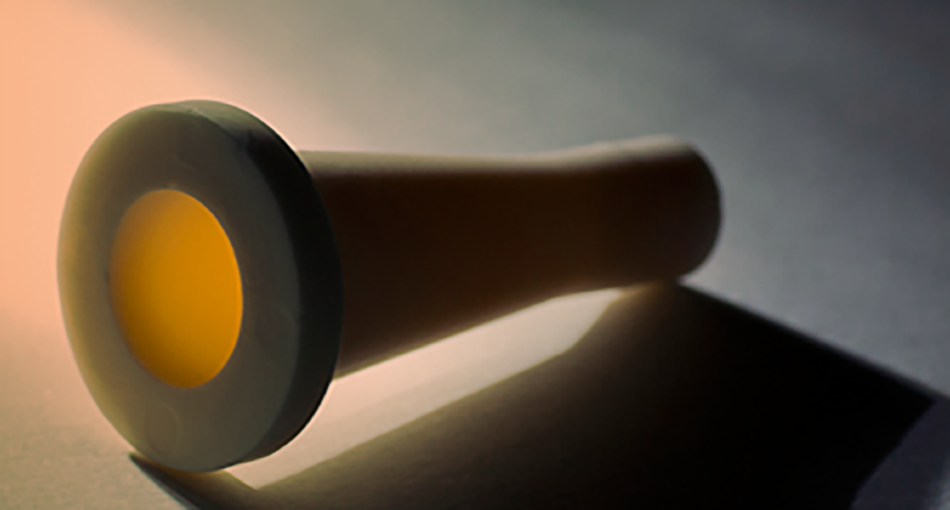
Wikimedia Commons
As one of the most effective materials of our time, technical ceramics are increasingly being utilized to replace metals, polymers and refractory materials in a number of applications, making the impossible suddenly possible – but what are they and how are they made?
These specialized, high-performance ceramics have exceptional mechanical, electrical, thermal and biochemical properties, with different technical ceramics exhibiting different properties. There are four major groups:
- silicate ceramics: one of the oldest type of ceramics primarily consisting of natural raw materials in conjunction with alumina,
- oxide ceramics: mainly metal oxides, aluminum or zinc oxides, aluminum titanate or dispersion ceramics,
- non-oxide ceramics: based on carbon, nitrogen or silicon compounds,
- piezo-ceramics, also known as functional ceramics: these convert mechanical parameters into electrical parameters or electrical signals into movement or vibration.
Properties
Technical ceramics must meet very high criteria in terms of their properties; they must exhibit:
- flexural and compressive strength,
- biocompatibility and food compatibility,
- chemical and corrosion resistance,
- electrical insulation,
- density and stiffness, hardness,
- dielectric strength,
- piezoelectricity and dynamics,
- thermal shock and fluctuation resistance,
- thermal expansion, insulation, and conductivity,
- temperature and wear resistance.
Technical ceramics can be more than four times harder than stainless steel, and this high rigidity translates into excellent wear resistance, meaning that many can keep their precise, high-tolerance finish much longer than any other material. Their exceptional wear resistance also means that they can withstand incredibly high temperatures while still retaining their mechanical and electrical properties. Such materials will still function long after other materials begin to fail, and so are suited to use in furnaces, jet engines, and brake systems.
These unique materials are much lighter than steel or titanium, and this low density means they are used in a number of applications where no other material can match their performance and longevity. They also exhibit extreme compressive strength, but only when compressed.
Technical ceramics’ excellent electrical properties mean they are brilliant electrical insulators and are useful in high-temperature applications where other materials’ mechanical and thermal properties have a habit of degrading. Their thermally conductive and insulative properties mean they are ideal for use in heat sinks or exchangers in many electrical applications.
Technical ceramics can function where almost no metal can maintain their properties; this ultra-high temperature ability makes them ideal for use in engines, turbines, and bearings. They are also chemically stable and have a low chemical solubility, making them highly resistant to corrosion - metals and polymers do not exhibit these same capabilities.
Manufacture
Technical ceramics’ unique characteristics can be imparted throughout the manufacturing process, during sintering for example. The targeted manipulation of a structural part’s microstructure results in an improved end product whose properties vary even if the base product is identical.
By altering the chemical formulation or manufacturing process, technical ceramics can be optimized for technical applications and their properties tailored to meet a variety of demanding conditions. Technical ceramics’ high performance can be attributed to the extremely high purities, most commonly metal compounds combined with oxides, carbides, and nitrides.
Components made from ceramic materials are increasingly becoming the only solution available for technical challenges that can’t be solved with conventional materials. They are often very advanced compared to competing materials such as metal and plastic in their respective fields of application.
When used correctly, technical ceramics can increase a product’s lifespan, improve its efficiency, decrease the overall maintenance costs and improve product performance. Technical ceramics are suitable for highly stressed parts in machines, plants, and devices. Uses might include centering pins, nozzles, cutting tools or side bearings; they might also be utilized in the automotive industry, electronics, medical technology, energy and environment and in general equipment and mechanical engineering.
Sources
Disclaimer: The views expressed here are those of the author expressed in their private capacity and do not necessarily represent the views of AZoM.com Limited T/A AZoNetwork the owner and operator of this website. This disclaimer forms part of the Terms and conditions of use of this website.