Graphene coatings are revolutionizing industries by offering enhanced durability, conductivity, and corrosion protection. This article provides insights into the production, application, and benefits of graphene coating, focusing on the various industries harnessing its potential.
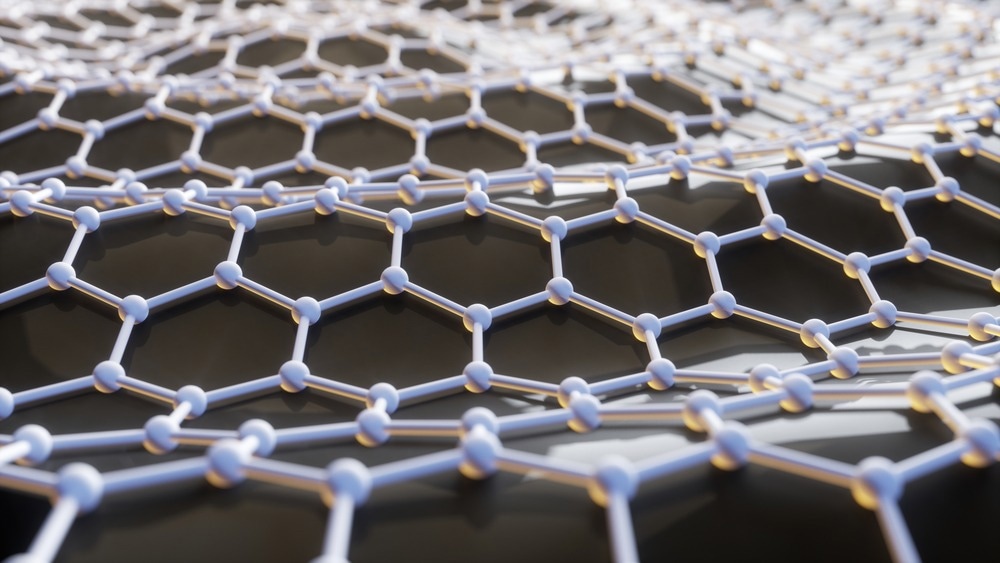
Image Credit: OliveTree/Shutterstock.com
What is a Graphene Coating?
Graphene coatings are a thin layer of graphene applied to the surfaces of a material. Graphene is a two-dimensional lattice of carbon atoms with remarkable properties such as high mechanical strength (1100 GPa), conductivity, and barrier effects. It is six times lighter and more flexible yet 200 times stronger than steel at the molecular level.
Graphene coating provides a protective surface layer, offering customizable characteristics such as thickness and conductivity. It effectively hinders the diffusion of oxygen atoms, preventing oxidation on the coated surface.
Even if graphene is oxidized, the coating acts as a barrier, significantly reducing the upward diffusion of oxygen and protecting against oxidation. Multilayer graphene coatings can further enhance protection, addressing vulnerabilities at defect sites.
Graphene coatings have potential applications in adhesives, anti-bacterial coatings, solar paints, insulation, rust prevention, anti-fog solutions, UV protection, and non-stick coatings. The material's unique properties make it a subject of extensive research for its potential to revolutionize various industries.
How Are Graphene Coatings Made?
Chemical vapor deposition (CVD) is a common and reliable technique for producing high-quality graphene coating over large areas. It involves the thermal decomposition of a carbon-rich source, leading to the deposition of carbon atoms in a honeycomb pattern on a metallic catalyst film.
CVD-based graphene coating is known for its high quality and characteristics such as imperviousness, high purity, fine grain, and increased hardness.
Rapid thermal annealing is another approach for producing protective graphene coating. Single-layer acetone-derived graphene coating has shown improved corrosion resistance by subjecting the material to high temperatures, significantly reducing the corrosion current density compared to untreated or mechanically polished surfaces.
Multilayer graphene coating is generally considered more reliable due to its enhanced protective properties.
How Are Graphene Coatings Applied?
Graphene coating is applied using various methods, such as spraying, dip coating, spin coating, and roll-to-roll coating, depending on the desired application and the substrate.
Spray coating involves dispersing graphene flakes or a graphene-based solution onto the target surface using a solvent. It is a simple and efficient method for coating large areas quickly, often used for corrosion protection and conductive coatings.
Researchers from the University of Illinois at Chicago and South Korea have developed a scalable version of this technique using a Laval nozzle and supersonic gas flow. The method improves adhesion, achieves an ideal lattice structure and offers control over graphene coating thickness and quality.
Spin coating is a common laboratory technique where a graphene solution is dispensed onto a substrate and rapidly spun. This spinning action spreads the solution evenly and removes excess, resulting in a thin and uniform graphene coating on the substrate.
Dip coating immerses the substrate in a graphene solution, slowly withdrawing it to form a thin graphene film.
What Are the Benefits of Graphene Coatings?
Graphene coating adds minimal thickness to the underlying sample while providing excellent conductivity for electricity and heat. The aromatic C=C bond network in graphene spreads across the entire basal plane due to the delocalization of the electron cloud, giving graphene coating high thermal stability.
Graphene's high flexibility and mechanical and chemical stability preserve the substrate's optical appearance, allowing it to conform to different surface roughness and curvature.
The chemical inertness and impermeability of graphene coating make it an ideal protective barrier, surpassing diamond stability under high pressure and exposure to superheated water. In addition, the high light transmission of graphene coating (97%) across a wide electromagnetic spectrum enhances its effectiveness as a protective coating.
Graphene coating offers a deep gloss, vibrant color, superior hydrophobicity, and dust-repelling properties, enhancing appearance and cleanliness.
