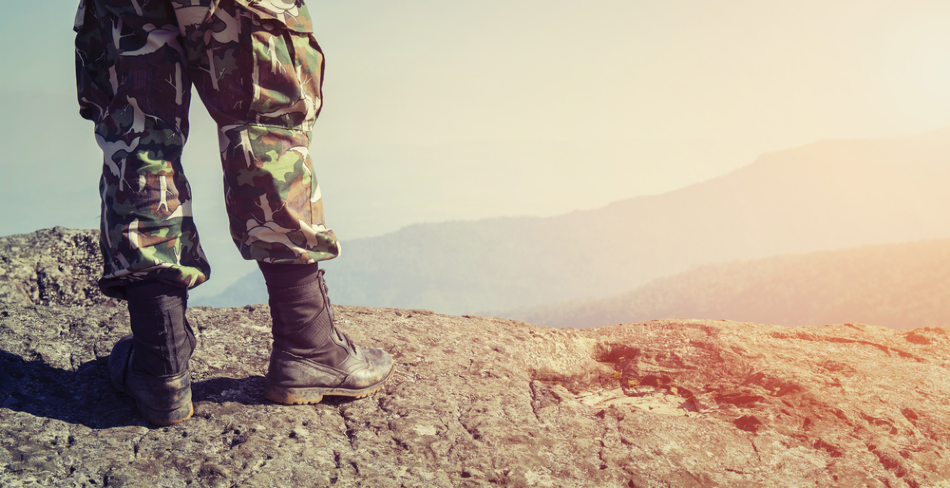
Image Credit: crazystocker/Shutterstock.com
According to a recent study, new nanofiber technology from Harvard University and the US Army could help protect against both the extreme impact of bullets and the intense heat of explosions – possibly leading to the creation of next-generation body armor. This body armor would be useful on the battlefield, but it could also be used to protect in other extreme conditions, such as the harsh conditions found in outer space.
Developing gear to shield the body from high temperatures and lethal impacts is challenging due to a rudimentary fact: materials that can withstand ballistic impacts are poor insulators of heat. Consequently, protective battlefield equipment is made up of several layers of various materials.
Modern body armor is bulky and heavy, which can seriously limit mobility. In a combat situation, a soldier has three principal tasks to perform: communicate, move and fire a weapon. If mobility is restricted, it decreases the odds of survival and mission success.
Nanofiber Technology for Body-Shielding Applications
Through a partnership with the US Army and using nanofiber technology, Harvard researchers created a lightweight, multi-purpose material that can shield the body from both high-velocity impacts and extreme temperatures. The scientists said their material could protect astronauts, firefighters and soldiers from many different threats encountered.
To achieve their goal, the Harvard researchers examined the inherent compromise between mechanical strength and thermal protection, qualities based in a material's molecular makeup. Metals and other materials that offer robust mechanical protection have a very ordered molecular structure that tolerates and distributes impact energy. Good insulators have a chaotic structure, which does not transfer heat energy effectively. Twaron and Kevlar are products commonly used to offer impact or thermal protection based on how they are used: material fibers for impact protection and aerosol gels for thermal protection.
Using Kevlar, the Harvard team set out to blend a woven fiber structure with a porous aerogel structure. Their ultimate result was long, continual fibers with big gaps in between the fibers. In this arrangement, the protracted fibers could withstand a hard impact while the structural gaps blocked harmful heat diffusion.
The study team created its fibers using a technique called immersion Rotary Jet-Spinning (iRJS). In this process, a spinning device extrudes a liquid polymer through a small hole via centrifugal force. After being extruded at a high rate of speed, the polymer passes through air, where chains of polymers stretch and line up. The liquid then enters a rotating bath that causes the polymers to precipitate, creating lengthy fibers. Because the bath is spinning, the newly formed fibers follow a vortex and encircle a round collector at the bottom of the machine.
Click here to find out more about nanofiber production equipment.
The scientists were able to tune the viscosity of their polymer substrate so that the resulting fibers formed into the desired porous material sheets. To evaluate the nanofiber sheets, the Harvard group enlisted their US Army partners to conduct ballistic tests with large round projectiles.
The tests involved the novel material being sandwiched by woven sheets of Twaron. The study team said their novel system compared favorably to an all-Twaron stack of material. Regarding thermal testing, the scientists reported that their nanofibers offered 20 times the insulating capability of Twaron and Kevlar.
Although improvements must still be made to create a useful protective system, the researchers have effectively opened the door to a new type of multifunctional protective material.
Spinning Synthetic Meat
The iRJS technique used in the new study was developed at Harvard and has been in use for several years. It appears to hold significant promise for creating novel materials, including synthetic meat.
According to a 2019 study, Harvard researchers were able to use iRJS to fabricate cow and rabbit muscles on edible scaffolds so that the muscles resembled the texture and feel of real meat.
To create fake meat, the researchers fabricated food-safe gelatin fibers to be used as a scaffold. The team seeded this gelatin scaffold with cow and rabbit muscle cells, which were grown into long, slender structures that resembled natural meat.
When the scientists evaluated their products alongside natural beef and rabbit meat, they discovered that, although comparable, natural meat held a greater amount of muscle fibers, which indicated they were more “mature.”
The study team concluded that advances in stem cell technology, media formulations, edible scaffold engineering and bioreactor culture would likely be needed to make a suitable synthetic meat product.
References and Further Reading
Burrows, L. (2020) Multifunctional nanofiber protects against explosions. [Online] The Harvard Gazette. Available at: https://news.harvard.edu/gazette/story/2020/06/new-nanofiber-protects-against-extreme-temperatures-projectiles/
Burrows, L. (2019) Real texture for lab-grown meat. [Online] The Harvard Gazette. Available at: https://news.harvard.edu/gazette/story/2019/10/lab-grown-meat-gains-muscle-as-it-moves-from-petri-dish-to-dinner-plate/
MacQueen, L.A. et al. (2019) Muscle tissue engineering in fibrous gelatin: implications for meat analogs. [Online] npj Science of Food. Available at: https://www.nature.com/articles/s41538-019-0054-8
Disclaimer: The views expressed here are those of the author expressed in their private capacity and do not necessarily represent the views of AZoM.com Limited T/A AZoNetwork the owner and operator of this website. This disclaimer forms part of the Terms and conditions of use of this website.