The construction of micro/nanorobots employing helical carbon nanowire as a manufacturing material is the topic of a recent study from the journal ACS Applied Nano Materials.
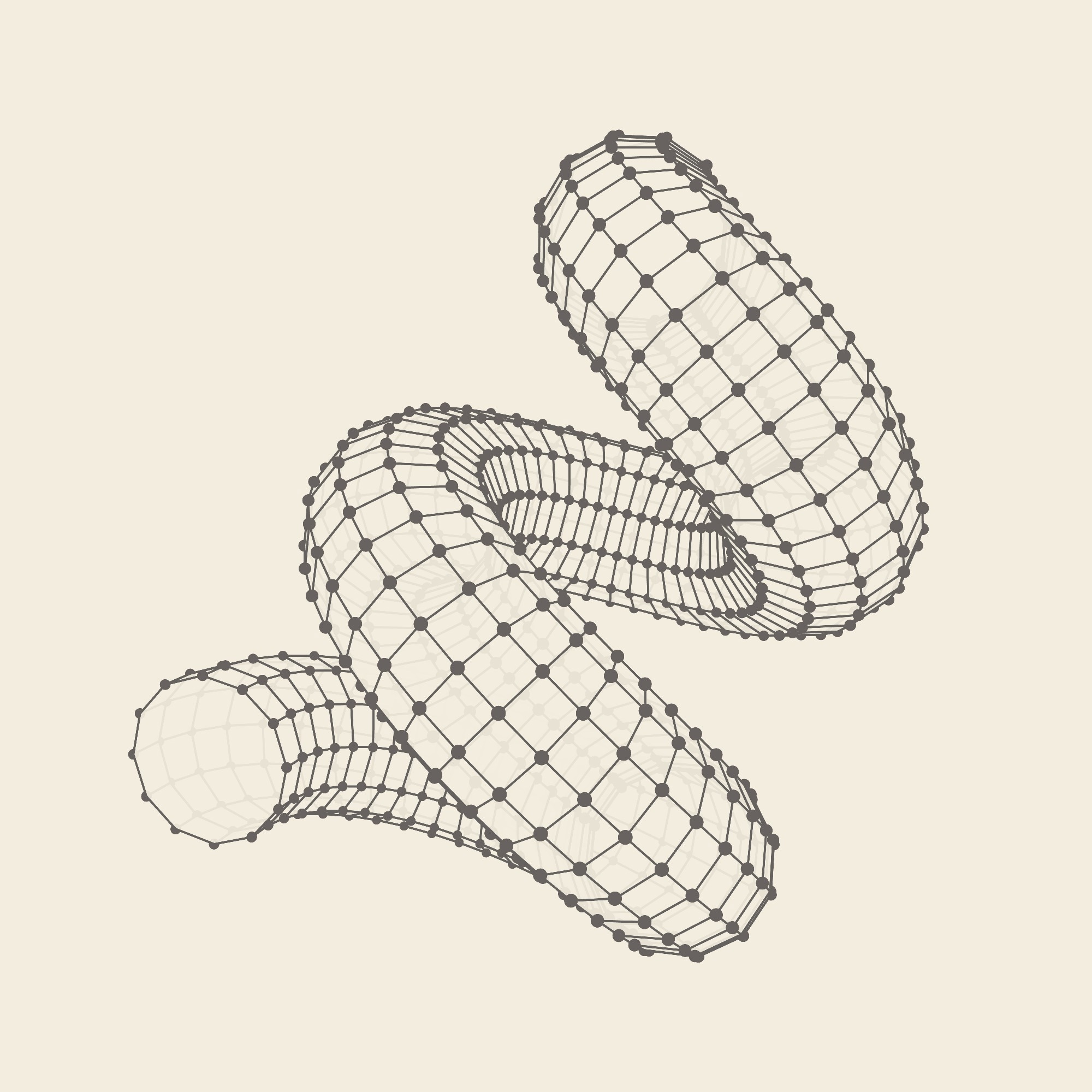
Study: Helical Carbon Nanowires for Magnetic-Field-Controlled Swimming. Image Credit: Login/Shutterstock.com
The study aims to address the important challenges of helical carbon nanowire dispersal, screening, and cutting of the suitable length and fabricate helical carbon nanowire robots (HCNRs) with unique characteristics.