Taking Graphene Coatings to Industry
Aerospace
Graphene coating is highly sought after in the aerospace industry for its ability to shield aircraft surfaces from lightning-induced electrical damage. Additionally, these coatings enable the detection of strain rate, providing pilots with real-time information on changes in stress levels experienced by the aircraft wings during flight.
Graphene-coated wings reduce composite layers, leading to a lighter aircraft, improved fuel efficiency, and lower environmental impact.
Automobile
Graphene coating offers advanced protection for the external elements of automobiles, such as chassis and body coatings, providing benefits such as superior hydrophobic properties, resistance to scratches and contaminants, and self-healing capabilities.
It effectively protects against corrosion, extends the lifespan of automotive components, and enhances scratch resistance, maintaining the vehicle's appearance and reducing maintenance needs.
Electronics
Graphene coating has shown significant potential in enhancing electrical circuits for flexible and wearable electronics, such as bendable smartphones, smart health patches, and large folding display screens.
A study published in ACS Applied Materials & Interfaces demonstrated that growing graphene directly onto copper lines improved their conductivity and durability, allowing them to withstand 200,000 folds without damage. This suggests that graphene coating can extend the lifespan of flexible electronics.
Another study published in ACS Applied Nano Materials demonstrated that graphene-coated gold surfaces are more corrosion-resistant from sweat, making them ideal for implantable biosensors and smart patches for monitoring health conditions.
Energy
Graphene coating improves heat transfer in thermal power plants by preventing the formation of insulating water films on the metal surface.
MIT researchers achieved a fourfold increase in thermal conductivity with a graphene coating, surpassing polymer coatings. This technology enhances the efficiency of heat exchangers and steam condensers by 2-3 percent, offering significant benefits to the energy industry.
The Sixth Element Materials designed an anticorrosion graphene coating primer for offshore wind power towers, offering a cost-effective alternative to zinc-rich epoxy primers.
The coating's first application on a wind turbine in the Rudong Sea area exceeded 2500 hours in salt spray testing, showcasing its remarkable performance. With 1% graphene content, the coating revolutionized the anticorrosion system by reducing the zinc powder requirement by over 50%.
The graphene coating market faces challenges in terms of limited awareness, low mass production capability, and high production costs, which may impede its growth. However, the growing energy, pharmaceutical, automobile and electronics industries, coupled with advancements in technology and increased focus on research and development, offer promising growth prospects for the graphene coating market.
References and Further Reading
Clavin, W. (2022). Graphene Boosts Flexible and Wearable Electronics. [Online]. California Institute of Technology. Available from: https://www.caltech.edu/about/news/graphene-boosts-flexible-and-wearable-electronics
Cui, G., Bi, Z., Zhang, R., Liu, J., Yu, X., & Li, Z. (2019). A Comprehensive Review on Graphene-Based Anti-Corrosive Coatings. Chemical Engineering Journal, 373, pp. 104-121. doi.org/10.1016/j.cej.2019.05.034
David L. Chandler. (2015). Graphene Boosts Flexible and Wearable Electronics. [Online]. MIT News Office. Available from: https://news.mit.edu/2015/graphene-coating-more-efficient-power-plants-0529
Graphene-info. (2023). Graphene Coating: Introduction and Market Status. [Online]. Available from: https://www.graphene-info.com/graphene-coating
Kim, D. Y., Sinha‐Ray, S., Park, J. J., Lee, J. G., Cha, Y. H., Bae, S. H., ... & Yoon, S. S. (2014). Self‐healing reduced graphene oxide films by supersonic kinetic spraying. Advanced Functional Materials, 24(31), pp. 4986-4995. doi.org/10.1002/adfm.201400732
Lu, C. H., Leu, C. M., & Yeh, N. C. (2021). Polymer-Compatible Low-Temperature Plasma-Enhanced Chemical Vapor Deposition of Graphene on Electroplated Cu for Flexible Hybrid Electronics. ACS Applied Materials & Interfaces, 13(34), pp. 41323-41329. doi.org/10.1021/acsami.1c11510
Lu, C. H., Shang, K. M., Lee, S. R., Tai, Y. C., & Yeh, N. C. (2022). Graphene on Nanoscale-Thick Au Films: Implications for Anticorrosion in Smart Wearable Electronics. ACS Applied Nano Materials, 5(3), pp. 4343-4349. doi.org/10.1021/acsanm.2c00401
Ollik, K., & Lieder, M. (2020). Review of the Application of Graphene-Based Coatings as Anticorrosion Layers. Coatings, 10(9), p. 883. doi.org/10.3390/coatings10090883
Prasai, D., Tuberquia, J. C., Harl, R. R., Jennings, G. K., & Bolotin, K. I. (2012). Graphene: corrosion-inhibiting coating. ACS nano, 6(2), pp. 1102-1108. doi.org/10.1021/nn203507y
Roberto Ruiz Hernández, A., Gutierrez Cruz, A., & Campos-Delgado, J. (2023). Chemical Vapor Deposition Synthesis of Graphene on Copper Foils. IntechOpen. doi.org/10.5772/intechopen.106058
The Sixth Element. (2016). Graphene in Heavy-Duty Anticorrosion of Ocean. [Online]. The Sixth Element (Changzhou) Materials Technology Co. Ltd. Available from: https://www.c6th.com/news/graphene-in-heavy-duty-anti-corrosion-of-ocean-1747777.html
Topsakal, M., Şahin, H., & Ciraci, S. (2012). Graphene coatings: An Efficient Protection from Oxidation. Physical Review B, 85(15), 155445. https://doi.org/10.1103/PhysRevB.85.155445
Disclaimer: The views expressed here are those of the author expressed in their private capacity and do not necessarily represent the views of AZoM.com Limited T/A AZoNetwork the owner and operator of this website. This disclaimer forms part of the Terms and conditions of use of this website.