Heat treatment improves the mechanical and barrier characteristics of materials like nanocomposites. This article focuses on an analysis of the effect of heat treatment on chitosan nanocomposites.
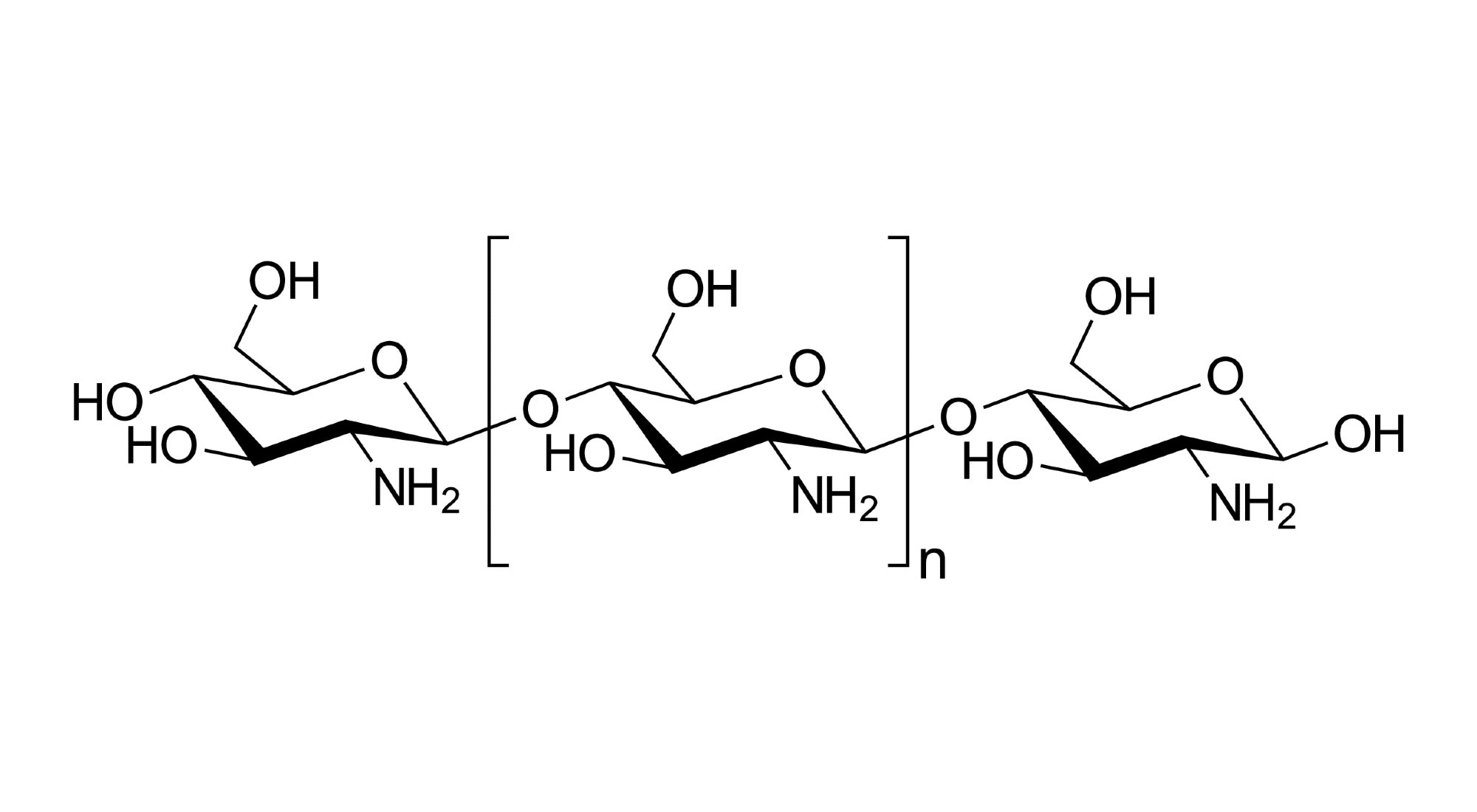
Image Credit: magr80/Shutterstock.com
Introduction
Polysaccharides, such as chitosan, exhibit poor mechanical and barrier characteristics in their current form. Consequently, compared to common plastic films, using materials based on biopolymers in industry has not been as widespread.
