Feb 24 2009
EU-funded scientists have developed a simpler, cleaner method of producing hydrogen peroxide (H202), which is widely used as an antiseptic and disinfectant. The results could lead to the on-site production of hydrogen peroxide in smaller quantities and at weaker concentrations, thereby avoiding the risks associated with the transport and storage of large amounts of highly concentrated H2O2.
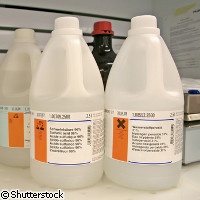
The work, which is published in the journal Science, was partly supported through the AURICAT ('Catalysis by gold') project, which was financed through the 'Improving human research potential and the socio-economic knowledge base' programme of the EU's Fifth Framework Programme (FP5).
Hydrogen peroxide, a powerful antiseptic and disinfectant, is one of the most widely used chemicals in the world. However, producing this important substance entails an energy-intensive process, and the economics of this process mean it is made in larger quantities and at stronger concentrations than are needed in most applications. As a result, large amounts of the chemical must be stored and transported; this can be hazardous, as the recent explosion of a lorry carrying hydrogen peroxide on a UK motorway showed.
Unsurprisingly, chemists have long sought a cleaner, simpler way of producing H2O2. Palladium has proved to be effective at catalysing the reaction in which hydrogen and oxygen combine to become hydrogen peroxide. However, as fast as the H2O2 is produced, the same catalyst drives the decomposition of the hydrogen peroxide to water.
In this latest study, UK and US scientists reveal that an alloy of palladium and gold nanoparticles catalyses the production of H2O2 but 'switches off' its decomposition into water.
'We found it was important for the palladium to incorporate just a small amount of gold,' explained Professor Christopher Kiely of Lehigh University in the US. 'The gold appears to modify the electronic structure and thus the catalytic activity of the palladium.'
The trick, according to the researchers, is to deposit these nanoparticles on a carbon support that has first been washed with nitric acid (HNO3). The acidic pre-treatment decreases the average size of the nanoparticles to between 2 and 25 nanometres (a nanometre is a billionth of a metre). These smaller particles are better able to block the decomposition reaction. Furthermore, washing the support with acid resulted in a better distribution of the nanoparticles on the support.
'We learned that neither the concentration of the nitric acid nor the length of time of the washing was important,' said Professor Kiely. 'What was important was to wash the support in nitric acid before putting the gold-palladium nanoparticles on it. The resulting change in particle size and distribution enables us to retain a lot more of the hydrogen peroxide and to make the direct process more economically viable.'
The researchers believe that with further development, their technique could be used to 'underpin the generation of H2O2 at the 3% to 8% concentration levels required in most chemical applications'.
Crucially, the process could allow users of hydrogen peroxide to produce the chemical on site in the quantities required, thereby preventing the need to store and transport large volumes of the substance.
Professor Kiely has been working closely with Graham Hutchings of Cardiff University in the UK on the use of gold nanoparticles as catalysts for 15 years. Three years ago they found that gold-palladium nanoparticles can be used to convert primary alcohols to aldehydes, an important reaction in the production of spices and perfumes, in a more environmentally friendly way.
Source: Cordis