In this article, we delve into the synthesis of 2D material-based polymers, specifically in situ polymerization, solution blending, and electrospinning methods, examining their respective pros and cons, aiming to provide insights into selecting the most suitable synthesis method for specific applications within nanotechnology.
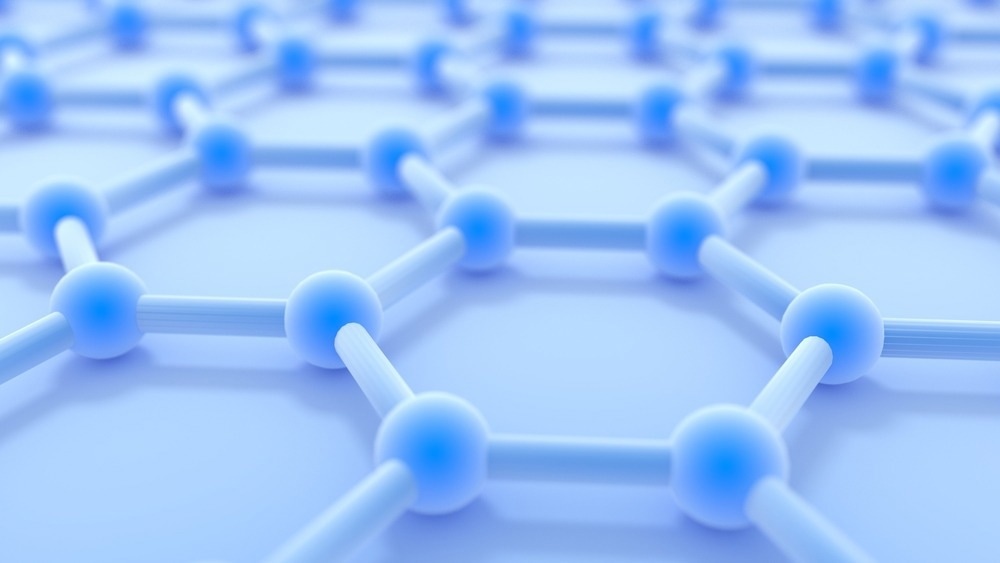
Image Credit: James A Isbel/Shutterstock.com
Two-dimensional (2D) polymers, a new class of materials, display a covalently linked sheet-like structure. They offer a range of fascinating characteristics, such as substantial specific surface area, minimal density, flexible control over size and composition, and exceptional adaptability. Consequently, these materials have applications in energy conversion and storage, nanotechnology, and biotechnology.1
Synthesis of 2D Material Polymers
The synthesis of 2D material polymers represents a groundbreaking approach in materials science, offering a diverse range of applications in various industries. These composite materials combine the extraordinary properties of 2D materials, such as graphene or transition metal dichalcogenides, with the versatility of polymers.1,2
The three prominent methods used to synthesize 2D material polymers have been explored here, and a comparative analysis of their respective advantages and disadvantages is provided.
1: In Situ Polymerization
In situ polymerization involves directly synthesizing polymers within the matrix of 2D materials. This method is achieved by dispersing 2D materials in a monomer solution and subsequently initiating polymerization. The reaction occurs in close proximity to the 2D material, leading to strong interfacial interactions and enabling a wide range of applications in areas like nanoelectronics, sensors, and nanocomposites.2,3
Step-by-step methods for in situ polymerization:
- The first step is to choose the appropriate 2D material as the matrix. Common choices include graphene, graphene oxide, transition metal dichalcogenides (e.g., MoS2, WS2), and phosphorene.
- Select a suitable monomer or a mixture of monomers that can undergo polymerization. The choice of monomers depends on the desired properties of the resulting composite material.
- Initiate the polymerization process within or on the surface of the 2D material. This can be achieved through various methods, including chemical initiators, thermal initiation, or photo-initiation.
- The selected monomers undergo chemical reactions to form polymer chains. These polymer chains grow and attach themselves to the 2D material, either through covalent bonding, non-covalent interactions, or physical entanglement, depending on the specific chemistry involved.
- The reaction conditions, including temperature, reaction time, and the concentration of monomers and initiators, are carefully controlled to achieve the desired polymerization degree and the distribution of polymer chains on the 2D material.