Combining chitosan with nanoparticles to produce chitosan nanocomposites is one of the most prevalent methods to overcome this problem. In addition to these nano-fillers, ferulic, tannic, and citric acids can cross-link chitosan and enhance its properties. However, there is a limit to the number of chemicals that can be applied before unfavorable aggregation effects emerge.
Heat treatment has been used to circumvent the aforementioned constraints. Kim et al. and Liu et al. have shown that subjecting materials to elevated temperatures improved their mechanical and barrier properties.
Chitosan Nanocomposites - Properties and Applications
The properties of biomimetics, biocompatibility, and biodegradability are connected to the diverse applications of chitosan. This has fueled recent interest in chitosan nanocomposites and other materials.
Food preservation, healthcare, and environmental monitoring are a few of the industries that find chitosan nanocomposites desirable. In tissue engineering, it is a suitable biomaterial to create extracellular tissue matrixes. It can also be used in targeted cancer therapy and for treating wounds.
Unlike chitin, these nanocomposites dissolve easily in acidic environments. The attributes of chitosan, including its physico-chemical and biological properties, are determined by the percentage content of acetyl-glucosamine and glucosamine moieties.
They function as analgesics, antibiotics, antifungals, and hemostatics. Furthermore, the mucoadhesive properties of the nanocomposites are influenced by the degree of deacetylation (DD). It exhibits strong electrostatic characteristics and readily interacts with negatively charged surfaces. Therefore, it shows suitable bioadhesive properties.
It can also be employed as a drug delivery vehicle and a carrier for various therapeutic compounds such as drugs, genes, and proteins.
Micro air vehicles (MAVs) made of chitosan nanocomposite have recently attracted attention because of its potential use in a variety of fields, including environmental monitoring, surveillance, rescue operations, and even military applications that call for small, maneuverable drones.
Heat Treatment and Nanocomposites
Heat treatment is important in modifying the microstructure and properties of nanocomposites to suit the intended applications (as previously stated). It entails exposing the material to high temperatures for a predetermined amount of time, which changes the material's physical, mechanical, and chemical properties, such as in nanocomposites.
It breaks down the hydrogen bonds that connect polymer chains. This encourages a more open structure, which enables intra- and intermolecular cross-linking. It can result in an improvement in the nanocomposites' microhardness and ultimate tensile strength. As a result, mechanical attributes are improved.
It is capable of altering the crystalline structure by promoting a rise in the recrystallization of a grain, for example, nickel. It also enhances the homogeneity of nanocomposites, resulting in the homogeneous distribution of nano-fillers in the composite.
Heat treatment can considerably reduce moisture content by either causing moisture evaporation or sublimation at elevated temperatures or increasing cross-linking between molecules within the composite, such as chitosan-based nanocomposites or films, making the material less permeable to moisture. Its improved biodegradability and barrier characteristics make it beneficial in food packaging and other applications.
The stress brought on by the physical fabrication processes used to create nanomaterials, including ball milling, can be significantly reduced by heat-treating nanocomposite. This may help avoid premature failure. Additionally, it plays a significant role in improving the hydrothermally treated nanocomposites' photodegradation performance and thermal stability.
Recent Research on Chitosan Nanocomposites and Heat Treatment
Studies show that, in addition to filler materials (e.g., nanocrystalline cellulose, nanoparticles), the properties of chitosan nanocomposite can be modified with heat treatment to promote stress relief, prevent degradation, improve thermal stability, and tensile strength, allowing it to be used in a variety of applications.
