Many industrial processes involve the heat treatment of materials, such as metals, plastics, and composites. Commonly used heat transfer fluids such as water, ethylene glycol, and oils exhibit relatively low thermal conductivity compared to solids.
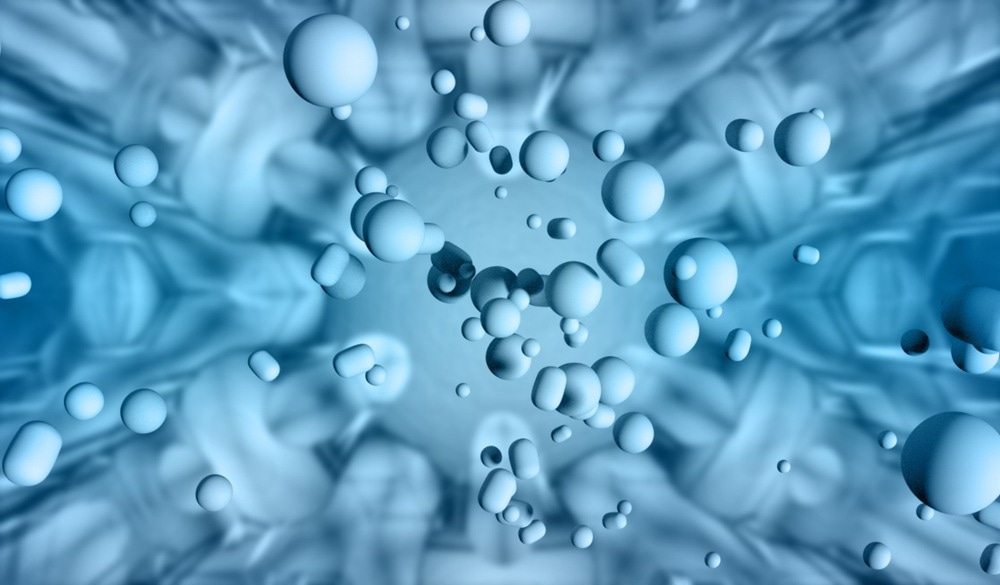
Image Credit: GiroScience/Shutterstock.com
By using nanofluids, which are colloidal suspensions of solid nanoparticles in a base fluid, researchers and engineers can increase the thermal conductivity of the heat transfer fluid, thus saving energy and reducing the required processing time.
Heat treatment is a process where materials are heated or cooled in a specific sequence to facilitate material processing, prevent materials from irreversible thermal damage, or improve their mechanical properties.
Benefits of Materials Heat Treatment
Heat treatment of metals and metal alloys is a particularly important process used in steel manufacturing. By choosing the appropriate heat treatment method, the manufacturers can enhance the hardness, strength, and wear resistance of the metal or improve its ductility. However, not all of the metal properties can be modified in one operation. For example, the quench hardening of a metal, a process commonly used in the steel industry to increase the reliability of the final product, may cause brittleness.
Here, once the material reaches a specific temperature following heating, it is held and then quenched in a cooling medium. The quenching process is carried out to trigger physical processes like heat transfer, which initiates other processes, phase transformation, and strain or strain evolution.
The outcome of the quenching process primarily depends on the heat transfer characteristics of the quenching medium. In the context of industrial heat treatment of metal, commonly used quench fluids, such as water, brine solution, and oils, the scope for enhancing the heat transfer is very limited. Thus, material scientists in the industry and academia focus on designing quench media with enhanced heat transfer characteristics.
Developments in Nanotechnology Facilitated the Emergence of Nanofluids
Modern nanotechnology enables the large-scale manufacturing of nanomaterials with an average particle size smaller than 50 nanometers. The unique properties of these nanomaterials include size-dependent physical properties, extremely large specific surface area, and tunable surface properties. The colloidal suspensions of nanoparticles in carrier fluids are called nanofluids. Commonly used nanomaterials in nanofluids are oxide ceramics (Al2O3, CuO), carbides (SiC), nitrides (AlN, SiN), metals (Al, Cu), and non-metals (graphite, carbon nanotubes, and others). The base fluids include water, ethylene or tri-ethylene glycol, oils, and polymer solutions.
Thermal and Physical Properties of Nanofluids
The nanofluids are predominantly produced using a two-step method, where nanoparticles are first synthesized and then dispersed in the base fluid. The extensive research on nanofluids in the past two decades demonstrated that the addition of nanoparticles to conventional fluids causes dramatic changes in the thermo-physical properties of the fluid. The high specific surface area of the nanoparticles improves the heat transfer between the nanoparticles and the fluid.