Pros:
The incorporation of 2D materials into polymer matrices offers several key advantages. Firstly, it establishes strong interfacial bonding between the 2D material and the polymer, leading to enhanced mechanical properties and efficient load transfer within the composite. Secondly, this method ensures the homogeneous dispersion of 2D materials throughout the polymer, preventing clumping or agglomeration and maximizing their reinforcing capabilities. These advantages collectively make integrating 2D materials into polymer matrices a versatile and powerful approach in materials science.2,3
Cons:
While the integration of 2D materials into polymer matrices offers significant benefits, it comes with its own set of challenges. Firstly, achieving precise control over the reaction conditions and polymerization kinetics can be complex, requiring careful monitoring and adjustment to attain the desired properties. Also, the method's applicability can be limited by compatibility issues, as not all types of polymers or 2D materials may interact favorably, necessitating careful consideration of material choices.2
2: Solution Blending
This approach involves dissolving the polymer precursors in a solvent, typically followed by the removal of the solvent to form the desired 2D polymer structure. This method relies on physical mixing rather than chemical reactions.3
Steps in solution blending synthesis methods:
- Choose the appropriate polymer precursors that can undergo polymerization to form a 2D structure. These precursors should be soluble in a common solvent.
- Select a suitable solvent in which the polymer precursors can dissolve. The choice of solvent depends on the nature of the precursors and the desired reaction conditions.
- Combine the polymer precursors and solvent in a container and stir or agitate the mixture. This allows the precursors to dissolve and form a homogeneous solution.
- Initiate the polymerization reaction by introducing a suitable initiator or catalyst into the solution. The choice of initiator depends on the specific polymerization mechanism, which can be radical, cationic, anionic, or other types.
- Maintain precise control over reaction conditions, including temperature, time, and concentration of reactants, to achieve the desired degree of polymerization and control over the 2D structure's size and properties.
- After the polymerization reaction has occurred, the solvent needs to be removed. This can be achieved through various methods, such as evaporation, filtration, or precipitation.
Pros:
Solution blending boasts ease of implementation, as it does not involve intricate chemical reactions, making it accessible to a broader range of researchers. Its versatility shines through, as it can be applied to various polymers and 2D materials, allowing for flexibility in material selection. Lastly, solution blending is scalable, making it suitable for both laboratory-scale research and large-scale production, offering practicality across a spectrum of applications.1,3
Cons:
It often leads to limited interfacial bonding between the 2D material and the polymer matrix since it lacks the formation of covalent bonds, potentially resulting in weaker interfacial interactions within the composite. Compared to techniques like in situ polymerization, solution blending provides less precise control over the material's properties, making it essential to weigh these trade-offs when considering this method for specific applications.3
3: Electrospinning
Electrospinning is a versatile method for making 2D polymer materials, specifically ultrafine polymer fibers. Here, a polymer solution is prepared, and then an electric field is applied, creating a charged droplet that forms into a thin jet. The solvent evaporates as the jet travels toward a collector, causing the polymer chains to solidify into nanofibers. These fibers can be collected randomly or aligned.4
Pros:
It results in nanofibers with a high surface area. When 2D materials are incorporated, this surface area can be further enhanced, rendering the material well-suited for applications like sensors and filtration, where increased surface area is beneficial. The electrospinning process allows for precise control over the morphology of the resulting material, including fiber diameter, orientation, and porosity, providing a valuable degree of customization to meet specific application requirements.4
Cons:
It involves a somewhat complex process that requires specialized equipment and expertise, making it less accessible for some researchers. It is most effective when producing nanofiber structures, which may limit its applicability to applications specifically requiring nanofibers. Therefore, while it offers distinct advantages, its suitability should be considered in light of these constraints and requirements of the desired end product.4
In conclusion, the choice of synthesis method for 2D material polymers depends on specific application requirements and material compatibility. In situ polymerization offers strong interfacial bonding but requires precise control. Solution blending is versatile but may result in weaker interactions. Electrospinning is suitable for nanofiber-based applications but demands specialized equipment. Researcher must carefully consider these pros and cons to select the most suitable method for their intended application.
References and Further Reading
Li, Z. & Lin, Z. Two-Dimensional Polymers: Synthesis and Applications. ACS Appl. Mater. Interfaces 13, 45130–45138 (2021).
Stupp, S. I., Son, S., Lin, H. C. & Li, L. S. Synthesis of two-dimensional polymers. Science (80-. ). 259, 59–63 (1993).
Zhang, N. & Wang, T. Synthesis methods of organic two-dimensional materials. J. Polym. Sci. 58, 3387–3401 (2020).
Kailasa, S. et al. Electrospun Nanofibers: Materials, Synthesis Parameters, and Their Role in Sensing Applications. Macromol. Mater. Eng. 306, 2100410 (2021).
Disclaimer: The views expressed here are those of the author expressed in their private capacity and do not necessarily represent the views of AZoM.com Limited T/A AZoNetwork the owner and operator of this website. This disclaimer forms part of the Terms and conditions of use of this website.