Micro/Nanorobots: Overview and Important Applications
A micro/nanorobot can transform magnetic, optical, or electrical energy into kinetic energy, enabling it to "swim" in a fluid medium.
The intensity, frequency, and orientation of the induced magnetic field can be adjusted to change the direction, velocity, and spatial position of micro/nanorobots. By varying the magnetic field, various types of motion such as rotations, swings, and rolls can be produced.
Magnetic-actuated micro/nanorobots made of helical carbon nanowire are appealing due to their wireless charging, three-dimensional manipulation, and biocompatible power generation. These properties enable them to be used in biomedical fields that require high precision control, such as drug delivery systems, tissue perforation, therapeutic procedures, vascular dredging, and epithelial manipulation.
Furthermore, these robots may be employed as microtools with six degrees of freedom to handle cellular or subcellular materials. As a result, helical carbon nanowire robots (HCNRs) have significant potential in targeted illness therapy.
Traditional Fabrication Methods and Their Limitations
Micro/nano robots have traditionally been actuated by magnetic, acoustic, optical, chemical, and electrical methods. At present, micro/nanorobots controlled by applied magnetic fields can achieve complicated trajectories and navigate obstacles.
These production processes, however, are limited by the one-dimensional character of direct laser inscription and the single-monolayer formation of glancing angle. Furthermore, these approaches are often complicated and need costly equipment. As a result, designing and manufacturing micro/nanorobots at a cheap cost and in batch numbers remains a substantial difficulty.
Helical Carbon Nanowire (HCN) for Fabrication of Micro/Nanorobots
Because of their importance in drug delivery systems, functionalized carbon nanowire (HCN) materials have gained increased attention in recent years. Carbon nanowire is a one-of-a-kind material with exceptional electrical, thermal, photonic, and mechanical capabilities. Chemically processed carbon nanowire is highly biodegradable because it can be easily excreted from natural resources.
Carbon nanowire has recently discovered uses in bio-tracking, targeted medication administration, and in vivo photothermic treatment due to its extraordinary features. Furthermore, carbon nanowire enables the high-density loading of various moieties for a range of purposes such as specific-cell identification and thermal monitoring.
The advancement of nanotechnology now enables the low-cost and high-yield manufacturing of helical carbon nanowire (HCN) materials by chemical vapor deposition (CVD). By adjusting the growth period or catalyst concentration in CVD, the length of the helical carbon nanowire can be modified.
In this study, the researchers created a helical carbon nanowire robot (HCNR) using a simple synthesis process. The study's objective was to create smaller micro/nanorobots and operate them with great precision via economic batch manufacturing. The mobility of the helical carbon nanowire robot and its capacity to transfer things were validated during the experiment using an applied magnetic field.
Key Developments
The as-prepared helical carbon nanowire robot not only has excellent mechanical qualities but also moves precisely and efficiently in response to an applied magnetic flux in a low-Reynolds-number fluid.
When subjected to a static magnetic field and a revolving magnetic field, the helical carbon nanowire robot rotates, and when exposed simply to a rotating magnetic field, it rolls. The helical carbon nanowire robot can be led through complicated paths with a precision of fewer than 5 micrometers during the rolling mode.
The findings show that the maximal translational velocity in rotational motion is affected by the length of the helical carbon nanowire robot and the frequency of the rotating magnetic force. The magnetic induction intensity influences the maximum translational velocity by influencing the step-out frequency.
The findings demonstrate that a helical carbon nanowire robot can grab, carry, and release tiny particles. As a result, these innovative micro/nanorobots can capture particles and subsequently transfer them to the desired location. The findings also imply that the helical carbon nanowire robot developed in this study can be employed for cell-level operations in biomedical sectors.
Reference
Bai, X. et al. (2022). Helical Carbon Nanowires for Magnetic-Field-Controlled Swimming. ACS Applied Nano Materials. Available at: https://pubs.acs.org/doi/10.1021/acsanm.2c02325
Disclaimer: The views expressed here are those of the author expressed in their private capacity and do not necessarily represent the views of AZoM.com Limited T/A AZoNetwork the owner and operator of this website. This disclaimer forms part of the Terms and conditions of use of this website.