In a study published recently in the journal Materials, polylactic acid (PLA) and polycaprolactone (PCL) were combined with various graphene nanoplatelet compositions (GNP), where wettability, morphology, rheology, thermoelectric, structural, and electrically characteristics of the 3D-printed materials were studied.
Study: Fabrication of PLA/PCL/Graphene Nanoplatelet (GNP) Electrically Conductive Circuit Using the Fused Filament Fabrication (FFF) 3D Printing Technique. Image Credit: Alex_Traksel/Shutterstock.com
Uses of Plastics
Plastics are increasingly used in a variety of applications. However, due to the increased need for sustainable products with eco-friendly properties, natural polymers have lately gained much attention.
One of the causes for the replacement of synthetic polymeric products is the spread of non-biodegradable plastic garbage in seas and marine habitats, as well as the risk to human and aquatic life which has become a serious issue.
Biorenewable sources may now be utilized to substitute regularly used oil-based materials in producing biopolymers, which are frequently recyclable through ecologically benign bioreactors.
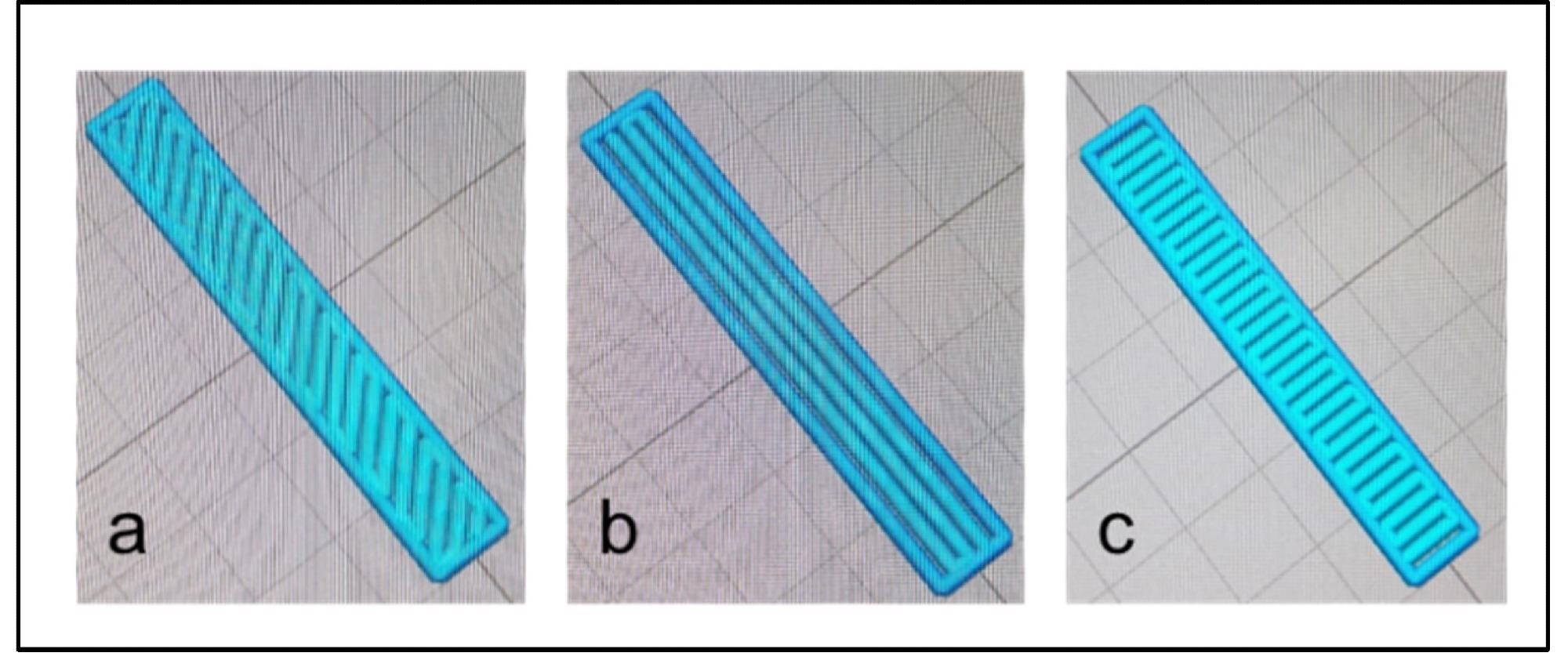
Figure 1. The different 3D printing patterns according to the three different raster angles: (a) +45°/−45°, (b) 0°, and (c) 90°. © Masarra, N.-A. et al. (2022).
