Lithium-sulfur batteries are among the most promising successors of lithium-ion batteries. Based on the reversible redox reactions between lithium and sulfur, these next-generation devices have become some of the most investigated systems in academic and industrial settings.
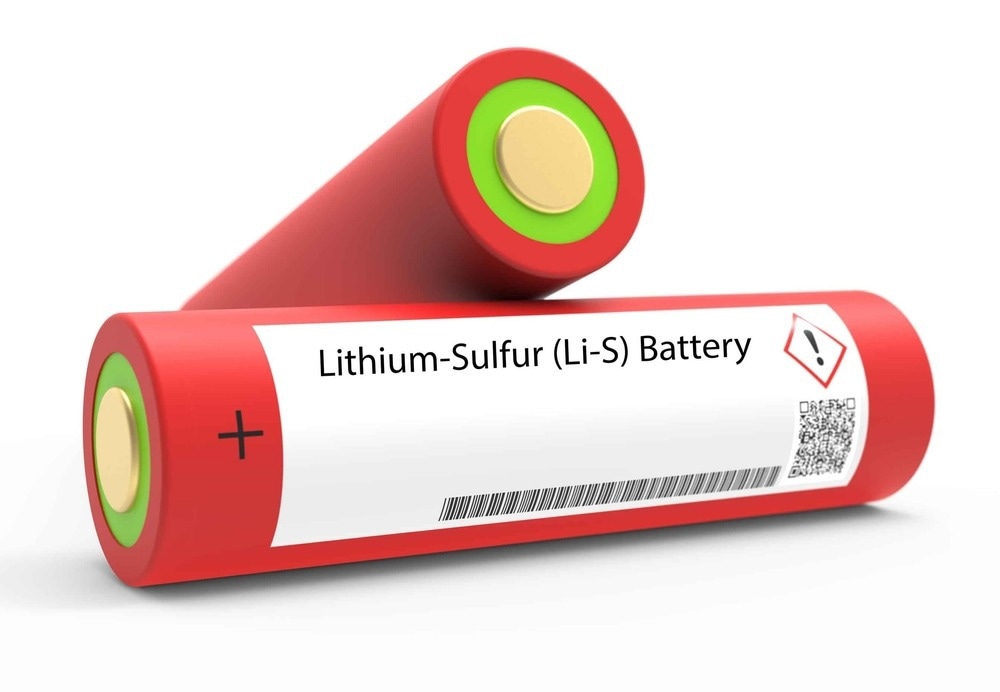
Image Credit: luchschenF/Shutterstock.com
Sulfur is a widely available, inexpensive, and environmentally friendly element. When paired with lithium metal, it can offer a high theoretical specific capacity of 1675 mA h g−1 – one of the highest among solid cathode materials. A lithium-sulfur battery can achieve an average cell voltage of 2.15 V, as well as presenting a much higher theoretical energy density (2500 W h kg−1) compared to their current lithium-ion precursors.
With sulfur replacing expensive transition metals (i.e., cobalt) and other toxic compounds, lithium-sulfur batteries could be a cheaper, lighter, and potentially safer technology. Although they have been known since the 1960s – when the concept of a sulfur cathode was first introduced – lithium-sulfur batteries have struggled to be commercialized due to several challenges, such as low cycle life and low practical energy density.
However, recent breakthroughs have reignited the interest of the scientific community, prompting significant research efforts within industry and academia. Some potential applications are in aviation (with drones and electric aircrafts) and grid energy storage.
Reaction Mechanism Inside a Lithium-Sulfur Battery
The basic components of a lithium-sulfur battery are a lithium metal anode, an organic liquid electrolyte, and a sulfur composite cathode. The mechanism is based on the reversible electrochemical redox conversion of elemental sulfur.
During the discharge process, the oxidation of the lithium metal at the anode releases lithium ions, producing electrons. Lithium and sulfur react to form long-chain polysulfides as intermediates, which are eventually converted into lithium sulfide (Li2S) at the cathode. The reverse reaction that takes place during the charging process oxidizes Li2S back to sulfur.
Despite seeming relatively simple, these electrochemical reactions are quite complex. In fact, during the discharge process, S8 is first lithiated to form soluble lithium polysulfides – Li2S8 first and Li2S6 and Li2S4 afterward. Upon further lithiation, Li2S4 is transformed into solid short chain sulfides (Li2S), precipitating on the electrode, leading to an average voltage of approximately 2.1 V.
