Learn about the different methods and techniques used to achieve controlled carbon nanotube fabrication, as well as the factors limiting their production.
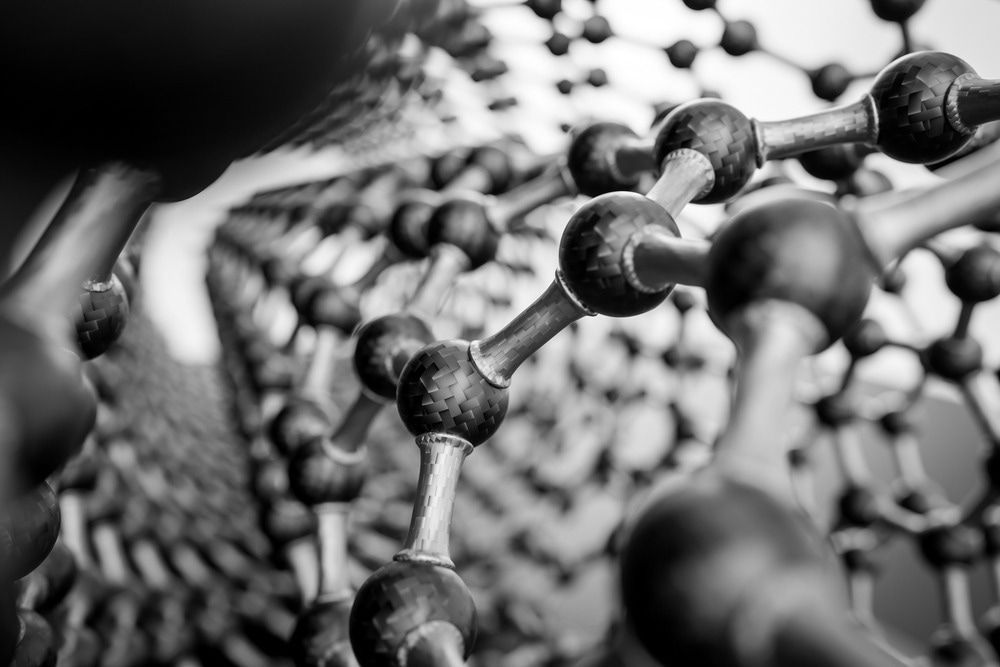
Image Credit: Forance/Shutterstock.com
Structural Features and Properties of CNTs
Carbon nanotubes (CNTs) are one-dimensional, nanoscale, hollow, tubular structures that are composed of carbon atoms. These carbonaceous nanostructures were formally named by Sumio Iijima in 1991, after studying a soot-like product, derived from graphite, under a transmission electron microscope.1
CNTs are developed by concentric rolling of graphene sheets. Besides covalent bonding between adjacent carbon atoms and tubular structural features, CNTs have many unique physical and chemical properties. For instance, these exhibit ultra-high strength and modulus, desirable chemical stability, very good electrical and thermal conductivity, and exceptional optical properties.
Based on the number of graphene layers, CNTs are classified as single-wall CNTs (SWCNTs), double-wall CNTs (DWCNTs), or multi-wall CNTs (MWCNTs). In SWCNTs, the carbon molecules are present in sp2 hybridization and represent a hexagonal honeycomb structure. However, MWCNTs comprise multiple concentric tubes encircling one another.
SWCNT and MWCNT comprise different chiralities, such as zig-zag, armchair, and chiral, influencing their structural features, properties, and applications. The armchair chirality shares similar characteristics with metals, while chiral and zig-zag chiralities have properties that are identical to semiconductors. Both chiral angle and diameter play critical roles in different CNT properties.2
General Applications of CNTs
CNTs are extensively applied in biomedical research due to their ultra-lightweight, biocompatibility, fast electron transfer kinetics, chemically inert property, antimicrobial activity, high tensile strength, and presence of exposed functional groups. In addition, they contain semi and metallic conductive properties, making them suitable sensor candidates. These biosensors are used for clinical diagnostics, environmental monitoring, and food safety. CNTs are also used to deliver drugs to targeted organs.3
CNTs are applied in textiles, microelectronics, thermal management of electronic circuits, electron guns, and transistors. These nanoparticles are also added to cement-based materials to enhance their durability, mechanical properties, and compatibility with the matrix.4
Different Methods to Produce CNTs
Different methods are used to synthesize CNTs, such as laser ablation, arc discharge, the sol–gel process, and chemical vapor deposition (CVD). In the arc discharge technique, direct current is introduced through graphite electrodes in the presence of an inert Agron at low pressure.
