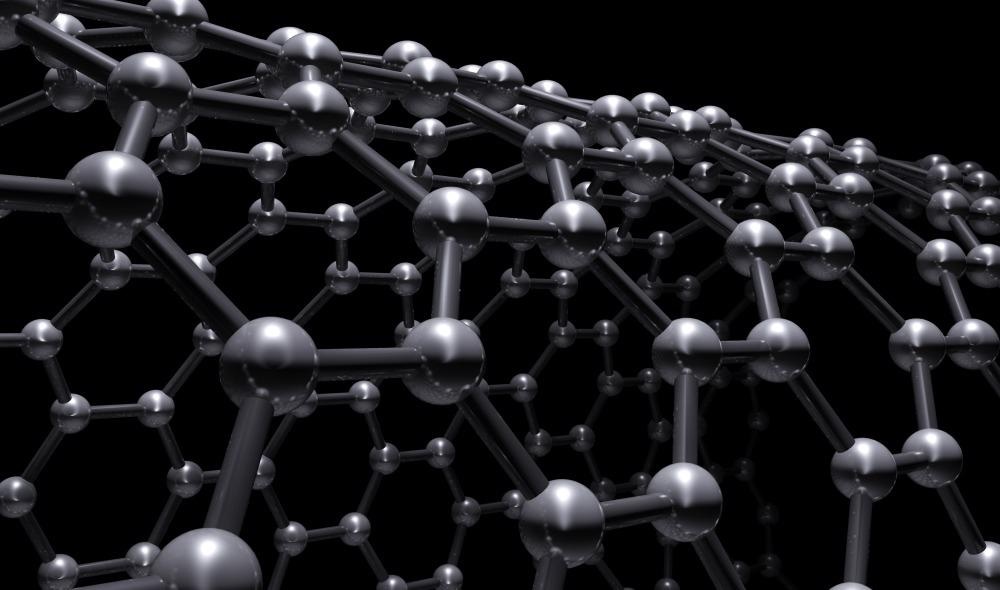
Image Credit: Evannovostro/Shutterstock.com
Carbon nanotubes (CNT) and graphene represent two of the most striking functional materials. Due to their outstanding mechanical, electrical, and thermal properties, these one- and two-dimensional carbon nanostructures have diverse applications in consumer electronics, composite materials, energy storage media, and field emission semiconducting devices.
Despite the rapid developments in the synthesis of low-dimensional materials in recent years, large-scale production of high-quality CNTs remains challenging, mainly due to poor yield and undesirable material quality variations. Recently, a group of Swedish researchers from the Chalmers University of Technology in Göteborg developed a high-temperature treatment method that allows the fabrication of CNTs with increased crystallinity and more consistent mechanical properties.
Rolled-Up Monoatomic Sheets of Carbon
CNTs consist of graphene sheets (a single layer of carbon atoms arranged in a two-dimensional hexagonal lattice) rolled up into long, hollow cylindrical structures, sometimes closed at the two ends by caps.
CNTs can either be single-walled structures (SWCNTs) or have walls composed of multiple layers, called multi-walled carbon nanotubes (MWCNTs). The unique properties of CNTs, such as low-cost, lightweight, high aspect ratios and surface area, distinct optical characteristics, high thermal and electrical conductivity, and high mechanical strength, make them suitable for a wide range of applications in microelectronics, biomedical sensing, and engineering materials.
Chemically Bonded Graphene–CNT Nanostructures
As a unique type of CNT, the vertically aligned substrate-bound CNTs (VACNTs) possess the extraordinary nanoscale mechanical, electrical, and thermal properties of the individual CNTs, but present them in a hierarchical and anisotropic morphology.
VACNT arrays can bond covalently to a graphene or graphite substrate, thus creating a seamless hybrid material. The nanotubes' unidirectional alignment, their uniform length, and the large surface area open up prospects for advanced application in supercapacitors, separation membranes, advanced fabrics, black-body-like energy absorbers, ultra-sensitive optical sensors, thermal transfer materials, and many others.
Large-scale synthesis of VACNTs is generally carried out by the chemical vapor deposition (CVD) process. This method involves the decomposition of hydrocarbons at a particular temperature and pressure in the presence of carefully controlled amounts of catalysts. The catalysts are either transition metals (like iron or nickel) or decomposition products of organometallic complexes (for example ferrocene).
Although the substrate-immobilized catalyst helps to synthesize well-aligned VACNTs with controlled diameter and lengths of up to several millimeters, the metallic particles remain in the final product as an impurity. As a result of this, as-synthesized VACNTs contain metal catalysts as impurities.
The presence of catalyst impurities at the bottom of the VACNT array, between CNTs and substrate, severely limits the array's electrical and thermal conductivity. In addition to the residual metal catalysts, the as-synthesized VACNTs also contain other carbonaceous impurities such as amorphous carbon.