During charging, the process is reverted, with lithium ions released into the electrolyte and Li2S reconverted into intermediate lithium polysulfides, followed by the formation of the original S8 product.
Thanks to its very low standard reduction potential (-3.04 V), lithium is an ideal negative electrode that possesses a low operating voltage and high specific capacity. Moreover, sulfur is a stable electronegative element that, when fully reduced to Li2S, can achieve a high theoretical capacity of 1672 mA h g−1. Nevertheless, the performance of lithium-sulfur batteries under practical conditions does not meet the theoretical expectations, with lower energy density and cycling stability.
Fabrication Methods
The manufacturing process of lithium-sulfur batteries is similar to the one for their lithium-ion analogs, where instead of cobalt oxide or nickel oxide, sulfur is used as the cathode material. The three main production stages are electrode manufacturing, cell assembly, and cell finishing.
Unfortunately, lithium-sulfur batteries present some challenges linked to poor capacity retention. This is due to a few factors, such as the shuttle effect (where the lithium polysulfide intermediates dissolve in the electrolyte and shuttle between the cathode and the anode), electronically insulating material, and low active material utilization.
To overcome these problems, several solutions have been explored, such as infusing sulfur particles into carbon, which creates an electron pathway in the sulfur network. The numerous types of carbon that can be used include mesoporous carbon, carbon nanotubes, graphene oxide and carbon fibers, each one with its own advantages and disadvantages.
Systems with a high loading of sulfur (>10 mg cm-2), require three-dimensional host materials as templates. Examples include carbon nanofiber or cellulose nanofibers. In particular, adding carbon nanofiber contributes to trapping the lithium polysulfides, mitigating the shuttle effect.
Furthermore, electrodes for some lithium-sulfur batteries can be prepared using water‐based processes, reducing the need for toxic solvents. A solvent-free dry‐transfer film process has also been developed, making the fabrication process more environmentally friendly.
Current Academic and Commercial Landscape of Lithium Sulfur Batteries
After going quiet for many decades, the interest in lithium-sulfur batteries was revived when a study in 2009 reported cells with a high discharge capacity and stable cycling over 20 cycles, thanks to mesoporous carbon as a host for sulfur.
Since then, research and development in the field have increased significantly, with substantial progress made in terms of cycle life and specific capacity. However, only a few organizations have managed to achieve lithium-sulfur battery technology at a technology readiness level (TRL) greater than 5.
LG Chem recently announced they co-developed with the Korea Aerospace Research Institute (KARI) a drone called EAV-3. The drone is powered by lithium-sulfur batteries with a specific energy of 410 W h kg−1 and expects to begin commercial production in 2025.
The Beijing Institute of Technology has reported a cell with a specific energy as high as 470 W h kg−1, while the Pacific Northwestern National Laboratory is working on a prototype that should bridge the gap between academic and industrial research.
The UK-based company OXIS Energy Ltd. is routinely producing high‐capacity (>15 Ah) pouch cells that exceed 400 W h kg−1 at a TRL of 7-8, and plans to expand its lithium-sulfur battery technology beyond its pilot‐scale to production capability for real‐world applications.
Despite the intensive research over the last few years and the major progress achieved, very often, the battery performance changes when moving from the lab to mass production. The transition from academic to commercial applications will still be problematic until the gaps between industrial production and academic research are filled in.
References and Further Reading
Chen, Y., et al. (2021). Advances in Lithium-Sulfur Batteries: From Academic Research to Commercial Viability. Advanced Materials, 33, e2003666.10.1002/adma.202003666. Available: https://www.ncbi.nlm.nih.gov/pubmed/34096100
Zhao, M., et al. (2020). A Perspective toward Practical Lithium-Sulfur Batteries. ACS Central Science, 6, pp.1095-1104.10.1021/acscentsci.0c00449. Available: https://www.ncbi.nlm.nih.gov/pubmed/32724844
Dorfler, S., et al. (2021). Recent Progress and Emerging Application Areas for Lithium-Sulfur Battery Technology. Energy Technology (Weinh), 9, 2000694.10.1002/ente.202000694. Available: https://www.ncbi.nlm.nih.gov/pubmed/33520596
Disclaimer: The views expressed here are those of the author expressed in their private capacity and do not necessarily represent the views of AZoM.com Limited T/A AZoNetwork the owner and operator of this website. This disclaimer forms part of the Terms and conditions of use of this website.