What is PLA
Polylactic acid (PLA) is a biocomposite and is a recyclable, nontoxic, and compostable aromatic polymeric polymer. It has significant mechanical qualities, such as an elastic modulus in the 3–4 GPa area and compressive strength in the 60–70 MPa region.
Polylactic acid does possess certain drawbacks, such as an absence of flexibility; nevertheless, combining it with other elastomeric plastics, such as polycaprolactone (PCL), may increase its hardness. Moreover, since the structural and tribological characteristics of the two polymers vary, their mixing may provide a material with well-balanced capabilities.
Because of its cheap cost, simplicity of use, compactness, and ability to produce multipurpose items, the fused filament fabrication (FFF) technology is an intriguing 3D printing approach.
Polylactic acid is the most often used material among FFFconsumers. Furthermore, FFF is a potential technology for the manufacture of carbon materials products, and the creation of novel conducting polymeric composites utilizing this process is desirable.
Methodology Used
This study was the first to describe the creation of conductive PLA/PCL/GNP 3D-printed materials capable of connecting an electrical circuit.
Polylactic acid and polycaprolactone were combined with GNP and projected as strands that use the melting mixing process.
Ultimately, the threads were 3D printed using the FFF method.
In parallel to the microhardness examination, the synthesized 3D-printed specimens were exposed to contacting degree assessment, wettability, heat, physical, and electric impedance testing. In order to investigate the possible impacts of the printing technique on the morphology and electrical characteristics of the nanocomposite, injection-molded specimens were made for reference.
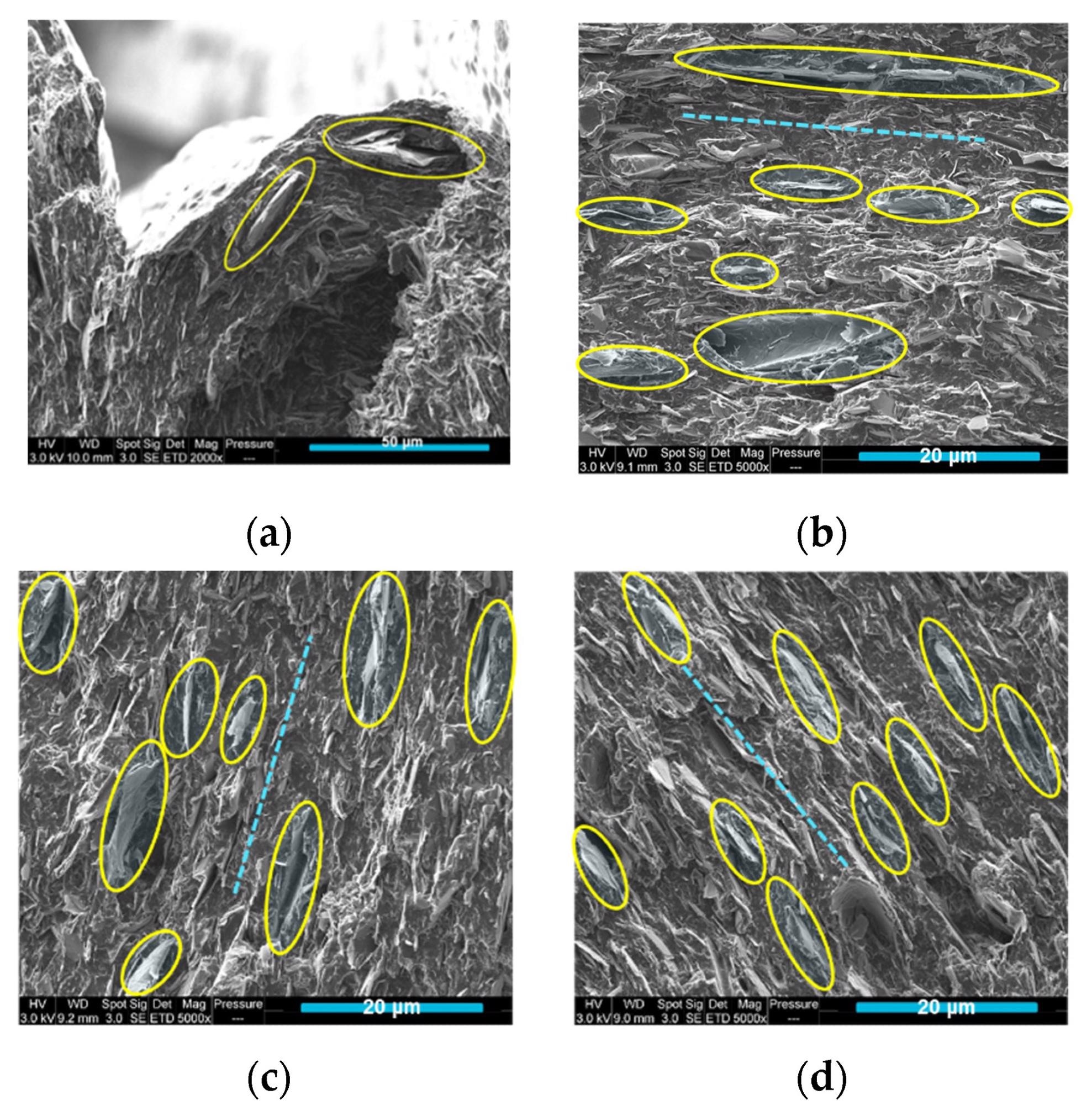
Figure 2. (a) SEM image of 3D-printed PLA/PCL/15 wt% M5; (b–d) SEM images of injection-moulded PLA/PCL/15 wt.% M5 composite (The yellow ellipses are surround some graphene flakes and the dotted lines indicate the similar orientation of the graphene platelets in the injection moulded samples). © Masarra, N.-A. et al. (2022).
Significance of Present Research
This work demonstrated the production of semi-conductive PLA/PCL/GNP materials utilizing the FFF approach for the first time.
The microstructural investigation revealed that M5 graphene nanoplatelet compositions were preferentially localized in polycaprolactone instead of Polylactic acid; this was attributed to PCL's lesser density and thermal properties, which facilitated graphite placement during ejection.
