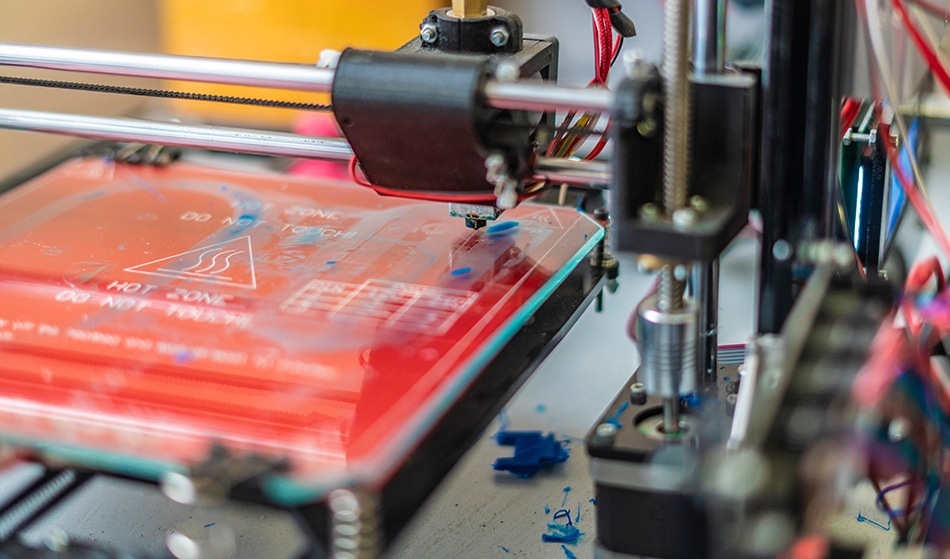
Image Credits: Mike_shots/shutterstock.com
After gaining wide acceptance on the macro scale, additive manufacturing is increasingly being used at the nanometer scale, currently allowing for the fabrication of minuscule 3D objects with nanoscale accuracy. Simply put, this is 3D printing on a very, very small scale.
Items with micro and nanoscale features are commonly used in many different industries including in the medical, optics, electronics and biotechnology fields. A shift in the direction of miniaturization in many of these industries has laid bare the constraints of commonplace micro and nano-manufacturing techniques with regards to processing ability, speed, versatility, dependability and scalability.
Micro and nanoscale additive manufacturing technologies are increasingly being viewed as a way to overcome these challenges. As opposed to other nanoscale fabrication techniques, additive manufacturing is generally simpler, faster, more cost-effective and capable of creating both high aspect ratio structures and intricate freeform structures. Still very much in development, nanoscale additive manufacturing an area of significant study around the planet.
Laser-based fabrication systems are currently being used to create products with nanoscale precision. These systems use ultra-fast laser pulses lasting just femto and picoseconds.
Below are a couple of additive manufacturing techniques capable of nanoscale precision.
Laser-Induced Forward Transfer (LIFT)
Developed at the University of Southampton, Laser-Induced Forward Transfer (LIFT) is a 3D printing method acceptable for extremely detailed printing of various materials, including DNA 'sensors' or nanoparticle inks. LIFT and its variants have gained a great deal of interest in the nanofabrication community over the last few years.
The principal benefit of LIFT is its versatility in processing materials with a high degree of precision. The fabrication sequence involves focusing ultra-fast laser pulses onto a thin film that has been coated onto a transparent support substrate. A pixelated transfer of material is caused by the heating and subsequent melting of the film, causing material to shift to a nearby substrate. The process enables the 3D printing of a range of materials onto non-traditional substrates and in a range of unique geometries.
At present, the LIFT system leverages femtosecond, picosecond and nanosecond laser pulses. For nanosecond pulses, LIFT can produce droplet sizes between 500 and 700 nm. LIFT operations using femtosecond laser pulses are capable of generating droplet sizes of around 300 nm.
One growing application of the LIFT system is the direct 3D printing of organic substances for tissue fabrication, regenerative medicine and biosensor technology. Researchers that developed the system have said they are currently focused on fabricating smaller and smaller scale structures. They say they are also developing ways to fabricate using transparent materials, which are difficult to print via laser irradiation.
Nanoscribe
Developed in Germany through a spin-off of the Karlsruhe Institute of Technology (KIT), Nanoscribe is a line of 3D printers capable of nanometer resolution.
The Nanoscribe Photonic Professional GT is a flagship 3D printing device that uses a two-photon laser setup to cure resins into intricate objects in almost any shape, including scaffolds, crystal lattices, smooth contours, undercuts and bridges. The system’s extremely high printing resolution offers users significant design flexibility when fabricating extremely small, intricate parts and features. Moreover, the device uses a relatively basic workflow to quickly fabricate based on digital 3D models. The device was designed for applications in biomedical engineering, micromechanics, micro-optics and other scientific fields.
Although the Nanoscribe is primarily known for its capability to create 3D microstructures through additive manufacturing, it can also create 2D structures with extremely high resolution. In addition to using resins as source material, the Nanoscribe system is also capable of fabrication using hydrogels, nanoparticle resins and custom-made materials.
Sources and Further Reading
Disclaimer: The views expressed here are those of the author expressed in their private capacity and do not necessarily represent the views of AZoM.com Limited T/A AZoNetwork the owner and operator of this website. This disclaimer forms part of the Terms and conditions of use of this website.