Reviewed by Emily Henderson, B.Sc.Oct 12 2022
A new fabric, designed by textile engineers, has been woven out of ultra-fine nano-threads made from a blend of phase-change materials and other unconventional substances. This fabric can respond to varying temperatures to cool down or heat up its wearer based on the need.
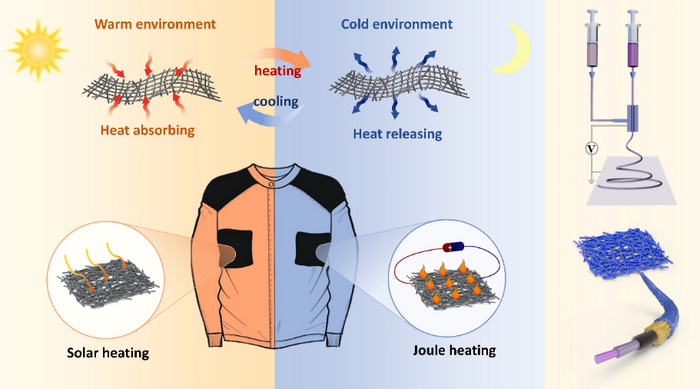
Graphical abstract. Image Credit: MODIFIED WITH PERMISSION FROM ACS NANO 2022, 16, 8, 12801–12812. COPYRIGHT © 2022, AMERICAN CHEMICAL SOCIETY.
Materials scientists have engineered an advanced textile with nanoscale threads comprising a phase-change material in their core, which can store and discharge large volumes of heat when the material shifts from liquid to solid.
Integrating the threads with photothermal and electrothermal coatings that improve the effect, they have fundamentally created a fabric that can rapidly cool the wearer down as well as warm them up as conditions vary.
An article illustrating the manufacturing method has been published in the American Chemical Society journal ACS Nano on August 10th, 2022.
Many professions, from farmworkers to firefighters, involve extreme cold or hot environments. Ice rinks, cold storage, bakeries, steel forges, and many other job settings necessitate workers to make repeated transitions between different and occasionally harsh temperatures.
Such common temperature variations are uncomfortable and can result in illness or even injury, and necessitate an inconvenient constant clothing change. A worker wearing a sweater will be warm when working in a cold meat locker but will overheat when outside that environment.
One alternative to get rid of the cold or heat stress of such workers, or any other person, from travelers to athletes, who undergo such discomfort, is the upcoming technology of personal thermal management textiles. These fabrics can instantly regulate the temperature of localized areas throughout the body.
Such fabrics regularly utilize phase-change materials (PCMs), which are capable of storing and later releasing large volumes of heat when the material shifts phase (or state of matter, for instance, from liquid to solid).
Paraffin is one such material that can in theory be combined with a textile material in various ways. When the temperature surrounding the paraffin touches its melting point, its physical state shifts from solid to liquid, which involves the absorption of heat. Then, heat is discharged when the temperature touches the freezing point of paraffin.
Regrettably, the integrally solid rigidity of PCMs in their solid form and leakage in their liquid form has thus far delayed their application in the field of wearable thermal regulation.
Several different approaches, including microencapsulation (wherein the PCM such as paraffin is coated in very small capsules), have been tried to enhance the “packaging efficiency” to surpass the rigidity and leakage issues.
The problem here has been that the manufacturing methods for phase-change micro-capsules are complex and very costly. Worse still, this option offers insufficient flexibility for any realistically wearable application.
Hideaki Morikawa, Corresponding Author and Advanced Textiles Engineer, Institute for Fiber Engineering, Shinshu University
Consequently, the team sought an option known as coaxial electrospinning. Electrospinning is a technique of manufacturing very fine fibers with diameters at the nanoscale. When a polymer solution held in a bulk reservoir, usually a syringe tipped with a needle, is linked to a high-voltage power source, electric charge amasses on the surface of the liquid.
Shortly a point is reached where the electrostatic repulsion from the amassed charge is greater than the surface tension causing a very fine jet of the liquid. As the jet of the liquid evaporates in flight, it is elongated more by that same electrostatic repulsion that created the jet, and the ensuing ultra-fine fiber is then gathered on a drum.
Coaxial electrospinning is quite similar but requires two or more polymer solutions fed from adjacent spinnerets, enabling the manufacture of hollow or coated nanofibers. These core-and-sheath fibers have an analogous structure to the coaxial cable one might use on one’s stereo but are much smaller.
In this scenario, the scientists encased the PCM in the center of the electrospun nanofiber to resolve the issue of PCM leakage. Apart from this, ultra-fine fibers allow very favorable flexibility that is suitable for human clothing.
To spread the range of work settings where the textile would be suitable, and the accuracy of thermal regulation, the scientists combined the PCM material with two other personal thermal regulation technologies.
Integrating photoresponsive materials—those that react when exposed to solar energy—with PCMs hypothetically provides the opportunity to improve the energy storage feature of the textile much more.
Furthermore, coating the composite material with polymers that turn electricity into heat (an electrothermal conductive coating) can make up for a similar expansion of energy storage should the working personnel be exposed to rainy, cloudy, or indoor situations.
The team integrated the three options—carbon nanotube and polydopamine solar absorbers, PCMs, and electro-conductive polymers composed of poly (3,4-ethylenedioxythiophene):polystyrenesulfonate (referred to as ‘PEDOT:PSS’)—into a single “trimode” thermoregulatory and wearable fabric.
This multi-core and shell structure allows synergistic support between its many components and offers instant thermal regulation that can adjust to a wide variety of environmental temperature variations.
The team currently aims to additionally enhance the phase-transition properties of the fabric and create real-world, wearable applications for their material.
Journal Reference:
Wu, J., et al. (2022) A Trimode Thermoregulatory Flexible Fibrous Membrane Designed with Hierarchical Core–Sheath Fiber Structure for Wearable Personal Thermal Management. ACS Nano. doi.org/10.1021/acsnano.2c04971.