Graphene is a much-celebrated thin-film material with numerous, diverse properties, making it suitable for a wide range of applications. Its development – as well as the continual development of applications for graphene – is concurrent with the development of advanced metal alloys. The graphene industry can be expected to work alongside – and in some cases against – the advanced alloy industry in coming years.
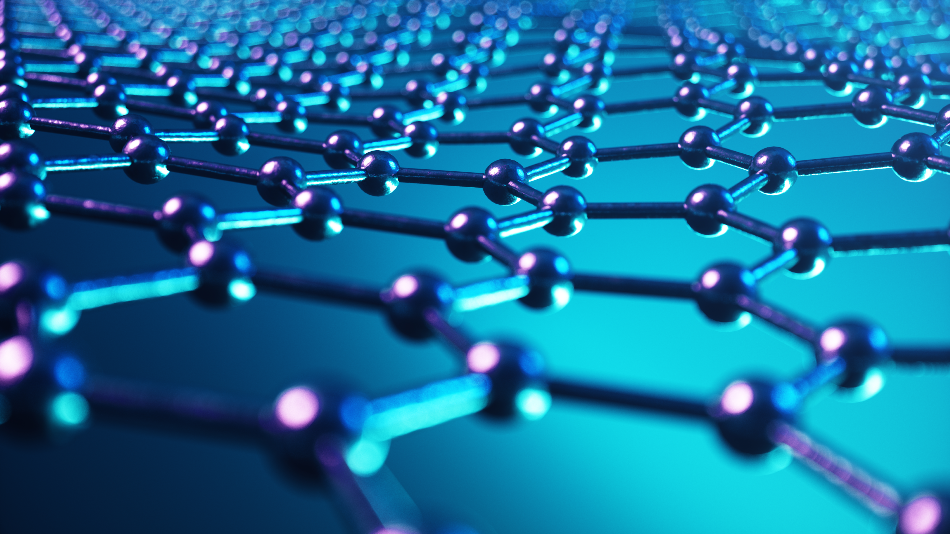
ImageCredit/Shutterstock:Rost9
Graphene
Graphene was first discovered in the 1960s but received little interest and further research in the academic community. It was not until 2004 when researchers from the University of Manchester UK, Andre Geim and Konstantin Novoselov, rediscovered the material, that graphene began to attract the interest of science and industry.
Graphene consists of one layer of carbon atoms arranged in a two-dimensional hexagonal lattice. In this structure, each carbon atom forms a vortex. Graphene is an allotrope of carbon, or structural configuration of the element, forming the basic building block for several other allotropes including graphite and charcoal.
Geim and Novoselov isolated and characterized the material and were awarded the Nobel Prize for Physics in 2010 for their work. The material as they characterized it; is transparent, flexible and electrically conductive.
Applications for graphene are extremely varied, with proposals of smartphone touch screens, wearable technology, filtration systems and composite materials all being made in recent years. It is already being used in touch panel modules, sporting equipment and printer-powder.
Graphene and advanced alloys
In the areas of composite materials and advanced materials research, graphene has been thoroughly investigated as a potential partner material. Applied to a base layer (or substrate) material, graphene can impart its impressive features onto the whole composite. It is also applied in other forms, such as mixed into the alloy in flakes. These applications are under scrutiny in the field of advanced alloys.
Advanced alloys are combinations of metal elements manufactured for unique or extreme features including high thermal resistance, electric conductivity, mechanical strength. They are most frequently utilized in the aerospace industry, whereby high-performing materials are a prerequisite for safe and effective flight.
Graphene nanoflakes reinforce aluminium alloys
Graphene nanoflakes (GNFs) – nanometre-sized flakes of the advanced material – can be mixed in with high-performing aluminium alloys, adding even more strength to the material. Graphene oxide is chemically reduced in a colloidal suspension to create GNFs, which while made up of several layers of graphene, still retain incredible mechanical strength properties – their tensile strength is estimated to be 100 times greater than structural steel.
GMF's can be mixed with aluminium alloys using a powder metallurgy process. This results in an alloy where the GNF material is consistently and evenly spread throughout the composite, resulting in good integration and reliable material properties. This technique results in an advanced aluminium alloy with up to 50% greater yield strength than the original metal.
Graphene in titanium aluminide alloys
Alloys mixing aluminide metals and titanium have been developed for the aerospace industry. These are even stronger than the strongest aluminium alloys and lighter than the already lightweight material. Still, increasing strength in this alloy without increasing density remains a goal for many within academia and industry.
Coating carbon fibres with graphene and then combining those with the titanium aluminide alloy – again using powder metallurgy techniques – can reduce the density of the metal, while providing remarkable mechanical strength. Other techniques for combining graphene-coated carbon fibres with titanium aluminide alloys include melt-spun and vacuum melt techniques.
The new composite material was found to exhibit a fracture strain ratio of 26% and average compression strength in the region of 2,300 Mpa. This is compared to a fracture strain of 16% and compression strength of 1800 Mpa in pure titanium aluminide alloys – which is already impressive.
Source
Cuffari, B. (2019). How Graphene Could Affect the Alloy Industry. [online] AZoM.com. Available at: https://www.azom.com/article.aspx?ArticleID=17993.
Disclaimer: The views expressed here are those of the author expressed in their private capacity and do not necessarily represent the views of AZoM.com Limited T/A AZoNetwork the owner and operator of this website. This disclaimer forms part of the Terms and conditions of use of this website.