Although the main principle of laser ablation is quite similar to arc discharge, the former uses a pulsed laser as a heat source. A high level of carbon vapor is released from graphite in the laser ablation method, and a flowing gas is used to remove Argon and the carbon vapor.
CVD is the most commonly used technique to produce CNTs. This method utilizes hydrocarbons as precursors in the presence of metal catalysts at varying temperatures of 500 - 1000°C.
At this temperature, the hydrocarbons are decomposed to produce CNTs. Some of the common CVD methods used to synthesize CNTs are hot-wire (HWCVD), microwave plasma-enhanced (MWCVD), microwave plasma-enhanced (MWCVD), hot-filament (HFCVD), liquid-injection (LICVD), and aerosol-assisted (ACVD).
Several advantages and limitations are associated with each of these methods, i.e., laser ablation, arc discharge, and CVD. For instance, the major advantages of the arc discharge method are its simplistic approach and the production of excellent SWCNT crystallinity. However, one of the key disadvantages of this method is low purity. The laser ablation method requires expensive facilities and produces limited CNTs. In contrast, CVD is the most widely used method because of its high yield and good controllability.5
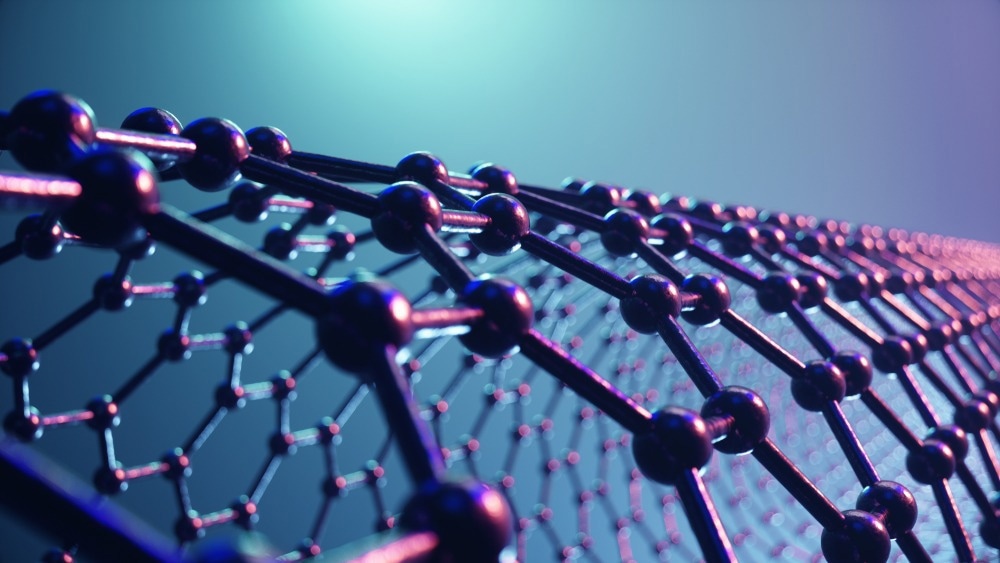
Image Credit: Rost/Shutterstock.com
Factors Associated with Controlled Fabrication of CNTs
Recently, scientists have focussed on the controlled synthesis of SWCNTs and explored their application. Compared to MWCNTs, SWCNTs have particularly drawn attention due to their small diameter, superior properties, and perfect C-C bonding. It is difficult to synthesize SWCNTs uniformly or in a pre-defined structure. To rectify this shortcoming, scientists used novel catalysts and formulated new methodologies for controlled SWCNT fabrication.6
Different growth parameters are modified by adding novel catalysts or reactive etchants to attain the desired diameter and transport properties of CNTs. The diameter of SWCNTs ranges between 0.4 nm to several nanometers. Since the diameter of SWCNTs considerably influences the band-gap and chirality, it is important to produce SWCNTs with uniform and controllable diameters for optimal functional outcomes.
A floating catalyst CVD (FCCVD) method has been recently developed to synthesize uniform CNTs with controlled diameters. This method utilizes ferrocene as a catalyst precursor, hydrogen as a carrier gas, and hydrocarbons as the carbon source. This method exhibited great efficiency in producing high-quality CNTs with good controllability on their structure and texture. In addition, this is a cost-effective approach.7
In CVD methods, temperature, ferrocene volatilization rate, and hydrogen/hydrocarbon ratio affect the growth of CNTs. High-quality SWCNTs with controlled diameters can be fabricated with a proper modification of these parameters.
