This article discusses the critical role of thermal analysis methods in overcoming the thermal challenges of semiconductor devices.
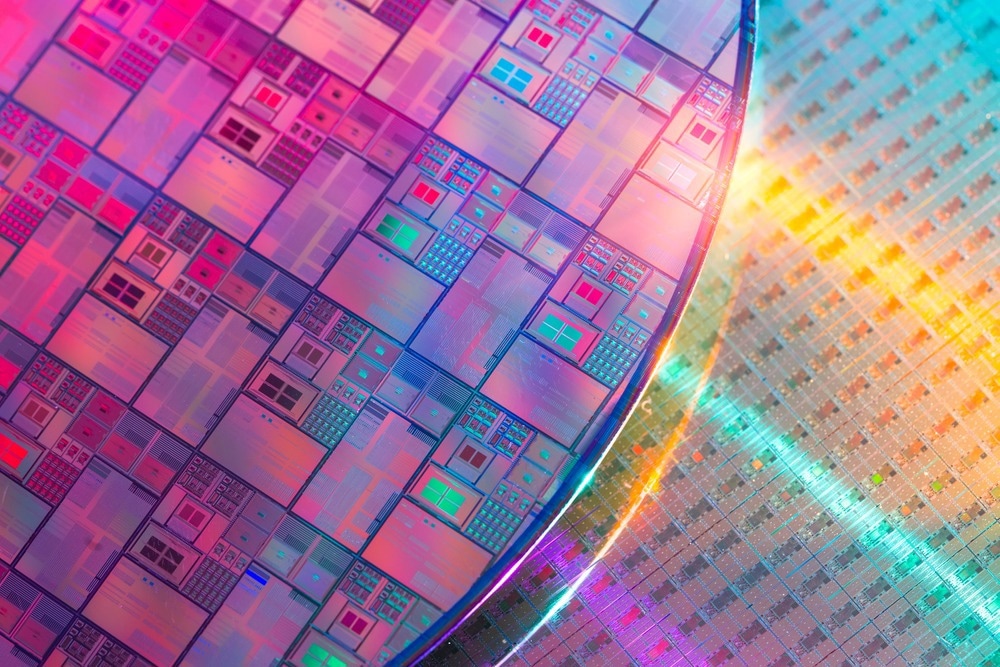
Image Credit: asharkyu/Shutterstock.com
Importance of Thermal Analysis in Semiconductor Device Design
Semiconductor device manufacturing requires careful consideration of key device fabrication and operation aspects, including the fabrication process, heat dissipation from the devices to the environment, and transport of holes and charge carriers inside the device.
Efficient dissipation of heat generated by a semiconductor device during operation to its surroundings is crucial to ensure device reliability. For instance, the mean-time-to-failure (MTTF) of a semiconductor device is decreased by a factor of two with every 10 oC increase in device operating temperature.
Thus, the device operating temperature must remain below 75-85 oC to ensure reliable operation. Additionally, the growing trend in the semiconductor industry towards large-scale integration of transistors on a single integrated chip (IC) to develop smaller and more complex chips with higher operating speed and computing power has also increased the need for efficient heat dissipation to achieve better chip performance.
These factors have increased the importance of thermal analysis to overcome the thermal challenges in semiconductor devices and achieve improved device performance. However, no single thermal analysis method is effective in all conditions. Thus, good thermal assessments often require a combination of analytical calculations using thermal modeling, empirical analysis, and thermal specifications.
Thermal Analysis Methods for Semiconductor Devices
Thermal analysis methods are primarily categorized into numerical and analytical approaches. The analytical approach involves the identification of proper analytical solutions for structures with regular geometries, such as rectangular, cylindrical, and semi-infinite geometries.
For instance, a complete solution of temperature at any location inside or on the surface of a rectangular four-layer structure with several heat sources on the structure surface has been derived using analytical approaches. A novel technique has also been developed based on this solution for the real-time thermal design of ICs with a large number of small heat sources.
The numerical approach includes the finite element technique, boundary element method (BEM), and finite difference analysis. General-purpose software packages are commercially available for these three numerical techniques. Numerical analysis methods can be applied to structures with irregular or regular geometries.
