Since its first successful isolation in 2004, graphene has undergone many evolutionary steps and inspired a plethora of applications ranging from electronics to life science. Graphene is typically synthesized using chemical vapor deposition.
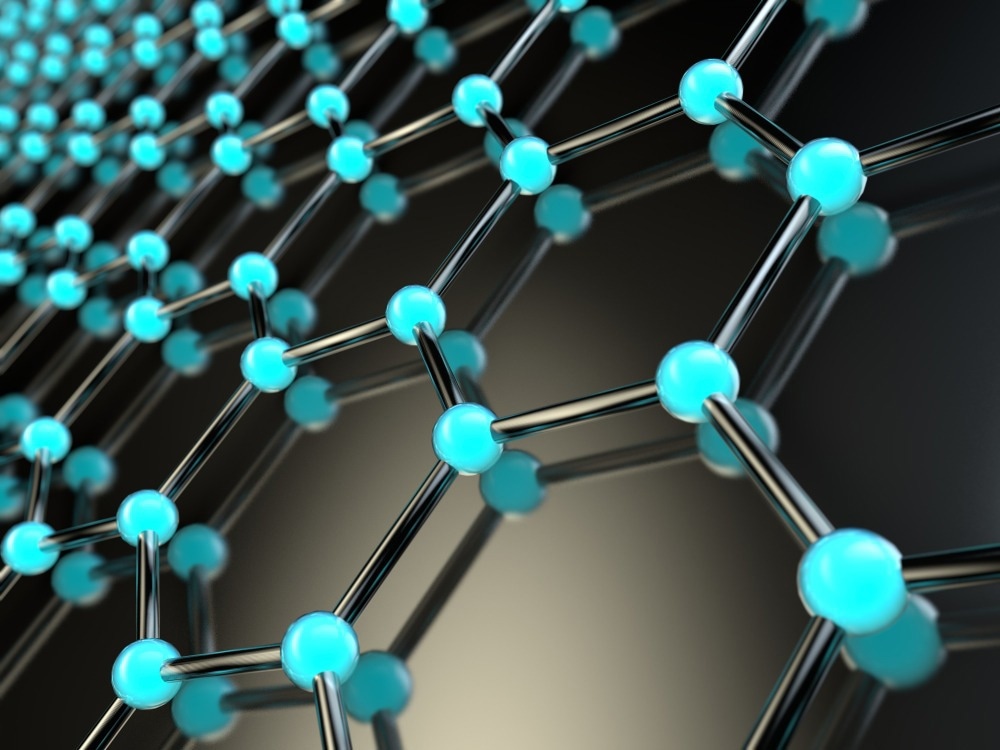
Image Credit: 3DStach/Shutterstock.com
However, the problem with CVD is that it requires a costly hot reactor (around 1000 °C) and a controlled environment to produce high-quality graphene. As a result, cost-effective graphene synthesis and patterning have proven difficult in electronic and energy storage devices. This article aims to shed more light on laser-induced graphene (LIG) technology and how it can produce graphene suitable for electronic applications.
Introduction: History and Properties
In 2014, Prof. James Tour and his research team from Rice University developed a scalable method for manufacturing and designing porous 3D multilayer graphene foam with high conductivity from a cheap polymer (in this case, polyimide) by burning it with a computer-controlled laser. The technique operates in ambient air at room temperature, eliminating the need for hot furnaces and regulated settings.
The resulting porous graphene is known as laser-induced graphene (LIG). The laser does not completely penetrate the foam, so it remains linked to a plastic substrate. Factors such as the type of laser and fabrication parameters affect the composition and morphology of LIG, which in turn affects its mechanical, electrical, and surface properties.
The laser-induced graphene produced by this process was not the usual 2D graphene sheet whose carbon atoms are organized in a hexagonal ring, but rather a porous 3D form of interconnected graphene flakes with five-, six-, and seven-atom rings and a thickness of approximately 20 microns. Typically, paired five- and seven-atom rings are considered defects; however, they are not a defect in this instance.
Instead, this unique defect structure traps electrons and increases its ability to store charges. Additionally, five-and-seven formations make the resulting LIG metallic. The LIG is not as conductive as copper but sufficiently conductive for numerous applications, including wearable electronics and energy storage.
Recent Progress
In 2017, as an extension of producing LIG on polymer surfaces, the Rice University team patterned LIG on the surface of pine wood, transforming it into an electrical conductor that might be utilized in biodegradable electronics.
Later in 2018, the Rice team studied the application of LIG patterned on food, paper, fabric, cardboard, and even toast. In the future, this study may make it possible to rapidly install conductive identification tags and sensors on the food itself, providing information on where it has been, how long it has been stored, and its country and city of origin. LIG tags could also be sensors that detect microorganisms on food and send a signal indicating whether food has gone bad.
Practical Advancements
Researchers developed micro-supercapacitors with LIG electrodes in a single step for practical testing. Comparable to other carbon-based microsupercapacitors, the LIG microsupercapacitor exhibited capacitance of more than four mF/cm2 and power density of roughly nine mW/cm2, as well as little deterioration after up to 9,000 charge/discharge cycles. This capacitance is enough for cost-effective wearable electronics such as fitness watches.
LIG can be patterned into target materials and employed as an electrocatalyst for fuel cells, biological sensors and radio-frequency identification (RFID) tags, among other uses. Wearable electronics may be an early application of the technique for incorporating conductive traces into textiles. The LIG patterned on wood has been reported for the use of electrochemical splitting water for the production of hydrogen and oxygen.
In this study, researchers have deposited layers of cobalt and phosphorus or nickel and iron on LIG to create a pair of electrocatalysts with large surface areas that proved to be effective and robust.
The only limitation of LIG is the structure is not mechanically robust. However, it is possible to produce composites with increased mechanical strength by infusing LIG with plastic, rubber, cement, wax, or other substances. These novel materials could be utilized in flexible apparel, superhydrophobic surfaces, and antimicrobial coatings. Composites constructed with LIG are the best at retaining the structure of LIG flakes. Thus, the material could also be utilized as a deicing or anti-icing coating, as a flexible heating pad for healing injuries, or in on-demand heating clothing.
Looking Ahead to the Future
The main benefit of technology is that it allows you to pattern various desired geometries on all possible materials directly in LIG, without the need for a controlled atmosphere or other intricate ways in a most cost-effective way. This finding will prompt researchers to consider how natural materials could be improved through engineering.
References and Further Reading
Lin, Jian, et al. (2014). Laser-induced porous graphene films from commercial polymers. Nature communications. Availabe at: https://www.nature.com/articles/ncomms6714
Graphene on toast, anyone? (2018). Available at: https://news2.rice.edu/2018/02/13/graphene-on-toast-anyone-2/
Defects are perfect in laser induced graphene (2014). Availabe at: https://news2.rice.edu/2014/12/10/defects-are-perfect-in-laser-induced-graphene/
Laser-induced graphene gets tough, with help (2019). Availabe at: https://news2.rice.edu/2019/02/12/laser-induced-graphene-gets-tough-with-help-2/
Need graphene? Grab a saw (2017). Availabe at: https://news2.rice.edu/2017/07/31/need-graphene-grab-a-saw-2/
Disclaimer: The views expressed here are those of the author expressed in their private capacity and do not necessarily represent the views of AZoM.com Limited T/A AZoNetwork the owner and operator of this website. This disclaimer forms part of the Terms and conditions of use of this website.