Nanoimprint lithography (NIL) is an advanced nanofabrication technique capable of creating patterns and structures smaller than 10 nm with low cost, high throughput, and high precision.
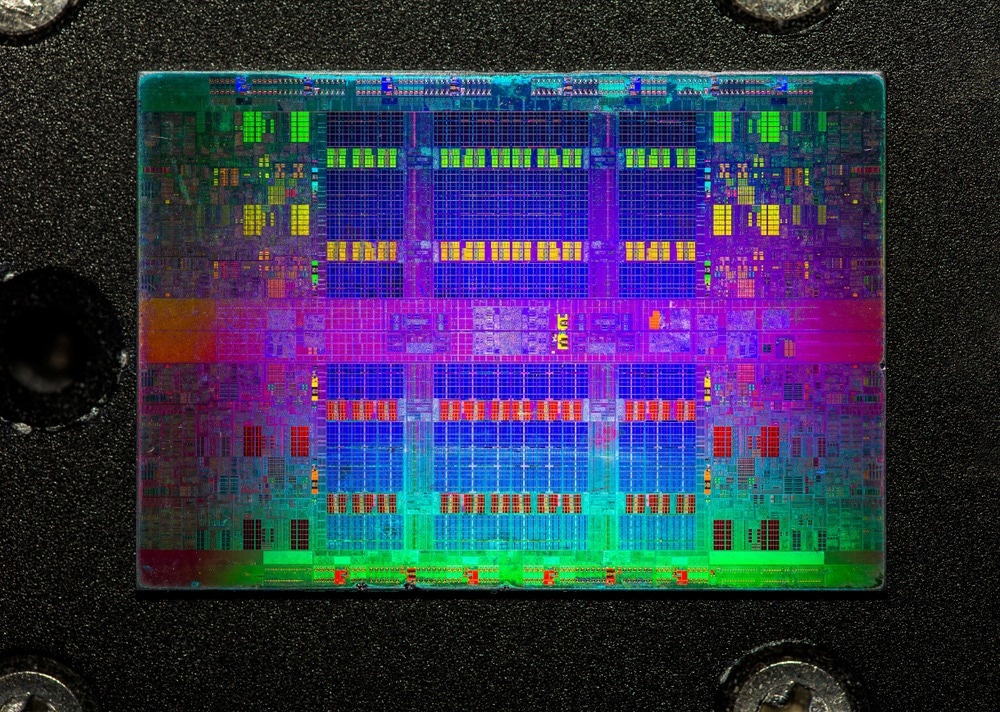
Image Credit: nanofabrication /Shutterstock.com
Currently, NIL is used to fabricate components for data storage, optoelectronic devices, nanophotonics, optical components, biosensors, and high-end semiconductor devices. To device manufacturers, defect control and avoidance are two of the key challenges that can help to improve product quality and yield.
Photolithography is the most widely used nanopatterning method in the semiconductor industry. However, as the characteristic dimensions of the electronic components go down to below 10 nm, the photolithography process exponentially becomes more complex and expensive. In the last two decades, a lot of research and development efforts have been directed at exploring alternative nanolithography methods capable of creating sub-10 nm patterns in a more accessible, cheaper, and faster way.
Unlike the optical lithographic techniques that create nanostructures through the interaction of photons or electrons with a thin polymer layer (called resist), NIL relies on direct mechanical deformation of the resist. As a result, the method can achieve resolutions beyond the diffraction limits encountered in the optical lithographic techniques.
How Does NIL Achieve Nanometer-Level Resolution?
The NIL method relies on the deformation of the resist layer using a template (made of quartz or silicon) engraved with the nanopattern that is being transferred. The resist material can be either thermoplastic or UV-curable polymer. Depending on the used resist material, the two main NIL processes are the thermo-mechanical NIL (usually referred to as just NIL) and the UV-NIL. In NIL, the resist layer is deposited on a substrate that is heated above the glass transition temperature of the resists. The template is brought into contact with the molten resist under some pressure and partially squeezes and deforms the resist layer. After lowering the resist temperature below its glass transition, the template and the substrate with the embossed resist layer are separated.
Alternatively, a liquid UV-curable polymer can be used as a resist, which is exposed to UV light after the template is brought into contact with the resist-coated substrate. After the curing of the resist, the template is released from the substrate.
