Trying to find the optimal location to construct a laboratory is no easy task. Many environmental factors, such as temperature and humidity, can influence measurement stability and drifts, and changes in environmental conditions can necessitate instrument retuning and alignment.
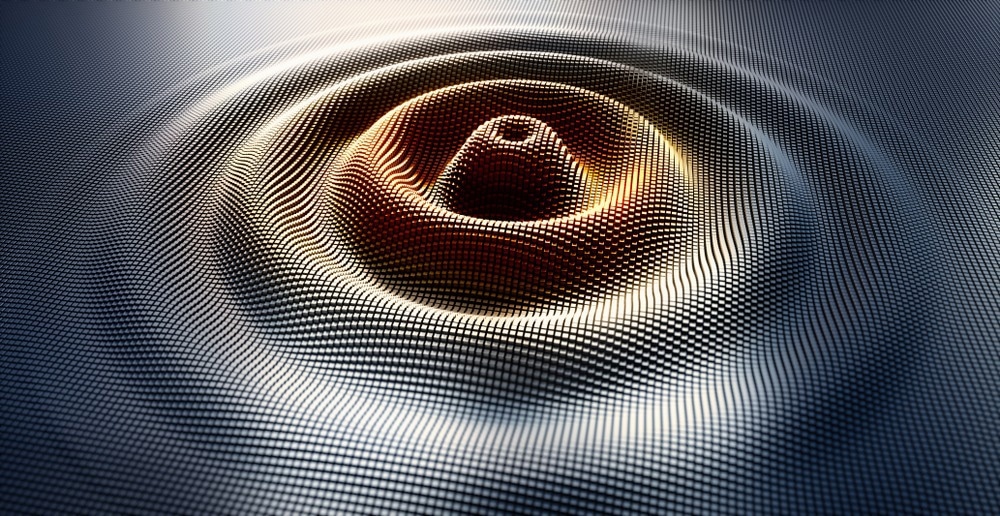
Image Credit: peterschreiber.media/Shutterstock.com
One problem for many laboratory environments is vibrations. Many laboratories, particularly those that perform metrological measurements and need extreme stability conditions, are built in remote locations to minimize environmental vibrational instabilities. Others make use of building engineering and the use of either active or passively stabilized optical tables to try and minimize vibrational interference.1
Often, building laboratories in geographically isolated areas or engineering rooms to house sensitive equipment is not always practical or feasible, so damping blocks and stabilization equipment become increasingly important. One recent example of such work is for the electron microscope at Cardiff University’s Cardiff Catalysis Institute’s (CCI) Electron Microscopy Facility, which is located near both a freight train line and a busy road network that are both in continual use.2
Stabilizing the microscope system involved installing an air spring-suspended inertial base with a total mass of 10500 kg that could help dampen all the sub 10 Hz frequencies that the microscope was particularly susceptible to. There was also tuning of the block required to minimize any cross talk and, as electron microscopes are susceptible to influence from stray magnetic fields as well as vibrational instabilities, the block had to be integrated into the magnetic shielding of the room as well.
The weight of the block and the even heavier microscope meant custom engineering was required to create a solution that would fit with the architecture of the room and would consider any constraints of the space and local environment.
Overall though, it was possible to achieve sufficient levels of vibrational isolation that the electron microscope could continue to operate despite the perturbations in the environment.
Electron Microscopy
Electron microscopy is used in many different areas of science, including nanotechnology and the life sciences, owing to its outstanding spatial resolution. Sub-Angstrom to even nanometer scale spatial resolutions are achievable, as is the imaging of single particles on surfaces or in other environments.3
The high level of spatial resolution achievable makes it possible to resolve the spatial features of nanoscale devices in full detail.4 Electron microscopy is one of the few methods that can be used for sizing the smallest nanoparticles or directly imaging small viral species.5
While the outstanding spatial resolution is a boon for the types of systems and scientific problems that can be studied with electron microscopy, it also poses several technical challenges for the method. There are two main geometries for performing electron microscopy experiments – either in transmission mode, where the electron beam is transmitted through the sample and detected directly, or in scanning electron mode, where secondary electrons are detected using an off-axis configuration.
In scanning and transmission electron microscopy, the electron beam is rastered over the sample to build up the full image of the sample area. There are several challenges with the rastering process – one, it can be very slow to scan large area samples with a very tightly focused electron beam.
Two, it requires very high precision motors and translation stages to not introduce aberrations and pointing issues from incorrect recognition of the beam positions and finally, the movement and movement recognition are sensitive to vibrational instabilities.