For instance, the finite difference technique has been used to determine the transient and steady-state temperatures of a p-i-n diode mounted on a special package, to analyze the temperature distribution of a laser diode bonded to a heat sink to investigate the impact of bonding layer voids on temperature distribution, and for transient and steady-state temperature simulation of thermal test chips bonded on an alumina substrate.
The finite difference technique has also been used to simulate the thermal performance of p-i-n grid array packages for high-density very large-scale integration (VLSI) and large-scale integration (LSI) logic circuits. The finite element analysis has been utilized to simulate the thermal stress and temperature distribution of leadless chip carriers mounted on a substrate.
The BEM is a relatively new technique that has multiple advantages over "domain" type solutions, such as finite difference and finite element, including the discretization of only the surface of the body under consideration and the facility to represent surfaces at infinity.
Thus, BEM can be used in structures, such as three-dimensional, multi-layer structures, that lack a numerical approach or an analytical solution. The simplicity of the input data required to solve problems is also a significant advantage of boundary element solutions.
BEM can be categorized as indirect and direct methods based on the formulation of integral equations. The indirect formulation method is less versatile and general compared to the direct formulation method, as the unknown quantities in the integral equations do not represent the physical variables of the problem.
In the direct formulation method, the unknown quantities in the integral equations represent the actual physical variables of the problem. Thus, in a thermal analysis, the direct formulation method can directly yield the heat flux and temperature densities on the system boundary. At the same time, the integral equation solution within the body can be derived by numerical integration from the boundary values.
BEM has been used to investigate the thermal properties of multiple-layer rectangular structures. Studies have demonstrated that the results obtained using BEM are similar to that of analytical solutions, which indicates the accuracy of BEM.
The transmission line matrix and analog electrical models are the prominent alternatives to numerical and analytical approaches for the thermal analysis of solid-state devices. For instance, the image method has been employed as a semi-numerical and semi-analytical approach to study the three-layer infinite plate structure.
Recent Studies Involving Thermal Analysis of Semiconductor Devices
In a recent study published in the journal Energies, researchers proposed a new mathematical model for thermal analysis of the case and junction temperature of a thyristor from a power rectifier. The finite element method-based Pro-MECHANICA software package was used to perform the thermal simulations in steady-state conditions.
The proposed mathematical model included a new formula to determine the power losses of power semiconductor devices used in bidirectional rectifiers supplying a resistive-inductive load and mathematical expressions for case-junction thermal resistance and environment-heatsink thermal resistance variation against airspeed during forced cooling.
The thermal model can analyze the thermal behavior of power semiconductors in steady-state conditions at different values of the direct current, firing angle, and airspeed in case of forced cooling, and at various types of load. The case and junction temperature of a power thyristor was computed successfully using the model.
Moreover, the case and junction temperature values obtained from simulations and experiments displayed good concordance with the theoretical values obtained using the model, which confirmed the feasibility of the new mathematical model. Thus, the new model can improve the design of power assembly and offer new solutions for better cooling of power semiconductor devices.
To summarize, thermal analysis methods will become more critical with the ever-increasing requirement of effectively dissipating the heat from increasingly complex semiconductor devices. An integrated approach that combines different thermal analysis methods can become more effective in the future for overcoming the thermal challenges of semiconductor devices.
References and Further Reading
Palisoc, A.L., Lee, C.C. (1990). Thermal Analysis of Semiconductor Devices. Electrical Engineering Applications. Topics in Boundary Element Research, 7. https://doi.org/10.1007/978-3-642-48837-5_2
Plesca, A. (2020). Thermal Analysis of Power Semiconductor Device in Steady-State Conditions. Energies, 13(1), p. 103. https://doi.org/10.3390/en13010103
Thermal Analysis of Semiconductor Systems [Online] Available at https://www.nxp.com/docs/en/white-paper/BasicThermalWP.pdf
Disclaimer: The views expressed here are those of the author expressed in their private capacity and do not necessarily represent the views of AZoM.com Limited T/A AZoNetwork the owner and operator of this website. This disclaimer forms part of the Terms and conditions of use of this website.