In both cases, the direct contact between the template and the resist imprints (or replicates) the nanopattern without the need for expensive light sources and collimating optics required by the photolithographic methods. Besides, employing mechanical contact instead of light for pattern transfer means that extremely high resolution can be achieved, thus overcoming the limitations set by light diffraction or beam scattering encountered in photolithography. This simplifies the process and can reduce the final product's manufacturing cost.
Key Defects in the NIL Process
At the same time, the NIL process brings new challenges. The direct pattern transfer demands very high-quality templates to ensure high-fidelity pattern replication. The viscoelastic deformation of the resist requires careful consideration of the topography of the template and substrate and their chemical and mechanical properties. The interaction of the two materials impacts the resist deformation behavior and its separation from the template, affecting the pattern quality and throughput. While recent developments have overcome most of the challenges, NIL patterning defects remain one of the industry's biggest barriers to wider adoption of the NIL process.
In the NIL process, the defects can be divided into randomly distributed and repeated. Randomly distributed defects are not repeatable in terms of location, amount, and occurrence. These may result from foreign particles or air bubbles in the resist, incomplete template-substrate contact, and non-uniform residual resist after the separation. The repeated defects are usually related to imperfections of the template and substrate.
How the Defects Are Created?
The presence of a foreign particle that prevents the contact between the template and the resist layer creates a defect area much larger than the particle itself. Such defect includes the particle, some void surrounding the particle, and an area incompletely filled by the resist.
The dimension of the defect depends on the particle size and shape, the stiffness of the substrate and the template, the applied pressure, and the properties of the resist. Dispensing the liquid resist for UV-NIL also poses risks of trapping gas bubbles between the template and the substrate. Subsequently, the bubbles can create defects like those resulting from foreign particles.
Another type of void defect occurs when the template and the substrate are not perfectly flat and conformal. This can cause local excess or shortage of the resist, leading to an incomplete pattern transfer. In addition, the increased adhesion between the template and the resists can result in incomplete separation of the template, thus affecting the quality of the transferred pattern.
Inspecting and Eliminating Defects
Unlike the photolithographic process, where the photomask features are usually four times larger than the patterned features, NIL is a direct transfer process (features on the template have the same dimensions as the final pattern) that requires high-resolution inspection tools for the assessment of the templates and the replicated patterns.
Defect inspection is an indispensable part of any industrial lithographic process. Establishing an effective inspection methodology is of critical importance for understanding the mechanisms of defect formation. Various inspection methods have been developed based on existing commercial deep-UV inspection tools combined with metrological tools scanning probe microscopy and high-throughput electron beam inspection systems.
The insights provided by the surface characterization inspection methods enabled the scientist to develop effective strategies for defect minimization and elimination. Designing novel micro-and nano-fluidic systems that minimize ambient gas dissolution in the resist during the dispensing and embossing of the resist greatly reduces the number and size of the bubble-associated defects.
In-process interferometric measurements of the template deformation can optimize the contact pressure in real-time to achieve near-perfect conformal contact between the template and the substrate. The development of low-viscosity resists together with low-surface-energy coatings for the templates optimizes the adhesion between the template and the resists, thus improving the quality of the transferred pattern and increasing the template lifetime.
Developing strategies for eliminating imprint defects paves the way toward the wider use of NIL for the mass fabrication of novel nanodevices.
References and Further Reading
D. Li et al., (2017) A nanofluidics study on nanoscale gas bubble defects in dispensing-based nanoimprint lithography. IEEE 17th International Conference on Nanotechnology (IEEE-NANO), 788-791, Available at: https://doi.org/10.1109/NANO.2017.8117426
Lan, H., and Ding, Y., (2010). Nanoimprint Lithography. In (Ed.), Lithography. IntechOpen. Available at: https://doi.org/10.5772/8189
Chen, L. et al., (2005) Defect control in nanoimprint lithography. J. Vac. Sci. Technol. B: Microelectronics and Nanometer Structures Processing, Measurement, and Phenomena 23, 2933-2938 (2005). Available at: https://doi.org/10.1116/1.2130352
Disclaimer: The views expressed here are those of the author expressed in their private capacity and do not necessarily represent the views of AZoM.com Limited T/A AZoNetwork the owner and operator of this website. This disclaimer forms part of the Terms and conditions of use of this website.