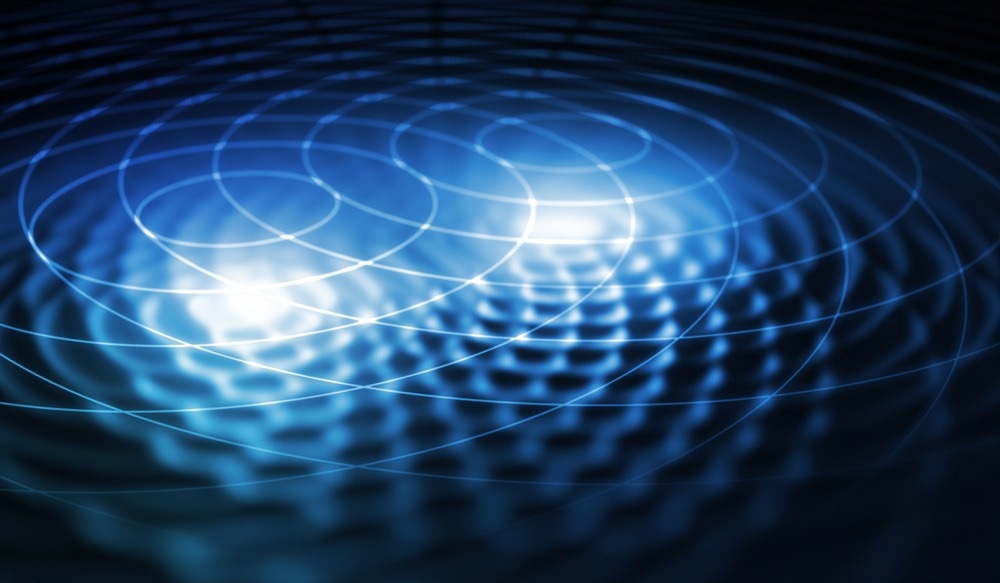
Image Credit: Andrey VP/Shutterstock.com
Vibrational Sensitivity
The focal spot size of the electron beam is one factor in the overall spatial resolution of the electron microscope. With some electron beams being only tens of nanometers in size, any small vibrational instability can cause blurring of the image and reduce the effective spatial resolution.
While electron microscopes are typically very large instruments, often weighing around half a ton, this alone is not sufficient to suppress the types of vibrational noise that can be found in all buildings and from more perturbing events such as heavy freight passing by.
Acquiring full images can take many hours when large area samples are being measured at very high resolution. Installing problems can also add up to create longer-term drifts in the sample measurement.6
Normally, an electron microscopy image will be reconstructed by using the measured motor positions for the electron beam position alongside the images recorded at this position. Images can then be ‘stitched’ together to create the full reconstructed image.
There are many attempts to improve scanning speeds and effective resolution by finding ways to correct various scan noises that can arise during the electron microscopy measurement.6 This includes correcting for acoustic and mechanical drifts as well as correcting for electromagnetic interference.
Achieving atomic level resolution often means that the vibrations need to be corrected for, as over time, the correlation between the measured beam position and the real beam position can be lost due to the uncertainties from the vibrational disturbance.
While post-processing of images is one way to correct for vibrational instabilities, it is often better to use the design of the laboratory or the use of additional damping equipment to remove these contributions to the image noise in the first place.
References and Further Reading
Trummer, D. J., Foley, R. J., & Shaw, G. S. (1999, July). Stability of optical elements in the NIF target area building. In Third International Conference on Solid State Lasers for Application to Inertial Confinement Fusion (Vol. 3492, pp. 363-371). SPIE. https://doi.org/10.1117/12.354148
Mason UK (2022) Can you operate a microscope next to a freight train?, https://www.labbulletin.com/articles/can-you-operate-electron-microscope-next-freight-train, accessed November 2022
Zhang, N. F., Postek, M. T., Larrabee, R. D., Vladár, A. E., Keery, W. J., & Jones, S. N. (1999). Image sharpness measurement in the scanning electron microscope - Part III. Scanning, 21(4), 246–252. https://doi.org/10.1002/sca.4950210404
Li, Y., Huang, W., Li, Y., Chiu, W., & Cui, Y. (2020). Opportunities for Cryogenic Electron Microscopy in Materials Science and Nanoscience. ACS Nano, 14(8), 9263–9276. https://doi.org/10.1021/acsnano.0c05020
Stewart, P. L. (2016). Cryo‐electron microscopy and cryo‐electron tomography of nanoparticles.pdf. WIREs Nanomed Nanobiotechnol, 9, e1417. https://doi.org/doi: 10.1002/wnan.1417
Jones, L., & Nellist, P. D. (2013). Identifying and Correcting Scan Noise and Drift in the Scanning Transmission Electron Microscope. Microscopy and Microanalysis, 19, 1050–1060. https://doi.org/10.1017/S1431927613001402
Disclaimer: The views expressed here are those of the author expressed in their private capacity and do not necessarily represent the views of AZoM.com Limited T/A AZoNetwork the owner and operator of this website. This disclaimer forms part of the Terms and conditions of use of this website.