This was contrary to the permeability forecast, indicating that the kinematic variables triumphed over the meteorological considerations in this situation.
GNP/PCL clusters were larger in size than plain polycaprolactone implants. The temperature tests revealed that no improvement in temperature durability was achieved in the vicinity of graphite, which may be attributed to the clumping of these nanomaterials in the epoxy resin.
The DSC experiments indicated that the proportion of crystallization of polylactic acid rose somewhat in the vicinity of polycaprolactone and as the amount of graphite improved.
Research Findings and Conclusion
Impedance measurements that use the four-probe technique revealed that thermoformed nanocomposites 15%, 20%, and 25% graphite were electrical isolators, but 3D-printed nanocomposites were the same proportions of graphite were semi-conductors.
The 20 wt.% and 25 wt.% 3D-printed specimens, in particular, were ready to connect wiring. The explanation for these discrepancies was due to microstructural changes in both kinds of specimens induced by the procedure.
The syringe specimens did not have a sufficient amount of filler particles on their interface, but the 3D-printed specimens had graphite particles on the exterior of the produced threads, whose orientation matched the production pattern.
The existence of a hump in storing elasticity graphs in the low-frequency area indicated the construction of a viscoelastic penetrable system, which requires less graphite than an electronic penetrable channel.
The Young's modulus findings agreed with the electrical data and increasing the graphite proportion resulted in improvements in this characteristic, but a flattening off occurred at 15 wt. % of graphene nanoplatelet compositions.
However, as the proportion of graphene increased, causing the assemblages to induce the composites' ductility to reduce.
It is also worth noting that the vector orientation affected the electrical resistivity findings, with specimens imprinted in the longitudinal axis performing the best in terms of conductance.
Continue reading: What Nanoparticles are Best for Additive Manufacturing and 3D Printing Applications?
Reference
Masarra, N.-A. et al. (2022). Fabrication of PLA/PCL/Graphene Nanoplatelet (GNP) Electrically Conductive Circuit Using the Fused Filament Printing Technique. materials. Available at: https://www.mdpi.com/1996-1944/15/3/762
Disclaimer: The views expressed here are those of the author expressed in their private capacity and do not necessarily represent the views of AZoM.com Limited T/A AZoNetwork the owner and operator of this website. This disclaimer forms part of the Terms and conditions of use of this website.