The boiling behavior of the fluid at surfaces is also affected, as the nanoparticles fill up the discontinuities at the solid-fluid interface, thus affecting the critical heat flux. The dispersion stability of the nanofluid, predominantly governed by the Brownian motion of the nanoparticles, ensures stable and isotropic heat exchange. Experimental evidence shows that nanofluids enable a reduction in pumping power, compared to pure liquid, to achieve an equivalent heat transfer rate. In addition, nanofluids offer adjustable properties, such as wetting kinetics and heat removal characteristics, by varying particle concentration and composition to suit different applications.
Importantly, a large enhancement of the thermal conductivity can be achieved at very low nanoparticle concentrations, which completely preserves the Newtonian behavior of the fluid without noticeable effects on the fluid viscosity and the required pressure drop during the fluid pumping. All these unique characteristics of the nanofluids can be exploited in the industrial heat treatment of materials.
Bio-Based Nanofluids for Steel Hardening
Researchers from the SSN College of Engineering in Chennai, India demonstrated the benefits of using low-cost sustainable biochar-based nanofluid (biochar is carbon residue remaining after the pyrolysis of biomass) as a quenching medium in low-carbon steep processing.
Adding only 0.25 wt% of thermally annealed biochar to distilled water resulted in a nanofluid that achieved a much higher cooling rate and resulted in smaller surface roughness, higher hardness, and more refined microstructure of the processed low-carbon steel when compared to conventionally quenched specimens.
Surfactants Improve the Performance of Organic Nanofluids
Similarly, a research group at the department of metallurgical and materials engineering at Universitas Indonesia investigated how using a nanofluid prepared by the addition of carbon nanoparticles in oil as a quenching medium affects the properties of medium carbon steel JIS S45C.
The microstructure and hardness of the steel specimen showed significant dependence on the nanoparticle volume fraction in the nanofluid. Compared to oil quenchant, quenching in oil-based nanofluid with 0.2 vol% nanoparticle content resulted in a higher hardness of the specimen. Higher nanoparticle concentrations resulted in lower steel hardness, probably due to particle agglomeration.
Adding anionic surfactants, such as sodium dodecylbenzene sulfonate, to the nanofluid allowed the researchers to improve the quenching process further and increase the steel hardness.
Ceramic Nanoparticles Help Reducing Steel Shape Distortion
The improvement of the hardness and the microstructure of low-carbon steel when using ceramics-based nanofluid (Al2O3 nanoparticles suspended in water-ammonia solution) as a quenching medium was also reported by scientists at the Poznań University of Technology in Poland. Their results established that the nanofluid quenching resulted in smaller shrinkage of the steel specimen while improving its hardness and reducing the processing time.
The addition of nanoparticles to conventional quenching fluids improves their heat transfer and wetting properties, thus minimizing shape distortion of the treated components and improving the reproducibility of the quench hardening treatment. In addition, using bio-derived nanomaterials to prepare nanoquenchants can improve the cost efficiency and sustainability of the industrial heat treatment processes.
References and Further Reading
Hassoni, S. M., et al. (2020) The Role of ZnO Nano-fluids on Heat Treatments of Medium Carbon Steel. 2020 IOP Conference Series: Materials Science and Engineering. 881, p. 012095. doi.org/10.1088/1757-899X/881/1/012095
Arularasan, R & Babu, K (2021) Thermally annealed biochar assisted nanofluid as quenchant on the mechanical and microstructure properties of AISI-1020 heat-treated steel—a cleaner production approach. Biomass Conversion and Biorefinery. doi.org/10.1007/s13399-021-01737-x
Riza, R. I., et al. (2020) Cooling Rate Observation in Quenching Process Using Carbon Nanofluids for S45C Carbon Steel. Key Engineering Materials, 833, p.13–17. Trans Tech Publications, Ltd. doi.org/10.4028/www.scientific.net/kem.833.13
Oktavio, L., et al. (2019). Effect of sodium dodecylbenzene sulfonate as anionic surfactant on water based carbon nanofluid performance as quench medium in heat treatment. IOP Conference Series. Materials Science and Engineering, 622(1). doi.org/10.1088/1757-899X/622/1/012009
Mahiswara, E. P., et al. (2018) Characterization of oil based nanofluid for quench medium. IOP Conference Series: Materials Science and Engineering, 299, p. 012068. doi.org/10.1088/1757-899X/299/1/012068
Łyduch, K., Gęstwa, W. (2018) The influence of chemical composition on the dimensions change of hardened steels in nanofluids. Archives of Mechanical Technology and Materials, 38, pp. 29-34.
Disclaimer: The views expressed here are those of the author expressed in their private capacity and do not necessarily represent the views of AZoM.com Limited T/A AZoNetwork the owner and operator of this website. This disclaimer forms part of the Terms and conditions of use of this website.