Impurities and Defects Deteriorate CNT Properties
Removal of the impurities and establishing covalent bonding between the CNT array and the underlying graphene or graphite substrate is essential for optimal performance in any advanced applications.
Traditionally, post-growth purification of CNTs is performed in a two-step process. The initial step involves selective oxidation of the raw CNTs (containing metal impurities and amorphous carbon) at approximately 450 °C in the air to remove the amorphous carbon. During this step, the amorphous carbon will be selectively oxidized and removed as CO2 (since the amorphous carbon is more reactive than CNTs). In the second step, the residual metallic impurities are refluxed and dissolved in strong acids. However, a significant drawback of this two-step purification is that strong acids can induce structural degradation of the CNTs.
High-Temperature Treatment as an Alternative to Chemical Processing
To overcome the problem of structural damage to the CNTs by the traditional methods for removal of impurities and defects, a research group at the Chalmers University of Technology in Göteborg (Sweden) led by Professor Johan Liu developed a thermal treatment method that significantly improves the mechanical, electrical and thermal properties of VACNT arrays by reducing the defects and increasing the crystallinity of the CNTs.
Previous studies have established that post-growth heat treatment of CNTs can be effective at removing impurities and structural defects. Chemical impurities can be eliminated at around 1200 °C, while temperatures above 2500 °C in an inert atmosphere are required to remove defects in the atomic structure of the CNTs.
Since most substrates are incompatible with such high temperatures, heat treatment is usually applicable only for freestanding arrays or randomly aligned CNTs.
Professor Liu and his team used a thin graphite fold as a substrate and a combination of aluminum oxide (Al2O3) and iron as a catalyst to create a VACNT array that could be subjected to an extremely high temperature of 3000 °C in an inert atmosphere.
Elimination of Residual Catalyst
This temperature is above the boiling temperature of both the Al2O3 and Fe, causing complete evaporation of the catalyst material. Investigating the VACNT array's elemental composition by x-ray photoelectron spectroscopy (XPS) revealed that, after the high-temperature annealing, the XPS spectrum was nearly identical to a pure graphite spectrum.
There were no detectable traces from either aluminum or iron, indicating that the annealing process has eliminated the remains of the CVD catalyst. The annealing process reduced the overall oxygen content from 5.23% to 0.27%, meaning that the oxygen has been mostly eliminated both in the alumina of the catalyst layer and from oxidized groups on the individual CNTs.
Enhanced Structural Order and Crystallinity for Improved Mechanical Strength
The researchers employed Raman spectroscopy and transmission electron microscopy (TEM) to study the crystallinity and number of defects in the CNT arrays. The Raman spectra indicated a significant reduction of defects within the CNTs structure and a corresponding increase of 50% in the overall crystallinity (confirmed by TEM diffraction measurements).
Professor Liu estimated that such an increase in crystallinity corresponds to a 124% increase in Young’s modulus of the material and expects similar improvements in thermal and electrical properties.
The Swedish scientists envisage that the novel heat treatment method will allow synthesizing higher quality VACNT arrays to manufacture advanced graphene/graphite-CNT hybrid materials with unique thermal, electrical, and mechanical properties.
References and Further Reading
J. Hansson, et al., (2020) Effects of high temperature treatment of carbon nanotube arrays on graphite: increased crystallinity, anchoring and inter-tube bonding. Nanotechnology, 31, 455708 Available at: https://doi.org/10.1088/1361-6528/ab9677
X. Tang, et al., (2020) Vertically Aligned Carbon Nanotube Microbundle Arrays for Field-Emission Applications. ACS Appl. Nano Mater., 3, 7659−7667. Available at: https://dx.doi.org/10.1021/acsanm.0c01280
I. Spikanth, et al., (2016) Effect of high-temperature heat treatment duration on the purity and microstructure of MWCNTs. Bull. Mater. Sci., 39, 41–46. Available at: https://doi.org/10.1007/s12034-015-0891-2
C. S. Rout, et al., (2012) Synthesis of chemically bonded CNT–graphene heterostructure arrays. RSC Adv., 2, 8250-8253. Available at: https://doi.org/10.1039/C2RA21443A
J. Sengupta (2016) Carbon Nanotube Fabrication at Industrial Scale: Opportunities and Challenges, in Handbook of Nanomaterials for Industrial Applications, pp 172-194, C. M. Hussain (Ed.), Elsevier Inc. Available at: https://doi.org/10.1016/B978-0-12-813351-4.00010-9
Disclaimer: The views expressed here are those of the author expressed in their private capacity and do not necessarily represent the views of AZoM.com Limited T/A AZoNetwork the owner and operator of this website. This disclaimer forms part of the Terms and conditions of use of this website.