obtained from the HTS algorithm demonstrated a minimum DD of 86.07 micrometers, a minimum SR of 2.64 micrometers, and a maximum MRR of 62.66 milligrams per minute. The simultaneous optimization displayed optimal MR, SR, and DD values of 51.68 milligrams per minute, 2.92 micrometers, and 94.72 micrometers at a current of six amperes, PC of two grams per liter, Toff of six microseconds, and Ton of eight microseconds.
Pareto fronts provide a complete set of solutions, which allows the operator to select the proper Pareto point based on the specified values of DD, SR, and MRR. Validation trials displayed the suitability and ability of the HTS algorithm for PMEDM machining of nitinol SMA. FE-SEM analysis revealed the minor occurrence of micro-cracks, micro-pores, globules, and debris particles at two grams per liter nano-graphene PC due to the formation of smaller craters and homogenous sparking.
To summarize, the findings of this study demonstrated that the addition of nano-graphene powder at two grams per liter concentration in PMEDM can significantly improve the machined surface quality of advanced alloys such as nitinol SMA.
Disclaimer: The views expressed here are those of the author expressed in their private capacity and do not necessarily represent the views of AZoM.com Limited T/A AZoNetwork the owner and operator of this website. This disclaimer forms part of the Terms and conditions of use of this website.
Source:
Vora, J., Khanna, S., Paneliya, S. et al. Machining parameter optimization and experimental investigations of nano-graphene mixed electrical discharge machining of Nitinol Shape memory alloy. Journal of Materials Research and Technology 2022. https://www.sciencedirect.com/science/article/pii/S2238785422007372?via%3Dihub