A new FCCVD method has been developed for the one-step fabrication of aligned CNT bundles. This method required a gas rectifier, also known as a honeycomb ceramic filter. This filter has one-dimensional liner channels to control the Reynolds number of a gaseous medium containing a growing CNT aerogel. The gas rectification effect involved in this approach has considerably improved CNT structure and alignment.8
CNTs are grown on multiple substrates like fused quartz, copper, highly oriented pyrolytic graphite, and mica. The substrates and catalysts are placed inside the CVD reactor. The reaction temperature is adjusted to allow the growth of nanotubes. Subsequently, the furnace is cooled to 300°C before exposing CNTs to air. In addition to temperature, gas type and flow rate influence the length and diameter of the fabricated CNTs.
The grain size of the substrate and catalyst metal play an important role in obtaining the desired physiochemical properties of the CNTs. The uniformity of sensors developed using CNTs depends on the grain size and shape.9
Challenges and Innovations in Controlled CNT Fabrication
Compared to other carbon-based nanomaterials, such as graphene, CNTs have greater structural defects. Controlled growth of SWCNTs with precise chiral angle, diameter, and transport properties is extremely important for nanoelectronics and nano-optoelectronics. This is a challenging task because a narrow structural difference in SWCNTs could influence their property.
Some techniques used to overcome this challenge include selective etching, catalyst engineering, and post-synthesis separation.
Scientists are continuously performing systematic research to better understand the growth mechanisms of SWCNTs. Innovative catalytic strategies are continually formulated for the controlled synthesis of SWCNTs. The emerging non-metal catalysts have enabled desirable CNT production with specific diameters and chiralities, even at a high temperature.10
References and Further Reading
Goldmann E, Górski M, and Klemczak B. Recent Advancements in Carbon Nano-Infused Cementitious Composites. Materials. 2021; 14(18). https://doi.org/10.3390/ma14185176
Mohd Nurazzi N. et al. Fabrication, Functionalization, and Application of Carbon Nanotube-Reinforced Polymer Composite: An Overview. Polymers. 2021;13(7), 1047. https://doi.org/10.3390/polym13071047
Anzar N, Hasan R, Tyagi M, Yadav N, and Narang J. Carbon nanotube - A review on Synthesis, Properties and plethora of applications in the field of biomedical science. Sensors International.2020; 1, 100003. https://doi.org/10.1016/j.sintl.2020.100003
Cui K, Chang J, Feo L, Chow CL, and Lau D. Developments and Applications of Carbon Nanotube Reinforced Cement-Based Composites as Functional Building Materials. Frontiers in Materials. 2022; 9, 861646. https://doi.org/10.3389/fmats.2022.861646
Mubarak N, Abdullah E, Jayakumar N, and Sahu J. An overview on methods for the production of carbon nanotubes. J. Ind. Eng. Chem.2014; 20(4), 1186-1197. https://doi.org/10.1016/j.jiec.2013.09.001
Zhang Z. et al. Controlled synthesis of single-walled carbon nanotubes by floating catalyst CVD for transparent conducting films: A critical role of loops. DRM. 2022; 124, 108942. https://doi.org/10.1016/j.diamond.2022.108942
Fujimori T. et al. One step fabrication of aligned carbon nanotubes using gas rectifier. Sci. Rep. 2022; 12(1), 1-9. https://doi.org/10.1038/s41598-022-05297-6
Tsentalovich DE. et al. Influence of carbon nanotube characteristics on macroscopic fiber properties. ACS Appl. Mater. Interfaces.2017; 9, 36189–36198.
Nag A and Mukhopadhyay SC. Fabrication and implementation of carbon nanotubes for piezoresistive-sensing applications: A review. J. Sci-Adv. Mater. Dev.2022; 7(1), 100416. https://doi.org/10.1016/j.jsamd.2021.100416
Liu C and Cheng H. Carbon nanotubes: Controlled growth and application. Mater. Today. 2013; 16(1-2), 19-28. https://doi.org/10.1016/j.mattod.2013.01.019
Disclaimer: The views expressed here are those of the author expressed in their private capacity and do not necessarily represent the views of AZoM.com Limited T/A AZoNetwork the owner and operator of this website. This disclaimer forms part of the Terms and conditions of use of this website.