Rubentheren et al. investigated the effect of heat treatment on chitosan nanocomposites. These heat-treated chitosan nanocomposites can be exploited as wing membranes to make biomimetic micro-air vehicles (BMAV) that closely mimic those of dragonflies. This comes as a result of chitosan's excellent film-forming abilities, which make it ideal for membrane applications.
The materials used by the researchers were chitosan film, chitosan/NCC nanocomposite, chitosan film cross-linked with tannic acid, and chitosan/NCC cross-linked with tannic acid. In a convection oven, all samples underwent a 30-minute heat treatment at 180 °C.
X-ray diffraction (XRD) and Fourier transform infrared spectroscopy (FTIR) revealed alterations in the chemical interaction of heat-treated films and the molecular structure of chitosan. Heat-treated films also demonstrated significant enhancements in moisture absorption.
Heat treatment increases tensile strength and Young' Modulus while significantly decreasing % elongation-at-break.
In this investigation, heat treatment of the chitosan nanocomposites improved their tensile strength and Young's modulus by up to 7 MPa and 259 MPa, respectively. These developments suggested that chitosan has been heat-treated and has a lot of potential for BMAV wing membranes.
In a different study, solution-casting was used to create alpha-Chitin whisker-reinforced chitosan nanocomposite films, which were then heated by saturated steam in an autoclave at 110 °C for 5–10 minutes (min). The heat-treated films were examined using a transmission electron microscope (TEM), a thermogravimetric analyzer (TGA), and other tools.
Sriupayo et al., reported that alpha-chitin whisker reinforced chitosan films had a higher tensile strength than pure chitosan films. The films' color changed from being transparent before heat treatment to pale yellow after 5 minutes, then to yellowish brown after 10 minutes.
The inclusion of a-chitin whiskers and heat treatment both improved the water resistance of the nanocomposite films, resulting in a lower percentage of weight loss and degree of swelling. The decreased affinity for water makes the chitosan/alpha-chitin whiskers nanocomposite films more stable when utilized in an aquatic environment.
Future Outlook
Heat-treated nanocomposites with chitosan as a matrix were introduced and addressed in this article with respect to their chemical makeup, shaping procedures, characteristics, and applications.
Heat treatment can be added to modify and improve the mechanical and barrier properties of chitosan nanocomposite. Recent studies reveal that heat-treated chitosan nanocomposites have much better mechanical strength and less water content.
This is because the structure was compacted by rapid cross-linking. In conclusion, heat-treated chitosan nanocomposites have a lot of potential for biomedical, wastewater treatment, food packaging, and energy storage applications.
References and Further Reading
Khanzada, B., et al. (2023). Chitosan based bio-nanocomposites packaging films with unique mechanical and barrier properties. Food Packaging and Shelf Life, 35, p. 101016, doi.org/10.1016/J.FPSL.2022.101016.
Silva, A.O., et al. (2021). Chitosan as a matrix of nanocomposites: A review on nanostructures, processes, properties, and applications. Carbohydrate Polymers, 272, p. 118472, doi.org/10.1016/J.CARBPOL.2021.118472.
Murugesan, S. & Scheibel, T. (2021). Chitosan‐based nanocomposites for medical applications. Journal of Polymer Science, 59(15), pp.1610–1642, doi.org/10.1002/POL.20210251.
Sriupayo, J., et al. (2005). Preparation and characterization of α-chitin whisker-reinforced chitosan nanocomposite films with or without heat treatment. Carbohydrate Polymers, 62(2), pp. 130–136, doi.org/10.1016/J.CARBPOL.2005.07.013.
Viyapuri, R., et al. (2016). Effects of heat treatment on chitosan nanocomposite film reinforced with nanocrystalline cellulose and tannic acid. Carbohydrate Polymers, 140, pp. 202–208, doi.org/10.1016/J.CARBPOL.2015.12.068.
Disclaimer: The views expressed here are those of the author expressed in their private capacity and do not necessarily represent the views of AZoM.com Limited T/A AZoNetwork the owner and operator of this website. This disclaimer forms part of the Terms and conditions of use of this website.